There are many different resins available for injection molding these days and each one has its own pros and cons. In this extended post, we thought it would be useful to explain the good and the bad so that you are able to make an informed choice when planning your next project. Even if we do not specify a material type here that you might want to consider, please discuss its use with your molding engineer who will have built up many years’ experience when it comes to assessing materials and their qualities.
Acetal –This is a fairly strong resin, With medium impact resistance and fair dimensional accuracy. It is fairly versatile and is able to accommodate small features with relative ease. It is able to withstand fairly high mold temperatures and is priced at the mid-level, so is fairly cost effective. An average all-round material with useful properties.
Acrylic – This is a common and mid-strength material with low impact resistance and good dimensional accuracy. It is fairly versatile and is generally capable of accommodating small features. It is good at withstanding high molding temperatures and is priced at the mid-level. An above average resin, which is well used throughout the industry for good reason.
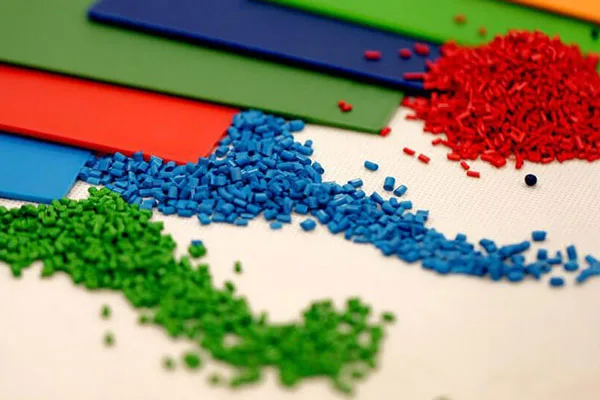
ABS materials
ABS – Acrylonitrile Butadiene Styrene has a low-to-medium strength, is very impact resistant and has good dimensional accuracy. It is just about capable of accommodating small features in the design and has a good performance at high mould temperatures. As a bonus, it is also a low-cost material so is a very well-used and highly versatile resin that is, Rightly, Very popular in the marketplace.
HDPE –High Density Polyethylene is not especially strong as materials go, but it does have high impact resistance and good dimensional accuracy. Its ability to accommodate small features in the design is not very high, although it does work well at higher mold temperatures. It also has a low cost and this has ensured that it is the go-to material for certain production runs requiring low strength, High impact resistance.
PC – Polycarbonate is a medium, Strength material with high impact resistance and good dimensional accuracy. It is generally capable of accommodating small features in molds and is well-suited to high molding temperatures. Unfortunately, the cost of the resin ranges from medium to high and this can mean it is not suitable for certain applications, even though it is plentiful and popular in the marketplace.
PC/ABS –Polycarbonate/ABS alloy is a fusion of two popular resins, which allows the benefits of both materials to be found in a single resin. This allows for medium strength and high impact resistance, As well as good to excellent dimensional accuracy. Even so, the accommodation of small features is not ideal, However, the material is able to withstand high molding temperatures. Cost-wise, the resin is of medium cost and so this makes it a more popular choice than Polycarbonate on its own.
PP – Polypropylene has low strength, but high impact resistance and this has made it a popular material in some quarters. The dimensional accuracy is fair and its capability to fill small features of molds is excellent, With good performance at high molding temperatures. It is also a low cost material and this, Along with its high impact resistance, Has made it common in the marketplace.
PS –Polystyrene has low-to-medium strength, Low impact resistance and good dimensional accuracy. It is able to fill small features of molds with ease and has good performance at high temperatures. Its other major benefit is that it is a low cost material, Allowing it to be used for a variety of cost conscious applications where high strength and impact resistance and not required, Such as in packaging.
So, as you can see, there are a number of materials that are available for use depending on the application that is required and the budget that must be accommodated. It is interesting to note that it is now common to blend resins in order to provide the benefits of more than one material in a single resin, Such as in the case of PC/ABS. This allows manufacturers even more flexibility and means that they are able to pass the benefits and cost savings along to their customers.
Firstly, it is important to consider the each individual property of the resin before deciding on whether to proceed with it as a material. Feel free to ask your manufacturer to produce a few samples in each material if you are unsure as to how a particular resin will work with your design or product. It is often only by trial and error that you might discover a material you had thought was not particularly suitable for the job able to fill the role admirably.
Secondly and as importantly, it is also important to not over specify the material that you wish to use in your project. If you only require low impact resistance, Low strength and low dimensional accuracy, then there is no point in purchasing a more expensive resin that handles these factors with ease – you would not use Polycarbonate for internal box packaging, For instance!
Finally, it is essential to always consider health, Safety and legislative requirements when choosing a material, in order to ensure that it is up to regulatory standards. Some products are required to be produced in specific resins in order to obtain certification and this is something that should be investigated as part of initial due diligence checks.
At NICE Rapid, We have a wealth of experience in rapid prototyping, Injection molding and tooling. We would love to hear about your next project!