Liquid Silicone Rubber (LSR) stands as a remarkable material in the world of manufacturing and design, offering a versatile and high-performance solution across various industries. From mold-making and prototyping to medical devices and consumer products, LSR has gained widespread recognition for its exceptional properties and applications. In this article, we delve into the world of liquid silicone rubber, exploring its characteristics, benefits, and diverse uses that continue to shape innovation and advancement.
Characteristics of Liquid Silicone Rubber:
Liquid Silicone Rubber (LSR) is a two-part platinum-cured silicone elastomer that cures at room temperature to form a flexible, durable, and heat-resistant material. Key characteristics of LSR include:
Flexibility and Elasticity: LSR exhibits excellent flexibility and elasticity, allowing it to conform to intricate shapes and maintain its shape under stress or deformation.
Heat Resistance: LSR can withstand high temperatures without losing its mechanical properties, making it suitable for applications that require exposure to heat or thermal cycling.
Chemical Resistance: LSR is resistant to a wide range of chemicals, oils, and solvents, making it suitable for use in harsh or corrosive environments.
Biocompatibility: Medical-grade LSR formulations are biocompatible and non-toxic, making them ideal for use in medical devices, implants, and healthcare applications.
Transparency and Clarity: LSR can be formulated to achieve optical clarity and transparency, making it suitable for applications that require clear or translucent parts.
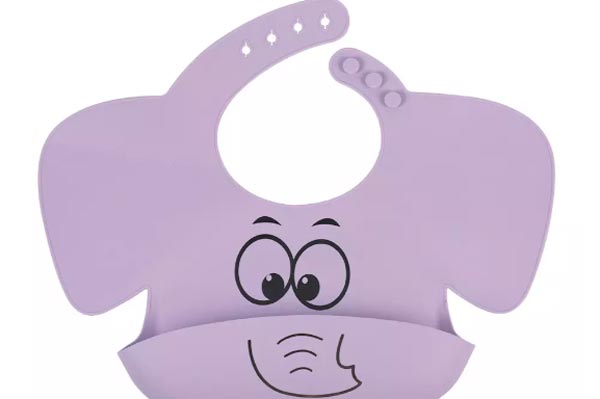
Silicone baby Bibs
Applications of Liquid Silicone Rubber:
Mold-Making and Prototyping: Liquid silicone rubber is widely used in mold-making and prototyping applications across various industries. Its flexibility, durability, and ability to reproduce intricate details make it ideal for creating molds for casting resins, plastics, and other materials.
Medical Devices and Healthcare: LSR is extensively used in the medical and healthcare industry for manufacturing a wide range of devices and components, including seals, gaskets, tubing, catheters, and implants. Its biocompatibility, sterilizability, and resistance to body fluids make it well-suited for medical applications.
Consumer Products: Liquid silicone rubber is used in the production of consumer products such as kitchenware, bakeware, baby products, and personal care items. Its food-grade properties, heat resistance, and durability make it a preferred choice for manufacturing silicone molds, spatulas, pacifiers, and other household items.
Automotive and Aerospace: LSR is utilized in the automotive and aerospace industries for manufacturing seals, gaskets, O-rings, and other components that require resistance to extreme temperatures, chemicals, and environmental conditions. Its ability to withstand thermal cycling and maintain sealing performance over a wide temperature range makes it well-suited for these applications.
Electronics and Electrical: Liquid silicone rubber is used in the electronics and electrical industry for manufacturing protective coatings, potting compounds, gaskets, and seals for electronic devices and components. Its excellent dielectric properties, thermal conductivity, and resistance to moisture and chemicals make it suitable for encapsulating and protecting sensitive electronic assemblies.
Liquid Silicone Rubber (LSR) stands as a testament to the ingenuity and innovation driving advancements in manufacturing and design. With its exceptional properties, versatility, and wide-ranging applications, LSR continues to push the boundaries of what’s possible, enabling industries to achieve new levels of performance, efficiency, and safety. As technology evolves and new formulations emerge, the potential for liquid silicone rubber to drive further innovation and transformation across industries is boundless, promising a future where the only limit is the imagination of those who harness its power.