The injection molding process is one of the most versatile and highly functional manufacturing techniques that is used to make a wide variety of parts and products used in different applications. Some of the most commonly used applications of injection molding are combs, automotive dashboards, wire spools, bottle caps, packaging, and numerous plastic product that we use daily.
It’s no surprise at all that plastic injection molding is one of the most widely used manufacturing techniques in the production world. The process is mainly suitable for high-volume production and comes with a lot of benefits compared to other production processes. This includes:
- It comes with higher production rates
- It’s compatible with a wide variety of raw-materials
- Has low labor cost
- Requires no or minimal finishing services
- Injection molding has low scrap rates
The only disadvantage that we found with plastic injection molding is the fact it requires huge investment, additionally, it also comes with huge running costs. The technique requires both engineers and designers to design parts and components specifically designed for molding.
Commonly used materials for injection molding
The good thing about plastic injection molding it uses a wide range of raw materials to make different parts and products. The materials used range from thermosets, elastomers, as well as all kinds of thermoplastics.
During the ’90s there were approximately 18,000 materials that were used in plastic injection molding at the time. Since then, the number has been increasing close to 750 every year. Most of the materials used are either alloys or blends of materials that have been previously developed which further widens the selection pool of materials to be used.
The materials used in these techniques are usually selected based on their strength as well as how the parts function on the end-product. Other vital and important aspects also influence the type of material to be used.
Products and appliances made from plastic injection molding
A lot of things can be created from plastic injection molding, here are some of the most commonly used products that we use in our daily lives.
Medical devices
Plastics are replaceable, sanitary, flexible, and lightweight. The medical industry is amongst the biggest beneficiaries of these qualities. It’s for this reason that there is a huge demand for medical equipment’s made using this technique.
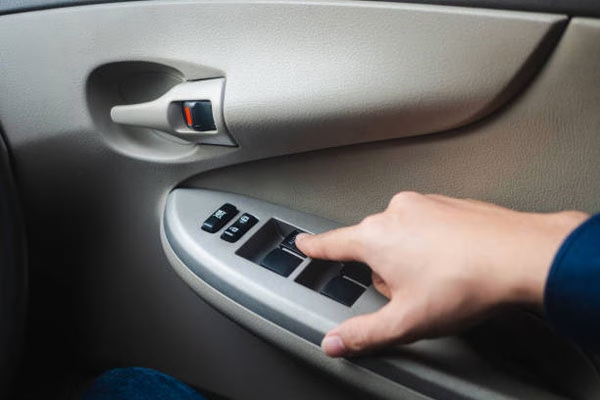
Plastic window buttons
Automotive and machinery parts
Motor vehicle has many plastic parts which have been fabricated through injection molding techniques. Some common parts include cup holders, window buttons, radio controls just to mention a few
Household items
Most of the normal items found in most households are made using injection molding techniques. Some of the commonly used household items include molded closures, drinkware and containers, and so on.
Agricultural materials
Most agricultural equipment is shifting from metal to plastics because they are a cheaper alternative, have high resistance to humidity as well as impact. Plastic is also highly resistant to high temperatures as most of the agricultural products are added with UV protection shielding them from corrosion.
Plastic injection molding is a common manufacturing technique, they are now used in virtually almost every sector, its opportunities are limitless.