In today’s fiercely competitive marketplace, manufacturers are engaged in a constant race against time, striving to produce large quantities of products with lightning speed, unwavering quality, and cost-efficiency that would make even the most frugal accountant smile.
High-volume manufacturing is the key to conquering these challenges, empowering businesses to scale production to dizzying heights, reduce unit costs to a whisper, and maintain product quality that would make even the most discerning critic nod in approval. But to truly unlock the full potential of high-volume manufacturing, optimizing the very processes that drive it is essential. It’s like fine-tuning a high-performance engine, ensuring every gear turns with seamless precision.
By streamlining operations, boosting output, and slashing time-to-market, manufacturers can not only stay ahead of the competition but also dance gracefully with the ever-growing demands of consumers. Let’s embark on a journey to explore how optimizing high-volume manufacturing can revolutionize your business operations and pave the path to enduring success.
What is High-Volume Manufacturing?
Imagine a production line humming with activity, churning out a steady stream of identical products with the precision of a Swiss watch. That’s high-volume manufacturing in action. It’s a process typically employed for items that are in high demand, think consumer electronics flying off the shelves, automotive parts keeping the world on wheels, life-saving medical devices, and the packaging that protects everything we consume.
High-volume manufacturing is a symphony of repeatability, consistency, and efficiency. The goal is to maximize production output while keeping costs as low as possible per unit, all without compromising on the quality that customers crave.
This type of manufacturing often requires advanced machinery, automated systems, and streamlined workflows to handle the sheer scale of production. It’s like conducting an orchestra, ensuring every instrument plays its part in perfect harmony. The result is a steady output of products that can be delivered to market with the speed of a cheetah, satisfying the insatiable hunger of consumer demand.
Why is Optimizing High-Volume Manufacturing Crucial?
Optimizing high-volume manufacturing is like fine-tuning a race car, ensuring it performs at its peak potential. Here’s why it’s crucial:
Maximizing Production Efficiency
In the high-stakes world of high-volume manufacturing, efficiency reigns supreme. The more efficiently production processes run, the higher the output and the lower the cost per unit. It’s a win-win situation that would make any business leader rejoice.
By optimizing workflows, manufacturers can reduce downtime, eliminate bottlenecks, and ensure that each step of the production process is as smooth and fast as a Formula 1 race car. This often involves upgrading equipment, automating processes, and continuously refining production schedules.
High-efficiency processes not only save precious time but also reduce labor costs and minimize errors, leading to increased profitability that would make even the most Scrooge-like accountant crack a smile.
Reducing Unit Costs
One of the primary goals of high-volume manufacturing is to minimize unit costs. The more units produced, the lower the cost per unit, thanks to the magic of economies of scale. To truly optimize this aspect, manufacturers need to focus on streamlining their material handling, inventory management, and workforce processes. It’s like a chef perfecting a recipe, ensuring every ingredient is used with maximum efficiency.
By minimizing waste, ensuring the right materials are always on hand, and improving workforce training, businesses can significantly reduce their overall production costs. This enables them to offer competitive prices that would make customers’ wallets sing without sacrificing the product quality they demand.
Maintaining High-Quality Standards
It’s crucial that high-volume manufacturing doesn’t come at the expense of quality. In fact, maintaining product quality while ramping up production is one of the biggest challenges in this high-stakes game. It’s like walking a tightrope, balancing speed and precision.
By implementing lean manufacturing principles, manufacturers can ensure consistent quality control throughout the production process. Automation and smart systems can also help monitor quality in real-time, quickly identifying defects or issues that could affect the final product.
Advanced technologies such as artificial intelligence and machine learning can be leveraged to predict and prevent potential failures, ensuring that high-quality standards are upheld without slowing down production.
Reducing Time-to-Market
In industries where time is of the essence, reducing time-to-market is a matter of survival. The faster a product is manufactured and delivered to customers, the better the company can respond to demand fluctuations and stay ahead of competitors. It’s like a game of chess, anticipating the next move and acting with decisive speed.
By optimizing high-volume manufacturing processes, businesses can speed up production timelines and deliver products faster. Efficient workflows, automation, and better coordination between supply chains can cut down on delays and lead to faster product release cycles, which is crucial in fast-paced industries like consumer electronics and automotive manufacturing.
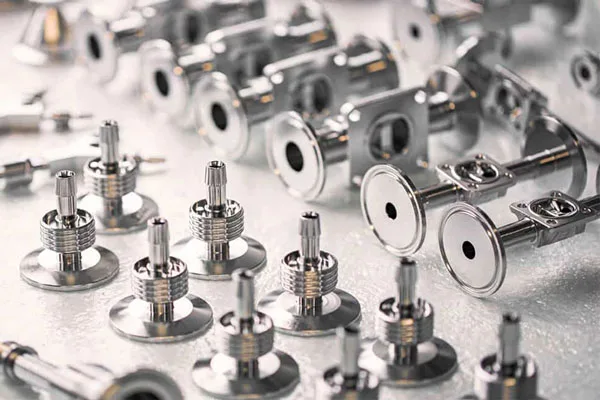
Stainless steel cnc parts
Key Strategies for Optimizing High-Volume Manufacturing
Optimizing high-volume manufacturing requires a strategic approach, like a master strategist planning a winning campaign. Here are some key strategies:
Embrace Automation and Robotics
Automation is one of the most powerful weapons in the arsenal of efficiency improvement for high-volume manufacturing. By integrating robotics and automated systems into production lines, manufacturers can speed up operations, reduce human error, and maintain consistent quality. It’s like having an army of tireless workers performing tasks with unwavering precision.
Automation can be applied to everything from assembly lines to packaging, reducing manual labor and freeing up workers to focus on more complex tasks that require human ingenuity. With the ability to operate 24/7, automated systems can significantly increase output and reduce the time spent on each unit.
Implement Lean Manufacturing Practices
Lean manufacturing is like a sculptor chiseling away at waste, eliminating anything that doesn’t add value to the final product. By adopting lean principles, manufacturers can optimize their production processes and reduce inefficiencies.
This includes optimizing workflows, improving inventory management, and focusing on continuous improvement. Regularly reviewing and adjusting processes helps to eliminate bottlenecks and streamline operations, ensuring that production moves quickly and without interruption.
Invest in Advanced Technologies
The integration of advanced technologies such as the Internet of Things (IoT), artificial intelligence (AI), and machine learning (ML) can significantly enhance the optimization of high-volume manufacturing. These technologies enable real-time monitoring of equipment performance, predictive maintenance, and quality control. It’s like having a crystal ball, predicting potential problems before they arise.
AI and ML algorithms can identify patterns and anomalies in production, allowing manufacturers to make proactive adjustments before issues disrupt the flow. IoT sensors can track the flow of materials, helping to improve supply chain management and reduce delays. These technologies can also assist with process optimization, leading to faster production cycles and lower operational costs.
Focus on Supply Chain Optimization
A seamless and efficient supply chain is the lifeblood of high-volume manufacturing. Delays in material deliveries or poor coordination between suppliers and manufacturers can cause costly downtime and production delays. It’s like a well-choreographed dance, ensuring every step is in sync.
By optimizing the supply chain, businesses can ensure that materials are available when needed and that production schedules are met without interruption. This includes implementing just-in-time (JIT) inventory management systems, improving communication with suppliers, and using data analytics to forecast demand and manage inventory levels more accurately.
Ensure Employee Training and Engagement
Although automation plays a significant role in high-volume manufacturing, human expertise remains an invaluable asset. To optimize high-volume production, manufacturers should invest in employee training programs to ensure that workers are well-equipped to handle automated systems, troubleshoot issues, and maintain high standards of quality control.
Engaged employees who understand the overall production goals are more likely to work efficiently, identify areas for improvement, and contribute to the optimization process. It’s like a well-trained team working together towards a common goal.
The Future of High-Volume Manufacturing
As the demand for faster production cycles and more complex products continues to soar, the future of high-volume manufacturing will be driven by the twin engines of innovation and technology.
The integration of smart factories, automation, and real-time data analytics will shape the next wave of optimization, making manufacturing processes even more efficient, flexible, and adaptable. It’s like a living organism constantly evolving and adapting to its environment.
Additionally, as sustainability becomes an even greater focus, high-volume manufacturers will need to find innovative ways to reduce waste, improve energy efficiency, and implement sustainable practices. The use of recyclable materials, energy-efficient machinery, and reducing carbon footprints will be essential to meet both regulatory requirements and consumer expectations for eco-friendly manufacturing.
Conclusion
Optimizing high-volume manufacturing is not just a desirable goal; it’s imperative for businesses looking to scale production, improve efficiency, and remain competitive in today’s dynamic market.
By embracing automation, lean practices, advanced technologies, and a relentless focus on quality control, manufacturers can streamline operations, reduce costs, and accelerate time-to-market.
As industries continue to evolve at a breakneck pace, the ability to optimize high-volume manufacturing processes will become a key differentiator for companies aiming to meet the growing demand for products while maintaining excellence in performance and delivery. It’s a journey of continuous improvement, a quest to achieve manufacturing excellence.