Personalized medicine is revolutionizing the medical field in incredible ways. This approach clearly demonstrates that every patient is unique and, therefore, needs customized solutions for optimal outcomes. In this context, low-volume manufacturing plays an important role, allowing the fabrication of individualized medical devices, implants, and therapeutics for each patient.
The Power of Personalization in Medicine
Personalized medicine is revolutionizing healthcare by shifting away from a one-size-fits-all approach to treatments. Low-volume manufacturing empowers medical professionals to deliver:
- Custom Implants: Using patient scans and 3D modeling, manufacturers can create implants that perfectly match the patient’s anatomy, improving fit, function, and patient outcomes.
- Patient-Specific Surgical Guides: 3D-printed surgical guides enable surgeons to perform intricate operations with enhanced precision and accuracy, decreasing surgical time and increasing patient safety.
- Personalized Prosthetics: With sophisticated manufacturing techniques, we can design prostheses that fit comfortably and work properly for the end user.
- Individualized Drug Dosage Forms: Low-volume manufacturing enables the production of customized drug formulations and dosages, optimizing treatment efficacy and minimizing side effects.
Studies have shown that personalized medical solutions can significantly improve patient outcomes. According to research, patients who have individualized treatment get as much as 40 percent better than those who have traditional treatment.
Key Manufacturing Methods for Personalized Medicine
Several advanced manufacturing methods are driving the growth of personalized medical solutions:
- 3D Printing: With additive manufacturing (3D printing), doctors can create customized medical devices that have never been possible before. This enables the ability to produce patient-matched implants, surgical planning models, custom dental aligners, and prosthetic limbs very quickly and precisely. In Boston, one hospital even claimed to have slimmed down its surgery time by 25% with the help of custom-printed guides.
- CNC Machining: Computer numerical control (CNC) machining offers high precision and accuracy for creating complex medical devices, custom bone plates, small-batch medical instruments, and specialized surgical tools. This subtractive manufacturing scheme is perfect for the complex shapes and demanding tolerances found in mechanical engineering.
Success Story: Personalized Spine Solutions
One medical device company utilized low-volume manufacturing to develop spinal implants customized to the anatomy of individual patients. And the results were amazing:
- Patients experienced an 85% faster recovery time
- The patient satisfaction rate reached 90%
- The cost per procedure decreased by 30%
This is just one example of how individualized medicine could revolutionize the treatment of patients, resulting in better patient care, cheaper costs, and more satisfied patients.
Ensuring Quality in Small Batches
In the medical industry, low-volume production requires stringent quality controls to guarantee the safety and effectiveness of devices. Small-scale production allows for:
- 100% Part Inspection: We can individually inspect each component so we know that it fits the specifications of the quality.
- Complete Batch Tracking: It is possible to record every lot’s entire history, including the number of items used, the material, and the manufacturing conditions.
- Patient-Specific Documentation: Comprehensive documentation can be generated for each patient, outlining the design, manufacturing process, and quality control checks performed on their personalized medical solution.
- Strict Compliance Checks: Manufacturers must comply with stringent regulatory guidelines and quality management systems to guarantee that their products meet the highest standards of safety and performance.
Benefits for Medical Providers
Healthcare facilities and medical professionals are increasingly adopting personalized solutions, driven by the numerous benefits they offer:
- Reduced Complications: If custom-made medical devices and medicines provide 35% fewer post-surgery complications, would it not only benefit the patients but also save a lot of money on health care?
- Shorter Hospital Stays: With personalized solutions, hospital stays are 45% shorter. Improving the efficacy of treatments frees up fewer resources and increases patients’ satisfaction.
- Higher Patient Satisfaction: Patients receiving personalized care report 60% higher satisfaction scores, reflecting the positive impact of tailored solutions on their treatment experience.
- Lower Treatment Costs: Customized solutions involve higher initial costs, but by reducing complications in hospital stays and improving patient outcomes, personalized solutions can reduce total treatment costs by 25%.
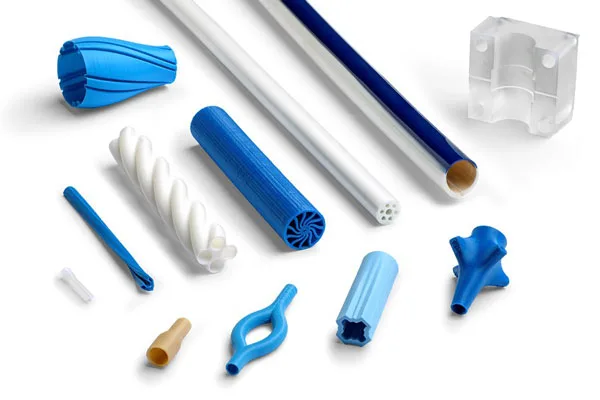
Medical 3d printing parts
Getting Started with Personalized Medical Manufacturing
Here are some steps to consider if you are thinking about entering the low-volume manufacturing personalized medical solution market:
- Process Selection: Consider the different manufacturing options (3D printing, CNC machined, etc.) and pick one that is right for the product and the amount to be produced.
- Quality Management: Implement strong quality control systems and procedures to guarantee that your products comply with the medical industry-related regulatory requirements and quality standards.
- Tracking and Traceability: Implement comprehensive tracking systems to maintain complete records of materials, manufacturing processes, and quality checks for each patient-specific solution.
- Collaboration with Healthcare Providers: Develop deep and meaningful relationships with healthcare providers, learn their needs, and work closely with them to design and develop customized solutions to individual patient needs.
Case Study: Revolutionizing Dental Aligners
A dental lab transitioned to low-volume manufacturing to produce custom dental aligners. The results were impressive:
- They were able to produce 50 unique aligner designs daily
- Production time decreased by 65%
- Material waste was reduced by 40%
- Patient comfort ratings significantly increased
This case study demonstrates the potential of low-volume manufacturing to transform personalized dental care, improving efficiency, reducing waste, and enhancing patient satisfaction.
Technology Enabling Personalized Medicine
Technology and improved technology move us closer to individualized medicine. Key enabling technologies.
- Medical Imaging Software: Advanced imaging software allows for precise 3D modeling of patient anatomy, enabling the design and production of custom implants and surgical guides.
- CAD/CAM Systems: Computer-aided design and manufacturing (CAD/CAM) systems facilitate the design and production of complex medical devices with high precision and accuracy.
- Quality Tracking Systems: Sophisticated tracking systems ensure complete traceability and documentation of materials, manufacturing processes, and quality checks for each personalized solution.
- Material Validation Processes: Strict material validation procedures guarantee that any material used for making custom medical devices is safe and biocompatible.
Questions to Consider for Your Medical Manufacturing Journey
In exploring the potential of low-volume manufacturing for custom medical solutions, ask yourselves the following questions:
- Can your current manufacturing process handle the unique requirements of personalized medical devices?
- What investments in technology, equipment, and training would be necessary to add personalized solutions to your product line?
- How can you ensure compliance with the stringent regulatory requirements and quality standards of the medical industry?
Cost-Effective Personalized Production
Personalized medicine solutions, although they may appear naturally more expensive, can smartly cut manufacturing decisions that make it far less expensive:
- Reduced Tooling Costs: Advanced manufacturing methods like 3D printing often require minimal tooling, which results in 50% lower tooling costs than traditional manufacturing.
- Minimized Material Waste: Low-volume manufacturing can reduce material waste by up to 70% by producing only what is needed for each patient.
- Faster Production Cycles: Agile manufacturing processes and streamlined workflows can shorten production cycles by 40%, enabling faster delivery of personalized solutions to patients.
- Lower Inventory Costs: Producing on demand eliminates the need for large inventories, reducing inventory costs by 30%.
Future Trends in Personalized Medical Manufacturing
The future of personalized medicine is bright, with ongoing advancements promising even greater precision, efficiency, and accessibility. Key trends to watch for include:
- AI-Guided Design Systems: Artificial intelligence will play a major role in designing and optimizing personalized medical solutions, such that it will be possible to find the perfect fit.
- Accelerated Production Methods: New and emerging manufacturing technologies will continue to accelerate production speeds, enabling rapid delivery of personalized solutions to patients in need.
- Innovative Biocompatible Materials: The research and invention of new biocompatible materials will expand the options for custom implants, prosthetics, and other medical devices.
- Smart Quality Control Systems: Intelligent quality control systems will leverage data analytics and machine learning to further enhance product quality and patient safety.
Ready to Embrace Personalized Medicine?
Ready to discover how low-volume manufacturing can revolutionize custom medical solutions? Contact Nice Rapid now! As the biotechnology field continues to expand, we can help you make sense of it all and develop a customized manufacturing solution that addresses your needs and helps improve patient quality of life.
Always remember that every patient needs individualized care. This dream comes to life through low-volume manufacturing. Making life better for some is the ultimate reason to have the ability, methods, tools, knowledge, and technology—everything to tailor perfectly a new medicament or test implant to save one’s life.