The main pillar of any successful project is the creation of a prototype. Making a prototype is not a straightforward process, it’s for this reason that most companies are looking for alternative ways of making the process much more efficient.
Most prototypes used are mainly custom-made, one way in which you can create engineered parts and products is through prototype machining to validate your designs and ideas. Prototype machining is usually the preferred method for a wide range of reasons.
For this post, we are going to take a quick dive on everything prototype machining and why its vital in product development.
Quick low-down on prototype machining
Prototype machining is a process where functional parts are created to be copied in exact form and function before mass-production commences. There are extensive steps which tests the design to its limits to determine its viability as well as endurance.
If you want to achieve peak performance, then prototype machining is the way forward.
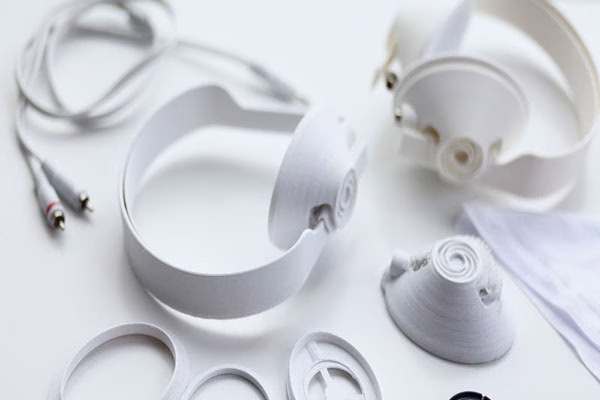
Prototype designs
Factors to be considered before choosing prototype machining
Currently, there are plenty of methods which can be used to create or manufacture prototypes. But for research and development purposes, engineers recommend using prototype machining. You might ask yourself why is this so? It’s because of quality and availability.
Here are some factors that you need to consider before using prototype machining.
Design requirements of the prototype
For those in the design team, the goal is creating designs that use standard parts, if the design still has unconventional requirements; you can decide to use machining. Another thing to note, you should factor in the complexity of your design, material wastage and total cost of the process
When you pay close attention to the above factored parts, your prototype machining will deliver precision, consistency, size and material.
Lead time and cost of machining
If you decide to go with prototype machining, you must know that not all the parts are created the same. Some may have more than one requirement for the machined parts. If this is the case, you should definitely increase the lead time as well as manufacturing cost for the project to be fully complete.
Machining process
One point of note that should be factored in is the machining process, not all the techniques have the capability of creating parts and products with specific geometry. When you go with multiple-axis CNC machines, this will require more investments as it’s made of intricate parts.
You can design the assembly but keep in mind it shouldn’t at any point interfere with the strength and functionality.
Bridging high volume production
After successful completion of the prototyping process, the next step is full production. The final finished part should be way cheaper to produce compared to prototypes. Thus, you’ll be looking for a process that is quite cheap and efficient.
One way of doing so is simplifying the machining process to make production cost-effective.