In the rapid prototyping and manufacturing industry, companies have options for low-volume and high-volume production. Low-volume manufacturing is suited to smaller projects. High-volume manufacturing services are the better choice for larger projects looking to benefit from savings brought on by economies of scale.
Companies must consider the right application for their project and debate the benefits of low and high-volume production for their needs. Whether they’re releasing new products to the market or scaling manufacturing for existing projects, manufacturers must balance low costs and high quality for success.
Increasing manufacturing volume results in lower unit costs when working with contract manufacturing partners. The type of manufacturing method and manufacturing location also contribute to project costs.
There are several considerations when choosing between low and high-volume manufacturing processes. Additive manufacturing is one of the most popular processes for all volume requirements in rapid prototyping and mass production projects. This gives project managers and manufacturers a viable production process for any volume required, reducing risk while improving the agility of the business.
Here is how additive manufacturing (3D printing) reduces the gap between low and high-volume manufacturing.
Overview of Low-Volume Production
- Suitable for 1-10,000 components per year.
- Reduced lead times and lower setup expenses.
Overview of High-Volume Production
- Suitable for projects producing more than 50,000 parts annually.
- Moderate setup expenses and lead times.
What is the Difference Between Mass Production & Low-Volume Production?
When considering your options for low or high-volume manufacturing, it’s important to consider several factors relating to cost-effective production. The elements driving costs in rapid prototyping or mass manufacturing are the following.
- Set up times.
- Flexibility for changes in design.
- Accuracy and precision for component manufacturing.
Let’s take a closer look at the differences between low and high-volume manufacturing.
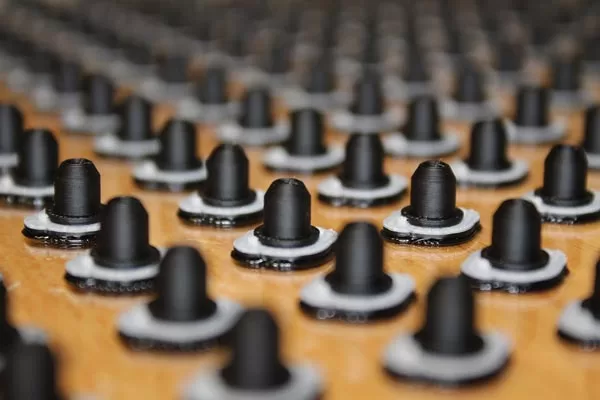
Low volume production parts
What are the Pros & Cons of High-Volume Production?
High-volume production is the best option for high-demand products. Companies looking to create and mass-produce prototypes to satisfy demand will get the best value and cost savings from high-volume production practices.
Mass production significantly drops unit costs per component compared to low-volume production processes. For instance, you might pay $500 for a one-off but $.050 for the same item when produced in the hundreds of thousands of units.
High-Volume Production Pros
- Faster turnaround times.
- Ideal for fulfilling large orders.
- Manufacturers can meet huge market demand.
- Greater project ROI from production cost savings.
High-Volume Production Cons
- Less flexibility with design changes.
- Limited capacity in production.
- It is not the best choice for small projects or rapid prototyping tasks.
- Requires significant resources with conventional manufacturing methods.
What are the Pros & Cons of Low-Volume Production?
A low-volume production strategy is ideal for rapid prototyping projects where a company wants to introduce low-demand products. Low production volumes are generally suited to rapid prototyping projects and limited-edition or customized products.
Low-Volume Production Pros
- Ideal for lower order quantities.
- Reduces overhead costs.
- Fewer materials are wasted in production.
- Enhanced agility for design changes.
- Great for fast prototyping lead times.
Low-Volume Production Cons
- Increases unit costs.
- Extended lead times.
- Limits on capacity.
- Not suitable for high-demand products.
Mass Production for High Volume and Less Variety
High-volume mass production is preferred over low-volume for improved cost efficiency while ensuring high quality. This production strategy is less labor-intensive and more efficient, resulting in huge project and manufacturing cost savings.
However, companies looking to produce products in lower quantities may see more benefit from low-volume production. This strategy has a higher degree of flexibility, accommodating a broader range of product designs and projects.
Why Use 3D Printing for High and Low Volume Manufacturing?
Additive printing, known by its more common moniker, “3D printing,” is highly adaptable and suitable for low- and high-volume manufacturing projects. 3D printing reduces CAPEX investment requirements for traditional process scaling.
Companies can implement low-volume, high-mix production strategies to improve and increase throughput. 3D printing allows manufacturers to change their business model with the following strategies.
Design Changes & Agility
Eliminate the requirement for custom tooling to accelerate manufacturing of revised and new designs. Design engineers can change the original design and experience immediate production of the new product with the desired changes.
On-Demand Ordering, Manufacturing, & Shipping
3D printers print directly from digital model designs, allowing the immediate production of parts and products on demand. Thus, companies benefit from cost savings since they need to keep less inventory on-site to satisfy market demand.
Consolidation of Manufactured Parts
3D printers can manufacture complex components, consolidating sub-parts to eliminate unnecessary assembly typically required in processes like injection molding. Streamlining manufacturing processes and steps makes 3D printing cost-competitive compared with injection molding.
No Custom Tooling Required
Increasing volume leads to improvements in manufacturing efficiency. 3D printing doesn’t require custom tooling for each component, giving the manufacturer a wide range of products using the same manufacturing equipment. Its high degree of flexibility supports a combination of multiple “SKUs” or products, thereby increasing manufacturing volume.
Improve Lead Times & Logistics Costs
With improved automation in manufacturing processes, companies receive better agility and flexibility in locating their operations. The manufacturer can set up their operation closer to the customer, resulting in lower logistics costs and faster customer fulfillment.