In advanced manufacturing, where precision and performance are paramount, Liquid Silicone Rubber (LSR) molding has emerged as a game-changer. This innovative process empowers manufacturers to produce parts with exceptional accuracy, flexibility, and chemical resistance, making it ideal for demanding applications across various industries.
From intricate medical devices to robust seals and resilient electrical components, LSR molding delivers consistent, high-quality results for high-performance products that must withstand extreme conditions. Let’s explore the intricacies of this remarkable process and discover how it unlocks new possibilities in precision manufacturing.
What is Liquid Silicone Rubber Molding?
Imagine a process where a liquid material, with the consistency of honey, is transformed into intricate, high-performance components. This is the essence of LSR molding. Liquid Silicone Rubber, a two-component material consisting of a base and a catalyst, is meticulously injected into a closed mold cavity. Within this precisely engineered space, the liquid silicone undergoes a remarkable transformation, curing and solidifying into a durable elastomer with exceptional properties.
LSR molding distinguishes itself from traditional silicone molding through its use of liquid silicone, which offers unparalleled precision and design flexibility. This advanced process allows for the creation of parts with intricate geometries, tight tolerances, and complex features that would be challenging to achieve with other molding techniques.
Advantages of Liquid Silicone Rubber Molding
LSR molding offers a compelling array of advantages that make it a preferred choice for demanding applications:
- Exceptional Precision and Accuracy: LSR molding excels at producing parts with intricate details and tight tolerances. The low viscosity of the liquid silicone ensures that it flows effortlessly into even the most complex mold cavities, capturing fine features with remarkable accuracy. This precision is critical for applications where dimensional accuracy is paramount, such as medical devices, seals, and microfluidic components.
- Unwavering Flexibility: Parts produced through LSR molding possess exceptional flexibility and elasticity, allowing them to withstand repeated bending, stretching, and compression without losing their shape or integrity. This flexibility makes LSR ideal for applications requiring dynamic movement or resistance to vibration, such as seals, gaskets, and wearable devices.
- Robust Chemical Resistance: LSR exhibits outstanding resistance to a wide range of chemicals, solvents, and oils, making it suitable for applications in harsh environments. This chemical resistance ensures that LSR parts maintain their performance and integrity even when exposed to challenging substances, making them ideal for automotive, aerospace, and industrial applications.
- High-Temperature Stability: LSR can withstand a broad range of temperatures, from extreme cold to high heat, without compromising its properties. This thermal stability makes it suitable for applications requiring resistance to extreme temperatures, such as seals in engine compartments, electrical insulation, and medical devices that undergo sterilization processes.
- Biocompatibility and Safety: LSR is biocompatible, hypoallergenic, and does not leach harmful substances, making it an excellent choice for medical devices, food contact applications, and products that come into contact with the human body. Its safety profile makes it suitable for sensitive applications where material purity and biocompatibility are critical.
The LSR Molding Process
1. Design and Prototyping: Before production, CAD designs are created and prototypes may be developed using 3D printing or other rapid prototyping techniques to validate the design.
2. Mold Fabrication: High-quality molds are typically produced from steel or aluminum, engineered to accommodate specific design features and tolerances.
3. Injection Molding: The LSR components are mixed and injected into the mold cavity at high pressure. The liquid silicone fills the mold and conforms to its shape.
4. Curing: Silicone undergoes a curing process, often facilitated by heat, that transforms it into a solid elastomer.
5. Demolding: After curing, the finished parts are removed from the mold. A well-designed mold allows for easy demolding without damaging the part.
6. Finishing and Quality Control: Post-processing such as trimming, inspection, and testing ensure that parts meet quality standards.
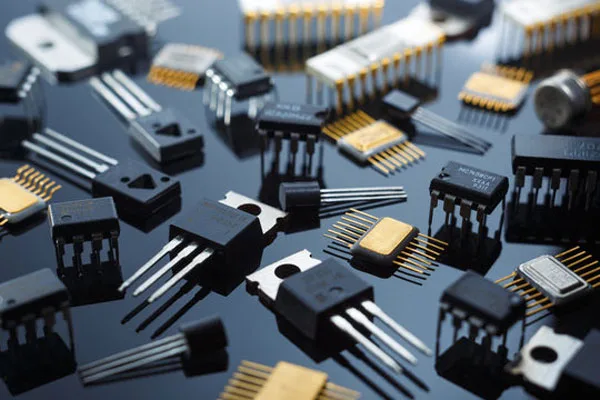
Electronic components
Applications of Liquid Silicone Rubber Molding
LSR molding’s versatility and performance benefits have led to its adoption across a wide range of industries:
- Medical Devices: LSR molding is extensively used in the medical industry to produce a variety of components, including implants, catheters, seals, and drug delivery systems. Its biocompatibility, sterilizability, and ability to create intricate geometries make it ideal for demanding medical applications.
- Automotive: The automotive industry relies on LSR molding for the production of seals, gaskets, O-rings, and other components that must withstand high temperatures, exposure to chemicals, and demanding operating conditions. LSR’s durability and resistance to oils and solvents make it a reliable choice for automotive applications.
- Electronics: LSR molding is employed in the electronics industry to create insulators, connectors, seals, and protective covers for sensitive electronic components. Its electrical insulation properties, flexibility, and resistance to moisture and dust make it well-suited for electronic applications.
- Consumer Products: LSR molding finds applications in a variety of consumer products, including kitchenware, baby products, sporting goods, and wearable devices. Its flexibility, durability, and non-toxic nature make it a safe and reliable choice for consumer applications.
Considerations
When considering LSR molding for precision manufacturing, it is essential to factor in:
- Material Selection: Different formulations exist for various applications and performance requirements.
- Mold Design: A well-engineered mold is crucial for achieving precise and consistent results.
- Equipment: Specialized LSR molding machines are required to handle the specifics of the material.
- Regulatory Compliance: For medical or food-related applications, adherence to relevant standards (like FDA regulations) is essential.
The Future of Liquid Silicone Rubber Molding
As industries continue to push the boundaries of innovation and demand increasingly sophisticated materials and manufacturing processes, LSR molding is poised for continued growth and advancement. Advancements in automation, mold design, and material technology are driving the development of even more precise, efficient, and sustainable LSR molding solutions.
With its ability to produce high-performance parts with exceptional precision, flexibility, and chemical resistance, LSR molding is transforming the manufacturing landscape. As industries seek to create increasingly complex and demanding products, LSR molding stands ready to deliver the precision and performance required to meet the challenges of the future.