When you think about everyday plastic products, it’s easy to overlook the technology behind their creation. But behind the scenes, blow molding is hard at work, shaping some of the most common, yet highly functional, items we use daily.
From plastic bottles to custom-shaped containers, blow molding is a manufacturing process that delivers versatility, cost-effectiveness, and high-quality results. Let’s delve into the intricacies of blow molding, exploring its transformative impact on custom plastic solutions and its role in helping industries achieve their design and efficiency objectives.
What is Blow Molding?
Blow molding is a manufacturing process that involves creating hollow plastic parts by inflating a heated plastic tube (called a parison) inside a mold. The parison is first extruded, and then air is blown into it, forcing the plastic to conform to the shape of the mold cavity. The result? A lightweight, hollow plastic product with seamless sides and smooth surfaces.
There are a few variations of blow molding, including extrusion blow molding, injection blow molding, and stretch blow molding, each suited for different types of products and production needs. Despite variations in technique, all blow molding methods adhere to the fundamental principle of employing air pressure to mold plastic into precise forms.
Why is Blow Molding So Effective?
Blow molding offers numerous advantages that make it a compelling choice for manufacturers across various industries. Let’s explore some of its key benefits:
Design Flexibility
One of the biggest advantages of blow molding is its remarkable ability to create custom plastic shapes. Whether it’s a standard bottle shape or a unique, custom-designed container, blow molding can handle it with remarkable flexibility. Manufacturers can produce everything from squeezable bottles to intricate designs tailored to specific industry needs. This design freedom makes blow molding a go-to process for industries ranging from packaging to automotive and medical devices.
Efficient Production at Scale
When it comes to mass production, blow molding truly shines. The process excels at producing large volumes of parts in a relatively short amount of time. Once the molds are created, producing thousands of plastic parts becomes a quick and cost-efficient endeavor. Plus, blow molding is highly automated, minimizing human error and ensuring consistent quality across every product. This efficiency explains why blow molding is such a popular choice for products like beverage bottles, personal care product containers, and even some automotive parts.
Low Waste, High Sustainability
Blow molding presents an excellent option for industries striving to minimize waste and reduce their environmental footprint. The process generates very little scrap material, as the plastic used to form the parts is recycled within the system. Additionally, the hollow nature of the parts often translates to less material usage compared to solid plastic alternatives, making them lighter and more cost-effective. This focus on reducing material waste positions blow molding as a more sustainable option for manufacturing.
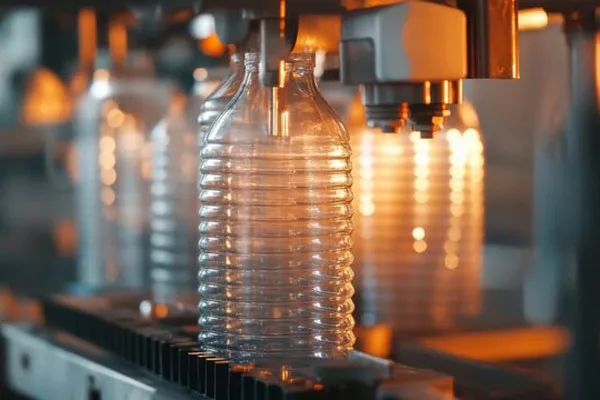
Blow molding bottles
Blow Molding in Action: Key Industries
Blow molding’s versatility and efficiency have led to its widespread adoption across numerous industries. Here are a few examples:
Packaging:
Perhaps the most well-known application of blow molding lies within the packaging industry. From plastic beverage bottles to personal care product containers, blow molding produces the lightweight, durable packaging that we encounter every day. The ability to create intricate shapes and sizes means that packaging can be precisely designed to suit the unique needs of each product while maintaining the strength and functionality required for transport and storage.
Automotive:
Blow molding isn’t just for small consumer goods—it also plays a key role in the automotive industry. Many car manufacturers utilize blow molding to produce parts like fuel tanks, air ducts, and other large, hollow components. The ability to create lightweight yet durable parts at scale makes blow molding an attractive option for the automotive sector, where performance and weight optimization are always top priorities.
Medical and Consumer Goods:
Medical device manufacturers are increasingly adopting blow molding for producing custom plastic containers, sterile packaging, and even medical components that require specific shapes or sizes. The flexibility of the process allows these manufacturers to meet strict regulatory requirements while still achieving the necessary functionality and precision.
Electronics:
In the electronics industry, blow molding is employed to make casings and housing for a variety of devices. The ability to create lightweight, durable and visually appealing products makes blow molding ideal for consumer electronics, including remote controls, phone cases and more.
Construction:
The construction industry uses blow molding to create a variety of components such as insulation materials, plumbing systems and weatherproofing products. These blow-molded parts help improve energy efficiency and reduce waste in construction projects.
Customization and Innovation: The Future of Blow Molding
As industries continue to demand more unique, customized plastic solutions, blow molding is poised for continuous evolution. Thanks to advancements in technology, the process is becoming even more precise, capable of producing increasingly intricate and specialized designs. Whether it’s integrating features like ergonomic grips or creating multi-layered plastic containers with advanced barrier properties, blow molding offers a level of innovation that keeps pace with the growing needs of modern manufacturing.
Moreover, with growing sustainability concerns, blow molding is well-positioned to meet the demand for more eco-friendly production methods. Manufacturers can now integrate recycled plastics into their blow molding processes, reducing their carbon footprint while still delivering high-quality products.
Conclusion
Blow molding stands out as one of the most flexible and efficient methods for creating custom plastic products. Its ability to produce high-quality, hollow plastic parts at scale makes it a valuable solution for a wide range of industries. From packaging and automotive to medical devices, blow molding empowers businesses to innovate and create products that meet both design and functionality requirements—all while minimizing waste. If you’re seeking a cost-effective, sustainable way to produce custom plastic solutions, blow molding is undoubtedly the way forward.