Sustainability is no longer a fad; it’s a need. As the world steers towards a lower-waste, resource-conserving future, production companies are looking for methods to adapt their manufacturing to the circular economy. One such process is pressure die-casting, which, in addition to being versatile and productive, is an important option to ensure high-quality production. In addition, it contributes to sustainable design in that it has the potential to be recycled or disassembled easily.
This blog explores how pressure die-casting contributes to the circular economy and highlights sustainable practices that position this manufacturing process as a leader in promoting a greener future.
What Is the Circular Economy, and Why Does It Matter?
The circular economy is an economic system aimed at minimizing waste and maximizing resource use. Instead of the old “take, make, dispose” linear model, it aims to create closed loops in which materials are reused, recycled, and regenerated.
Pressure die casting perfectly fits this model. The process is well known for producing some of the most intricate metal parts ever made with amazing precision. It has many environmental benefits, including little wasted material and reduced energy. These parts, made by pressure die casting, are designed for disassembly and have the recycling factor interwoven, thus making up the core of sustainable manufacturing.
Sustainable Design in Pressure Die-Casting
1. Design for Disassembly
A key element of the circular economy is designing products that can be easily disassembled. When their time is up, each component can be individually removed for repair and/or recycling. Pressure die-casting excels at this. If the die can always produce parts with the correct geometries, it will be easier to disassemble them.
For instance, in the automobile and electronics industries, pressure die casting takes on the role of a major process in creating some of the modular components. A: These components are made to be taken apart quickly and easily so that you can melt down the metals (aluminum, zinc, magnesium) and reuse them for manufacturing. It decreases the volume of materials sent to the landfill and the use of natural raw materials.
2. Materials That Support Recycling
Metals used in pressure die-casting, such as aluminum and zinc, are inherently recyclable. Aluminum, for instance, can be recycled indefinitely without losing its properties. This aligns perfectly with the circular economy’s emphasis on resource regeneration.
In addition, because these metals are so highly recoverable, the energy used in extracting and producing them can be amortized over many lifetimes, remarkably lowering carbon dioxide emissions.
3. Lightweighting Without Sacrificing Strength
In industries like automotive and aerospace, lightweight materials are critical for improving fuel efficiency and reducing emissions. Pressure die-casting allows manufacturers to create lightweight yet durable components, meeting performance standards while contributing to sustainability goals. By reducing the overall material usage, pressure die-casting optimizes resource efficiency.
Environmental Advantages of Pressure Die-Casting
- Energy Efficiency in Production
Pressure die-casting consumes less energy than other forms of manufacture. By injecting molten metal into a mold at high pressure, this metal saves more material and is quicker to produce. Metals such as zinc and aluminum have lower melting points, so less energy is needed than alternatives such as steel.
- Reduction in Greenhouse Gas Emissions
Pressure die-casting considerably lowers greenhouse gas emissions due to its use of recycled metals and efficient energy use. For example, recycling aluminum requires only 5% of the energy needed to produce it from bauxite ore; the same is true for CO2 emissions.
- Waste Minimization
Pressure die-casting produces a near-net-shape product, unlike conventional manufacturing methods whose waste adds up to more than the part itself. That means parts need little post-processing, saving time and scrap.
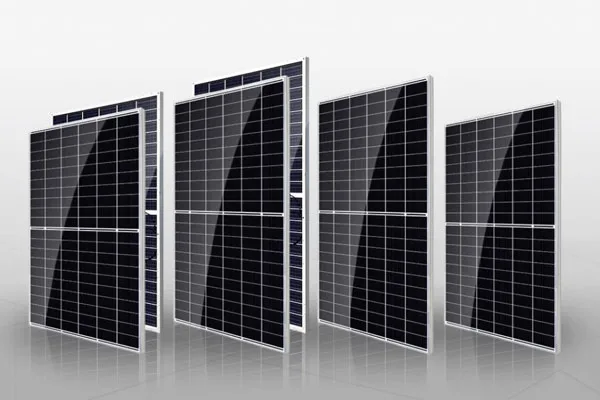
Solar panel modules
Innovative Applications Driving Sustainability
1. Automotive Industry
Die casting is used in the automotive industry to produce lighter components, such as engine blocks, transmission cases, and structural parts. The parts are engineered to be recyclable, so they can be disassembled and recycled when the car reaches the end of its service life.
2. Electronics
In electronics, pressure die-casting produces tough, recyclable casings and heat sinks. Because it can create complex objects without wasting material, it is an essential process for the future of sustainable electronics fabrication.
3. Renewable Energy
The renewable energy industry can also make use of pressure die-casting for the manufacture of certain wind turbine and solar panel components. Some of these parts are built so they can be used for many years and even recycled one day into something else to support a cleaner energy network.
Challenges and Opportunities in Sustainable Die-Casting
While pressure die-casting offers significant sustainability advantages, challenges remain. For instance, ensuring that recycling systems are efficient and widely adopted is crucial for maximizing the benefits. Manufacturers themselves must incorporate sophisticated technologies like auto-sortation and materials tracking to facilitate their recycling process.
However, the upside is that new developments in materials science and engineering will allow for even more sustainable practices in the future. Biodegradable core compounds for dies and molds and energy-efficient melting ovens are setting new standards in sustainable pressure die-casting.
A Circular Future with Pressure Die-Casting
As industries strive to meet sustainability goals, pressure die-casting stands out as a manufacturing method that seamlessly aligns with the principles of the circular economy. It is a prime factor in decreasing environmental impact by producing high-quality parts with minimal waste and a player because of its recyclable components.
The applications of pressure die-casting are huge, from parts for lightweight automobiles to modular electronic components. When manufacturers implement sustainable design principles, they are assuring that their products support a regenerative economy.
In conclusion, pressure die-casting is more than just a manufacturing process—it’s a pathway to a sustainable future. By prioritizing design for disassembly and recycling, industries can harness the full potential of this versatile technology, closing the waste loop and paving the way for a greener planet. Let’s make pressure die-casting the backbone of the circular economy!
Partner with Nice Rapid for Sustainable Pressure Die-Casting Solutions
Do you need a dependable partner who will help you achieve your environmental manufacturing dreams? Nice Rapid specializes in pressure die casting and prides itself on precision, efficiency, and environmental friendliness. Our expertise in sustainable design practices will ensure your products meet quality, not quantity, in a circular economy, reducing waste, enhancing recyclability, and achieving the highest standards.
Contact Nice Rapid today to discuss your next project and learn how we can help you meet your sustainability goals. Let’s create a greener tomorrow!