Here is a fan fact, most of the products that we use in our everyday lives are made from injection molding. Have you ever sat and wondered why is this so? Well, the answer is quite simple, injection molding is one of the most versatile techniques when it comes to the manufacture of parts and products.
Its one of the most widely used techniques as it comes with a wide variety of benefits, for this article we are going to look at some of the reasons why the use and application of injection molding have been on the rise.
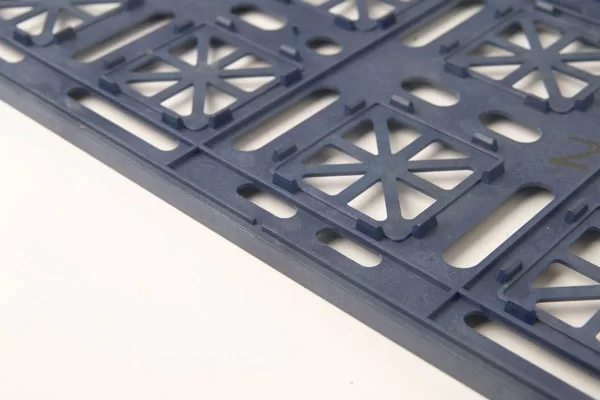
Plastic parts
What is plastic injection molding?
When it comes to the production of plastic parts in large quantities, plastic injection molding is one of the most commonly used techniques. Some of the most common accessories we use every day were made used injection molding techniques and procedures such as toys, disposable cutleries, chairs, consumer electronics casing, and many others.
Injection molding machines and equipment’s has primarily three parts: the plastic injection, clamp, and the injection unit. Within the machine, there is also a separate unit that primarily holds the material used to heat the plastic pellets.
After melting, the material is forced forward and injected into the mold cavity where it takes the desired shape or design. Once the material is cured it forms the plastic part. This part is then ejected out of the mold, and you’ll have the final product.
Reasons as to why injection molding is popular
In the 21st century, manufacturers are always looking for ways to lower the overall cost as well as enhance productivity. Well, injection molding is one of the key techniques that provide everything that you might need.
The entire molding process is fully automated, only one operator can monitor and control the whole machine. Automation significantly reduces the manufacturing as well as the overhead costs that are also reduced. If there is a reduction of the overhead cost, this means the cost-saving or lower manufacturing cost will be in turn passed onto the consumer. Furthermore, injection molding minimal wastage as well as being highly repeatable which further cuts down on production cost.
Another reason is the capability of the injection process to make products with complex features and geometries. Injection molds are usually subjected to intense pressure, the material is pressed harder against the mold, a fact which cannot be used in other manufacturing techniques. Because of this, it can accommodate huge design details. The high pressure applied in the molding process is part of the big reason why it’s simple to incorporate intricate and complex designs into its products.
The products made from the injection molding technique are robust and strong because it’s possible to use fillers in the injection molds. This hugely contributes to the reduction of density on the plastic while being molded. Plastic injection molding also can use a wide variety of materials giving producers a large pool of options to select from.