The global struggle against plastic pollution has taken great strides in the past few years. But with more than 8 million tons of plastic waste entering the oceans every year, the environmental and ecological consequences are dire.
Amid this crisis, injection molding technology is emerging as a key player in transforming ocean waste into valuable, sustainable products. Let’s explore how injection molding can be part of the solution to plastic pollution while promoting sustainability.
What Is Injection Molding?
Injection molding is a versatile manufacturing process used to produce parts by injecting molten material into a mold. Used across industries such as automotive, consumer goods, and medical devices, the reasons this method is highly valued include precision, efficiency, and the ability to create complex designs.
Virgin plastic has been the traditional route for injection molding. Still, with growing awareness of environmental issues, the focus has shifted to incorporate recycled plastics, including those harvested from the oceans.
The Problem with Ocean Plastic Pollution
Ocean plastic pollution is a complex problem with far-reaching implications:
- Harm to Marine Life: Marine creatures often ingest or get entangled in plastic debris.
- Ecosystem Disruption: Plastics break down into microplastics, infiltrating the food chain and causing unknown long-term effects.
- Economic Costs: The cleanup and ecological damage caused by plastic pollution amount to billions of dollars annually.
Recycling ocean plastics offers a dual benefit: it reduces pollution while providing raw materials for manufacturing. Injection molding serves as a revolutionary solution that transforms the production process.
How Injection Molding Supports Sustainability
Utilizing Recycled Ocean Plastics
Injection molding allows recycled ocean plastics to be incorporated into new products without any visible difference. These materials are collected, cleaned, and processed into pellets suitable for molding. Replacing virgin plastic with recycled alternatives reduces manufacturers’ carbon footprints and supports a circular economy.
Energy Efficiency
Modern injection molding machines are designed to be energy-efficient, consuming less power during production. Combined with the use of recycled plastics, this approach minimizes environmental impact without compromising on product quality.
Scalability and Versatility
Injection molding’s adaptability makes it ideal for producing a wide range of products, from consumer electronics to packaging. This scalability ensures that recycled ocean plastics can be utilized in various industries, maximizing their impact on sustainability efforts.
Examples of Products Made with Recycled Ocean Plastics
Several innovative companies are already leveraging injection molding to create products from recycled ocean plastics, such as:
- Footwear and Apparel: Brands use injection molding to craft durable shoe soles and accessories.
- Household Goods: Items like furniture, containers, and even phone cases are being made from recycled materials.
- Automotive Parts: Recycled plastics are molded into car interiors, demonstrating their potential in industrial applications.
- Surfboards: Some surfboard manufacturers have started using recycled ocean plastics in their boards, showcasing the potential for high-performance products made from waste.
- Furniture: Brands are producing outdoor furniture made from recycled ocean plastics, combining aesthetic appeal with a commitment to sustainability.
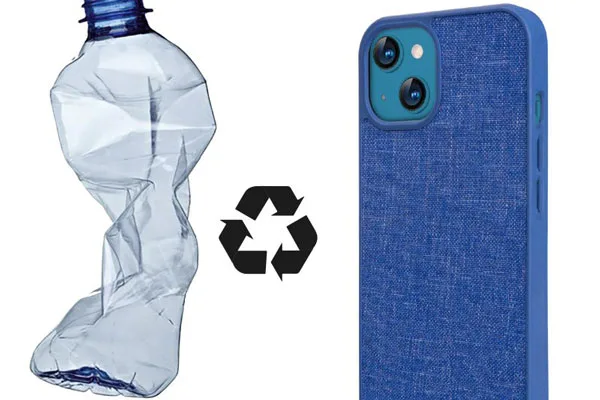
Recycled plastic iphone cases
Challenges in Using Recycled Ocean Plastics
While promising, integrating recycled ocean plastics into injection molding is not without its challenges:
- Material Quality: Most ocean plastics have to be reprocessed because of the long exposure to sunlight and saltwater that causes them to deteriorate.
- Cost: Collecting, cleaning, and preparing ocean plastics can be more costly than using virgin materials.
- Consumer Perception: Some consumers are still skeptical about the quality of products made from recycled materials.
However, advancements in material science and increased consumer awareness about sustainability are helping to overcome these hurdles.
The Future of Injection Molding with Recycled Ocean Plastics
The future is bright for the synergy between injection molding and recycled ocean plastics. Here’s what we can expect:
- Innovative Materials: New formulations of recycled plastics that enhance durability and performance.
- Regulatory Support: Governments worldwide are introducing incentives and regulations to promote the use of recycled materials.
- Increased Adoption: As technology and processes improve, more industries will adopt recycled plastics for their products.
By embracing recycled ocean plastics, injection molding addresses the pressing issue of plastic pollution and sets a benchmark for sustainable manufacturing practices.
Why Choose Nice Rapid for Sustainable Injection Molding?
Nice Rapid is dedicated to helping create state-of-the-art injection moldings aligned with sustainable development. Our experience with material choice and up-to-date production technology guarantees product quality for you while keeping our promise of respect for the environment.
Whether you’re integrating recycled plastics into your production line or developing new, eco-friendly products from scratch, Nice Rapid is the partner you can rely on. Together, we can end plastic waste and create a cleaner, greener future.
Conclusion
Innovative solutions are required to win the battle against ocean plastic pollution, and injection molding with recycled ocean plastics is a huge step in that direction. This technology, which converts waste into value, is environmentally friendly and further shows how sustainable manufacturing could be. With more industries and consumers embracing this approach, we inch closer to a world where plastic pollution becomes a thing of the past.
Are you ready to take the first step towards sustainable manufacturing using injection molding? Contact Nice Rapid today, and let’s work together toward a greener future.