In an ideal manufacturing realm, having a modern technological application and skills of the operator will yield a perfect product all the time. Of course, not everything is ideal. And mistakes can happen. Like in sheet metal fabrication, distortion is one of the mistakes that can bever be avoided.
Several techniques can be applied to correct this error with minimum effect to the part. In this article, we compile four of the most common issues with sheet metal fabrication and go through the best practices that manufacturers are using to correct them.
Minor or Severe Wrinkles
One of the most common errors in sheet metal manufacturing is minor or severe wrinkles. These are caused by the compressive strains in the sheet metal stamping process that pushes the metal. Wrinkles can result in a wrong manufacturing process or invalid parameters.
The good news is, wrinkles on the sheet metal can be easily corrected by stretching or drawing the material back out using binders and pads. For more complex shapes, manufacturers can use draw beads. The only issue with wrinkles is the waste produced from clamping and stretching the wrinkles out.
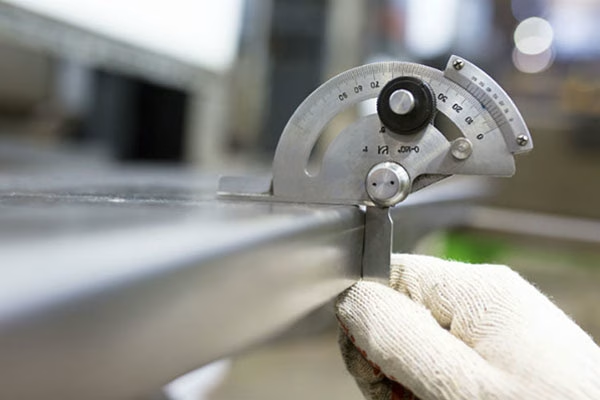
Sheet metal measurements
Splits
Formation of splits during sheet metal fabrication is inevitable because the material is often extended to the point that they are far more than their allowed tensile strength.
Splits can be avoided using software that simulates stamping. This software will consider several variables like the material type and thickness, the number forming stages, form depth and radius, and the blank size and shape.
Springback
This sheet metal fabrication error is usually caused by the elastic characteristics of the material. Springback occurs when the sheet metal is strained during the process and then relaxes back after. It is a problem that is common in metals with high tensile strength because there is a small difference between their yield and tensile strength.
The solution to this error is by compensating or overbending the material to accommodate the elasticity of the metal. Though this method is commonly used, it is not necessarily effective. Experts recommend using positive stretching to manage springback. It is made possible by increasing the part strength to make the metal stronger and stiffer, resulting in a reduced springback.
Distortion
When the sheet metal can no longer handle the stretching and compressing during the fabrication process, deformation ensues. It will result in bending across the grain, variations in thickness and hardness, or reducing the hardening process. In some cases, the position of the holes or the size of the sheet metal is also affected.
There are plenty of solutions to correct distortion, depending on the type of distortion. Here are some of them:
- Mechanical Strengthening: It can be corrected by pressing or hammering. However, between the two, hammering can cause surface damage and work hardening. Pressing is more favored because it can correct bowing or angular distortion.
- Thermal Correction: It can be achieved by applying heat to the local area to the point that it pulls the distortion back into place upon cooling. There are three corrective techniques to choose from: spot heating, line heating, and wedge-shaped heating.
Conclusion
Errors cannot be avoided during sheet metal fabrication. However, there are solutions available to manage these issues. All you need to do is find the best company that offers these services within your budget and project timeline.