Toys have always been a popular product for injection molding and we will discover why this is the case and what you can do to ensure a successful project, every time.
Toys are big business, however, due to the target market and health and safety concerns, it is important to ensure that in order to both make a profit and create a safe and sustainable product, they are made to exacting requirements every time. To achieve this, it is imperative that the initial design is safe for use by children, with no sharp edges, or removable parts that could be swallowed by small children. It is also essential to think about the materials and paints used, due to the likelihood that a child will put the toy in its mouth during play, so this must not contain any harmful substances such as lead.
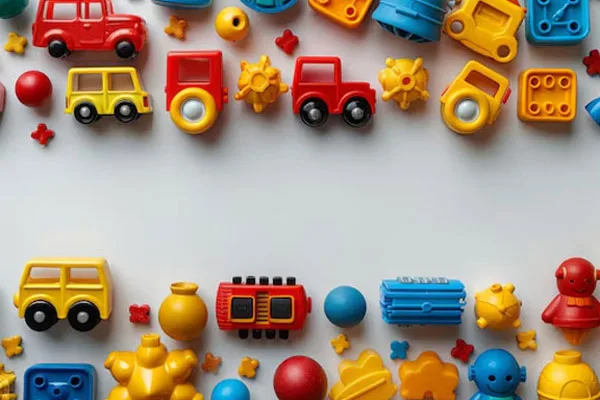
Plastic toys
Once the design has been assessed as safe and worthy of production, financial and commercial concerns come into play. When producing toys, it is usually the case that a family mold is used, which is able to lower the cost of production and produce multiple parts out of the same mold. This is important, as the cost price per piece is usually fairly low in relation to mass produced toys and so costs must be low in order for profit to be enjoyed by the manufacturer and seller.
Toys which are produced for younger children are usually fairly simple and colourful designs, manufactured from high-impact plastic materials such as ABS. It is inevitable that toys will be subject to a lot of user abuse and this must be taken into account during design in order to reduce breakages and returns. It is also very important to ensure that colourful plastics match and blend with each other – strict adherence to colour mix ratios will ensure that this is the case and the product is as cosmetically pleasing as possible.
NICE Rapid are experts in ensuring your next project is a success. Please do not hesitate to contact us to discuss your plans with one of our knowledgeable and friendly engineers.