Plastic components feature excellent flexibility in production processes, making them a popular choice in many industries. Manufacturers can create components that meet clients’ exact requirements and specifications, benefiting many industries.
However, choosing a manufacturing partner with state-of-the-art processes in rapid prototyping and mass production of plastic components in a wide range of materials and designs is a critical consideration.
This post examines the industries relying on plastic injection molding for rapid prototyping and low-, medium-, or high-volume manufacturing projects.
Consumer Goods
Plastic injection molding is an ideal manufacturing process for the development and manufacture of toys, plumbing fittings, and household items. Materials like polyethylene terephthalate are incompatible with machining processes like CNC cutting and milling, requiring a different manufacturing approach.
Fittings and parts used in joint sealing require injection molding to ensure tight tolerances, making plastic injection molding the ideal production process for these components.
Plastic injection molding offers high-volume production capability for producing thousands of items relatively quickly, making it ideal for large-scale production of consumer goods.
Automotive & Aerospace
The automotive and aerospace industries use components made with specialist materials requiring high repeatability and accuracy.
Plastic injection molding offers fast and effective manufacturing of lightweight, durable aerospace and automotive components that are compliant with safety regulations for streamlined production.
Additionally, 3D modeling and prototyping methods can test the efficacy of plastic parts, ensuring precise planning and design to client requirements.
Electronics
Electronics companies utilize plastic injection molding to produce housings and casings that are resistant to moisture and dust, protecting sensitive components inside the devices.
Plastic injection molding offers parts with excellent protection and durability, ensuring optimal performance of these electronic products.
Additionally, specialized molding techniques for plastic components used in electronic devices enable companies to use precise design of components for devices, meeting design specifications for excellent repeatability for quality control purposes.
Telecommunications
Plastic injection molding offers excellent, repeatable, large-scale production of many components used in conventional switching and relay components.
It’s effective for manufacturing specialized parts used in fiber optic and mobile communications technology for data transfer.
Injection molding techniques are critical in producing these parts, offering consistency and quality in high-volume applications.
Medical & Pharmaceuticals
The pharmaceutical and medical industries have incredibly stringent quality policies for producing devices and sundries used in hospitals and private practices.
Precision is a huge factor in the manufacturing of pharmaceutical products, including X-ray and MRI components, testing kits, and more.
Plastic injection molding allows the production of components in various specialist materials with excellent strength properties and many colors.
The process offers a high degree of design flexibility, making it capable of producing parts for innovative technological developments in the industry.
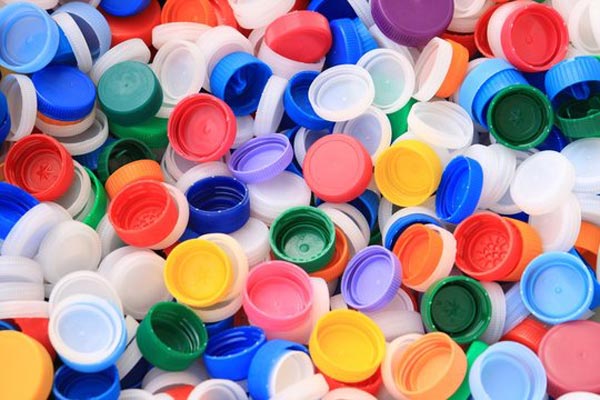
Plastic lids
Packaging
Tubes, lids, jars, bottles, and caps are just a few examples of products manufactured through plastic injection molding for the packaging industry.
The process allows for the use of many additives and resins to create cost-effective, versatile packaging solutions to suit many applications.
The plastic materials used in packaging are limitless in styles, shapes, textures, and colors, making injection molding the preferred manufacturing technique for this industry.
The versatility of plastic resins makes them ideal for creating custom products that meet the requirements for chemical and heat resistance, UV tolerance, and impact resistance required in packaging products during transportation and storage.
Food & Beverage
The food and beverage industry has tight safety and quality regulations regarding products utilized in all applications.
The FDA ensures food safety and requires manufacturers to maintain compliance with certain standards, such as BPA-free plastics.
Food containers, beverage over caps, conveyor systems, and filtering components are all examples of products manufacturing with plastic injection molding techniques.
The highly customizable nature of the plastic injection molding process concerning material selection makes it ideal for this industry.
Construction
Plastic injection molding can create components for frames, adaptors, and casings, which are required to house electrical components used in construction projects.
These housings protect the components from damage caused by water, dust, and other environmental and corrosive elements, increasing service life.
Plastic components used in the construction industry have excellent load resistance and good temperature resistance in environments where temperatures vary widely between the seasons.
Plastic injection molding can produce molded fasteners, window frames, and support struts to lower production and project costs.
Wrapping Up – Choose the Right Partner with Industry Experience
The plastic injection molding industry features thousands of manufacturing partners ready to take on your project. However, it’s critical to choose a partner who meets your project requirements.
Your preferred manufacturing partner should have a good understanding of your industry and its compliance and regulatory requirements.
The manufacturer must offer dependable processes and have excellent materials knowledge to assist in selecting the right plants for your manufacturing project.
Design, engineering, and manufacturing effective plastic injection molded components rely heavily on selecting the right manufacturing partner and may make the difference between project success and failure.