Companies use inexpensive approaches to assess products before mass producing them or when there is little demand. Three low-cost options include 3D printing, CNC machining, and Injection Molding. Each low-level manufacturing method has advantages and disadvantages and is used in various contexts.
Injection Molding is the first low process
Large quantities of products or parts are produced using injection molding. This is not a common production strategy for low-cost items that require quality improvement or have a high ID, such as medical devices, because of the high processing and equipment requirements. Casting materials with a longer service life, like aluminum or reinforced plastic, are employed in low-cost injection molding. Since large molds are composed of steel and can withstand the production of millions of pieces, they are more expensive. Low doses don’t work as well as bone marrow.
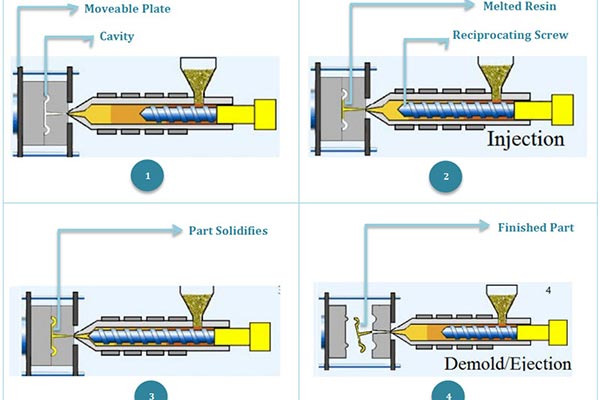
Plastic injection molding processes
The second Low-Volume Manufacturing Process is CNC milling
Rotary cutters are used in CNC milling, an advanced industrial method, to remove material from stock. Due to lower tooling costs, CNC machines may produce items faster and with lower startup costs than small-scale injection molding. When CAD files are converted to CNC programs and the machine is ready for operation, CNC milling production can start.
CNC machining might still take hours or even days, even if it is faster than injection molding. Sometimes an item needs special tooling, which is ordered from the machine shop before manufacturing starts. With the development of computer-controlled (CC) CNC milling machines, only trained professionals can carry out their tasks, including conceptualizing and designing the process, choosing the right tools and methods for the job, creating programs, installing them, and testing them. Cutting methods used by CNC machines are equally harmful.
3D printing is a low-volume manufacturing method as well
A form of additive manufacturing known as 3D printing uses materials to build something from scratch. Just like CNC milling, 3D printing uses CAD data to create the object directly. Additionally, compared to a CNC router, 3D printing requires no special tools and is far easier to use. Companies can either use their own 3D printer or work with a smart office that provides 3D printing services to use 3D printers to produce small-scale things.
Before initiating the 3D printing process, the designer has to produce a CAD file of the thing. 3D printers can handle more complex models, such as those with interior geometry or difficult-to-access locations. With great versatility, manufacturers can blend a variety of materials or components required for injection molding or CNC machining.
Assembly is accelerated by a lower part count, increasing manufacturing effectiveness and efficiency. A home computer or smart office receives the CAD file after it has been converted to a Standard Tessellation Language (.STL) file. 3D printing machine software reads the file and then divides its model into layers for printing. The usual length for the 3D printing process can generally range from several minutes to hours, depending on the size, setup, and printing method used. The manufacturing cycle is shorter than that of a CNC machine since 3D printing does not call for the insertion of parts and fasteners, while a modern 3D printer requires little to no handling. The additive process of three-dimensional printing uses less material than subtractive techniques.
With good design, the loss of supporting structures is reduced. In contrast to 3D printers, CNC machines have tolerances in the hundreds of inches, making them both expensive and exact. Numerous applications call for 3D printing, and the technology is continually evolving and increasing resolution and tolerance.