Pressure die casting is an essential manufacturing technique in the aerospace industry, used to produce lightweight, high-strength components critical to aircraft performance and safety. This process involves injecting molten metal into a mold under high pressure, creating complex, precise parts with exceptional durability. Here, we explore the fundamentals, advantages, and future developments of pressure die casting in aerospace.
The Fundamentals of Pressure Die Casting
Pressure die casting involves forcing molten metal into a steel mold, or die, under high pressure. Once the metal fills the mold and cools, the part is ejected. This method is beneficial for producing large volumes of precision-engineered components, often required in aerospace applications. Components made with this technique must meet rigorous standards for safety, performance, and weight.
Advantages of Pressure Die Casting in Aerospace
1. High Precision Manufacturing
One key advantage of pressure die casting is its ability to produce components with tight tolerances. The high pressure ensures the molten metal fills the mold, reducing defects like air pockets and voids. In aerospace, precision is critical—any minor imperfection can jeopardize a part’s performance and safety.
2. Lightweight, High-Strength Components
Pressure die casting allows for producing lightweight yet strong components, an essential requirement for aerospace parts. Alloys like aluminum, known for their strength-to-weight ratio, are commonly used. By producing lightweight components, aerospace manufacturers can enhance fuel efficiency, reduce overall weight, and improve performance while maintaining structural integrity. The ability to create durable, strong parts without adding unnecessary weight is why pressure die casting is so valued in the aerospace industry.
3. Fast Production Times
Another advantage of pressure die casting is its speed. Once molds are made, the process allows for rapid parts production, essential when aerospace manufacturers face tight production deadlines. The efficiency of this method makes it cost-effective while maintaining the quality required for aerospace components.
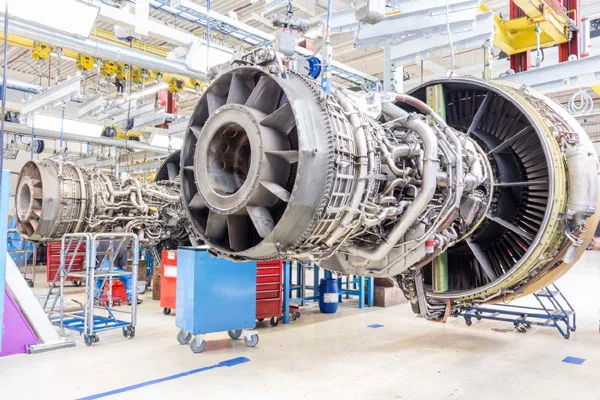
Aluminum die casting parts
Material Selection and Manufacturing Precision
Material selection is crucial in pressure die casting, particularly in aerospace. Aluminum alloys are often the material of choice due to their low weight, resistance to corrosion, and ability to handle high temperatures. Magnesium and zinc alloys may also be used depending on the component’s requirements.
Manufacturing precision in die casting is critical, and advanced computer-aided design (CAD) tools optimize the design before production. This allows manufacturers to ensure tight tolerances and enhance the final component’s quality.
Comparing Pressure Die Casting with Other Techniques
Pressure die casting offers superior precision and speed than other casting techniques, such as sand casting and investment casting. Sand casting, though versatile, results in rougher surface finishes and lower precision. Investment casting can achieve more complex shapes but is generally slower and more expensive. Pressure die casting balances speed, precision, and cost, making it the preferred choice for high-volume aerospace manufacturing.
Future Advancements in Die Casting
The future of pressure die casting in aerospace looks promising. AI-driven quality control systems are being integrated to monitor the casting process in real-time, improving accuracy and reducing defects. Additionally, emerging alloys, including titanium and advanced composites, promise to enhance aerospace components’ strength and lightweight nature, pushing the boundaries of performance and fuel efficiency.
Conclusion
Pressure die casting remains a critical technique for producing lightweight, high-strength components in aerospace manufacturing. Its precision, speed, and cost-effectiveness make it indispensable in creating reliable parts. As new materials and technologies emerge, pressure die casting will continue to evolve, ensuring its vital role in advancing the aerospace industry.