Pins of an ejector are crucial in making parts or items. These items are indispensable equipment of the launch framework in mold. These items also help in deciding the ultimate result of items in an injection molding procedure. Injection molding could be a fabricating preparation that includes infusing liquid plastic in a metal shape to accept the shape of the shape. Hence, pins of an ejector in injection molding include the expulsion of finished designs from the die structures. The metal form is designed from two unique materials such as B and A areas. During cooling of the liquid fabric within the shape, all sides of the metal shape remain isolated to permit the evacuation of the strong plastic. Infusion molds come in such a way that when they are opened, the A-side half is lifted, clearing out the shaped portion and the B portion. Pins of an ejector are found on the side of the B area half of the structure. It’s from this area these items move the shaped portion out of control.
Creating Ejector Pins Uniform Surface Thickness with Injection Molding:
If a liquid fabric is put inside a shape with uniform divider thickness, it streams openly without confinement. It fills the wall’s depth and expecting its characterized shape. Non-uniform shape dividers will result in the cooling of the more slender area of the liquid fabric. Hence, as the thicker segment cools, it’ll result in the contracting of the fabric, stretch concentration, and in the long run splitting amid expulsion. By the by, in case your plan does not permit uniform divider thickness, it can be helped by coring and including gussets. Coring could be a preparation for evacuating the liquid plastic from the wide zone to guarantee consistency along the divider. Gussets are back structures that you include to the divider as fortifications to decrease the wall’s thickness.
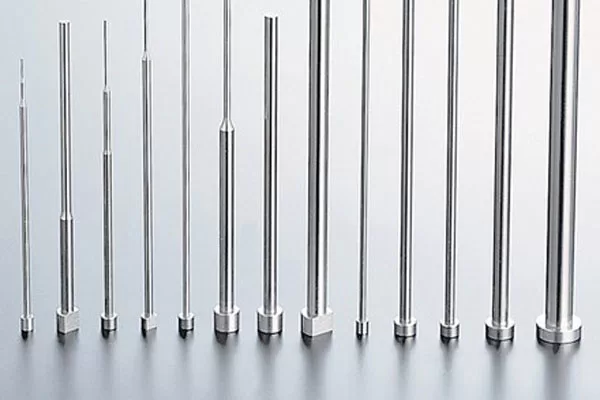
Customized nitrided ejector pins
Black Injection Molding for Ejector Pins:
Producers created these ejector pins since of the failure of the Nitride H13 pins to be utilized in working temperatures over six hundred degrees. The dark ejector stick is coated with a dark surface treatment which permits it to be self-lubricating and withstand tall temperatures up to one thousand degrees. It is a costly ejector stick and is appropriate for a metal launch framework in shape for automobiles.
Using Injection Molding to Design Draft Angles:
Draft point could be an incline in shape that’s connected to both sides of an injection molding. This slight mutilation within the shape of the shape permits for the easy expulsion of the plastic from the shape. The draft shape must be displayed to supply resistance against grinding whereas evacuating the portion from the form. Permitting more draft points would guarantee the simple discharge of parts from the discharge framework in shape. The nonappearance of draft points would result in expansive ejector stick marks on the portion amid evacuation and rub on the divider of the form.
Using Injection Molding to Minimize Undercuts:
Undermines are jutting highlights within the shape plan that deter the expulsion of either side of the form. Undermines are fundamental and unavoidable in a form plan as they avoid the portion from coordinate discharge from the shape. Be that as it may, undermines can be helped by making interlocks or locks that permit for simple evacuation or gathering. As much as conceivable, the planning group must keep the number of undermines in a launch framework in the form at a minimum.