It’s possible to launch rapid prototyping of plastic-designed components using plastic injection molding. This six-step manufacturing process involves designing and manufacturing a mold, then clamping it, injecting a resin, dwelling the part while cooling, and finally ejecting it.
The plastic injection molding machine injector is a unique design feature of the device, manufactured from materials like aluminum or stainless steel. The injector is available in three design categories: single, multi, and family-cavity.
This post compares the types of injectors and focuses on how multi-cavity injection molding offers manufacturing processes effective results.
Multi-Cavity Injection Molds Explained
The multi-cavity injection mold utilizes several cavities within a singular design. This setup accommodates the production of several identical components with each production cycle. These molds can host anywhere from two to 164 mold cavities in increments of doubles, such as 2, 4, 8, 16, etc.
Multi-Cavity Vs. Family-Cavity Molds
The family mold is similar to the multi-cavity option in the sense it offers several cavities. However, the difference is that the family mold can shape different components in a single production run.
As a result, these molds are ideal for part and prototype manufacturing when it calls for different component designs in each production run.
Family molds offer variation in filling speed, presenting issues with defects during injection molding processes. Family molds are usually inexpensive to produce due to the potential for molding errors.
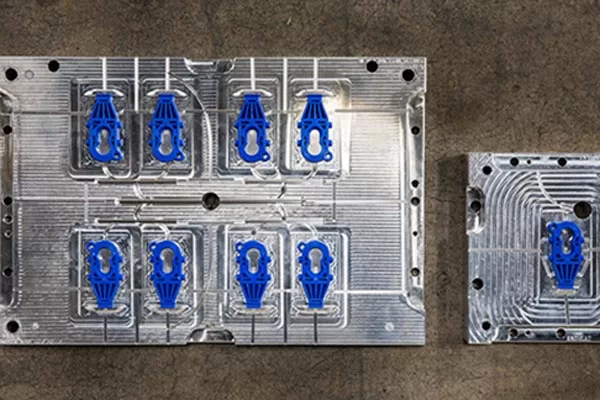
Multi-cavity injection molds
Multi-Cavity Vs. Single-Cavity Molds
The single-cavity mold differs from the multi-cavity design in that it only produces one item per production cycle. As a result, multi-cavity molds are the better choice for mass-production processes.
What are the Advantages of Using Multi-Cavity Molding?
Single, multi, and family molds offer unique features and applications for different production processes. Let’s unpack the benefits of using multi-cavity injection molding for customized production runs.
Reduction in Per-Unit Costs
Since multi-cavity molds allow for the production of multiple parts in a single manufacturing run, companies benefit from economies of scale and a reduction in production costs. Less operating time, labor, and overhead translates to lower production costs.
Increased Production Speeds and Efficiency
The increased cavities in multi-cavity molds offer a larger number of parts produced in each cycle. As a result, manufacturers get increased production speed and efficiency. Other design factors like filling speeds and venting also speed things up during manufacturing processes.
Enhanced Quality Control and Product Consistency
The multi-cavity injection mold offers manufacturers the optimal option for mass-product manufacturing, providing better levels of quality control and product consistency. Manufacturers benefit from fewer defects in production cycles and better consistency to design specifications.
Greater Flexibility with Designs
Multi-cavity injection molds offer manufacturers and designers better levels of flexibility with product and prototype design. In comparison, manufacturing using single-cavity injection molds only offers single and separate manufacturing, which isn’t ideal for large-scale production requirements.
With multi-cavity molds, manufacturers and designers can produce complex and intricate product designs easily and at scale. Multi-cavity molding offers manufacturers optimal flexibility in terms of component shapes and size.
For instance, components requiring several parts in varying sizes and shapes, multi-cavity molds can make parts of any given shape or size before moving on to other designs. This level of simultaneous part production saves manufacturers on production costs and time taken in production runs.
Minimize Production Space
Since the multi-cavity mold is capable of producing several components in a single production cycle, it reduces the need for workshop space for the machine. As a result, manufacturers can accommodate several machines and optimize the workshop floor space.
In contrast, single-cavity molds take up similar floor space on the production floor but don’t produce as many components per production cycle.