In the realm of manufacturing, precision is paramount. Silicone, with its versatile properties, stands as a cornerstone material. This guide is your beacon to navigating the sea of options, ensuring your molding project’s triumph.
Silicone is a versatile material that can be used for a variety of molding applications. It is available in a wide range of durometers, making it suitable for a variety of applications. Silicone is also resistant to heat and chemicals, making it a good choice for molding applications that require durability.
When choosing a silicone for your molding project, it is important to consider the following factors:
- The durometer of the silicone. The durometer is a measure of the hardness of the silicone. The higher the durometer, the harder the silicone.
- The temperature resistance of the silicone. The temperature resistance of the silicone is important to consider if your molding project will be exposed to high temperatures.
- The chemical resistance of the silicone. The chemical resistance of the silicone is important to consider if your molding project will be exposed to chemicals.
Once you have considered these factors, you can begin to narrow down your choices of silicone for your molding project. There are a variety of silicone molding compounds available on the market, so you should be able to find a silicone that is suitable for your needs.
Understanding Silicone Varieties
Silicone is a versatile material with a wide range of applications. However, it is not a one-size-fits-all solution. The hardness, elasticity, and chemical resistance of silicone can vary significantly, depending on the specific formulation.
For intricate parts, a softer silicone is often preferred. This is because softer silicones are more forgiving and can be molded into more complex shapes. Conversely, tougher applications often require firmer silicone. This is because firmer silicones are more durable and can withstand more wear and tear.
In addition to hardness and elasticity, silicone can also vary in its chemical resistance. Some silicones are more resistant to chemicals than others. This is important to consider when choosing silicone for a particular application. For example, if a silicone is exposed to harsh chemicals, it is important to choose a silicone that is resistant to those chemicals.
By understanding the different varieties of silicone, you can choose the right silicone for your specific application. This will ensure that your silicone parts perform as expected and last for many years to come.
Decoding the Durability Debate
Durability is a complex topic, and there is no one-size-fits-all answer. However, there are a few key factors that can help you determine the durability of a silicone product.
- Hardness: Silicones are available in a wide range of hardness levels, from soft and flexible to hard and rigid. The hardness of silicone will affect its durability, with harder silicones being more resistant to wear and tear.
- Resistance to chemicals: Silicones are resistant to a wide range of chemicals, but some chemicals can be more damaging than others. If your project will be exposed to harsh chemicals, be sure to select a silicone that is resistant to those chemicals.
- Resistance to temperature: Silicones can withstand a wide range of temperatures, but some silicones are more resistant to heat or cold than others. If your project will be exposed to extreme temperatures, be sure to select a silicone that is resistant to those temperatures.
By considering these factors, you can select a silicone that is durable enough for your project.
Here are some additional tips for selecting a durable silicone:
- Test the silicone: If you are unsure about the durability of silicone, test it by subjecting it to the conditions it will be exposed to. This will help you determine if the silicone is durable enough for your project.
- Consult with a silicone expert: If you are still unsure about the durability of silicone, consult with a silicone expert. They can help you select a silicone that has the right hardness, chemical resistance, and temperature resistance for your project.
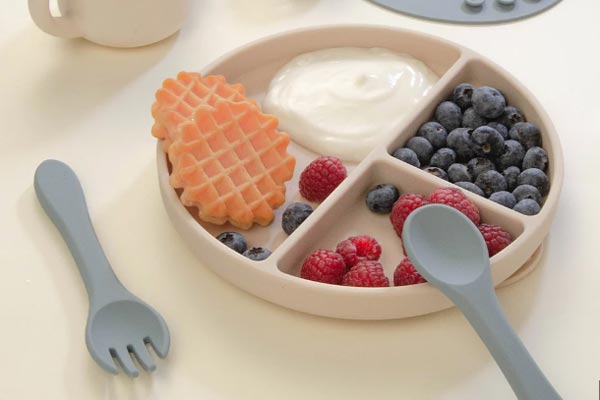
Silicone baby dinnerware
Navigating the Compliance Complex
In industries like food and healthcare, compliance isn’t an option; it’s a mandate. Regulatory bodies around the world have strict standards for silicone products, and your silicone choice must meet these standards.
Here are a few things to keep in mind when navigating the compliance complex:
- Identify the relevant regulations. The first step is to identify the regulations that apply to your silicone product. These regulations will vary depending on the industry you’re in, the intended use of your product, and the country where you’re selling it.
- Understand the requirements of the regulations. Once you’ve identified the relevant regulations, you need to understand the requirements of those regulations. This includes understanding the specific testing methods that are required, the acceptable levels of impurities, and the labeling requirements.
- Select a silicone that meets the requirements. Once you understand the requirements of the regulations, you can select a silicone that meets those requirements. It’s important to work with a supplier who can help you verify that your silicone meets the necessary standards.
- Document your compliance. It’s important to document your compliance with the regulations. This documentation can be used to demonstrate your compliance with regulatory authorities and to protect yourself from liability.
Navigating the compliance complex can be a daunting task, but it’s essential to ensure that your silicone products meet the necessary standards. By following these tips, you can make sure that your products are compliant and that you’re protected from liability.
Efficiency and Economy: Striking the Balance
When it comes to choosing materials for a project, efficiency, and economy are often competing priorities. It can be tempting to go for the cheapest option, but this is not always the best choice in the long run. A more efficient material may cost more upfront, but it can save you money in the long run by reducing energy consumption or maintenance costs.
For example, a solar panel may cost more than a traditional light bulb, but it will save you money on your electricity bill over time. Similarly, a high-efficiency air conditioner may cost more than a standard model, but it will use less energy and save you money on your utility bills.
When choosing materials, it is important to consider the entire lifecycle cost of the product, not just the initial purchase price. The most efficient material may not always be the most economical, but it is often the best choice in the long run.
Here are a few tips for striking the right balance between efficiency and economy:
- Consider the lifespan of the material. A more efficient material may cost more upfront, but it will last longer and save you money in the long run.
- Consider the performance of the material in your application. An initially cheaper option might cost more in the long run due to replacements and maintenance.
- Do your research. Compare different materials and their costs to find the best option for your project.
By considering the entire lifecycle cost of a material, you can make the most economical choice for your project.
Seeking Specialist Support
When it comes to silicone, there are a lot of factors to consider. The type of silicone you need, the application you’re using it for, and the desired properties all play a role in the decision-making process. That’s why it’s so important to work with a silicone expert who can help you navigate the complex world of silicone and find the perfect solution for your needs.
A silicone expert can help you with everything from choosing the right type of silicone to formulating a custom solution that meets your specific requirements. They can also provide valuable insights into the application process and help you avoid costly mistakes.
In addition to saving you time and money, working with a silicone expert can also help you ensure that your project is completed successfully. With their expertise and guidance, you can be confident that you’re using the right silicone for the job and that your project will be completed on time and within budget.
So, if you’re considering using silicone for your next project, don’t hesitate to reach out to a silicone expert for help. They can make the process easier, more efficient, and more successful.
In conclusion, the right silicone selection is less about guesswork and more about informed decisions. Understand your needs, consider the environment, and seek expert guidance. With this approach, your molding project is set not just for completion but for excellence.
Ready to Elevate Your Project with Precision Silicone Molding? Connect with Nice Rapid Today! Our expert team is standing by to bring your vision to life with top-tier manufacturing solutions. Don’t wait to transform your ideas into reality. Click here to get started with Nice Rapid – where innovation meets excellence!