Sheet metal fabrication is a cornerstone of modern manufacturing, enabling the creation of everything from sleek electronic enclosures to robust industrial machinery. This versatile process transforms flat sheets of metal into precise, functional components using a variety of techniques, including cutting, bending, and shaping. As industries push the boundaries of technology, design, and sustainability, sheet metal fabrication remains a vital driver of innovation.
What is Sheet Metal Fabrication?
Imagine taking a flat sheet of metal – typically steel, aluminum, copper, or brass – and transforming it into a complex, three-dimensional object. That’s the essence of sheet metal fabrication. This process involves a combination of techniques:
- Cutting: Using lasers, plasma torches, or mechanical tools to precisely cut the metal into the desired shapes and dimensions.
- Bending: Skillfully shaping the metal into angles or curves using press brakes or rollers.
- Welding and Assembly: Joining different components together to create the final product.
- Forming: Using dies or molds to stamp or stretch the metal into intricate shapes.
The result is a highly versatile manufacturing method that produces durable, lightweight, and cost-effective components suitable for a wide range of applications.
The Evolution of Sheet Metal Fabrication
Traditionally, sheet metal fabrication relied heavily on manual labor and mechanical tools. While these methods were effective, they lacked the precision and efficiency required for today’s demanding applications. Thankfully, advancements in technology have revolutionized the process, making it faster, more accurate, and capable of handling increasingly complex designs.
- Automation and Robotics: Automated systems now dominate sheet metal fabrication, using computer-controlled machines to perform tasks with minimal human intervention. This boosts productivity, reduces errors, and enables high-volume production with consistent quality.
- CNC Machines: Computer Numerical Control (CNC) technology allows for unparalleled precision in cutting and shaping metal. With programmable tools, manufacturers can produce intricate designs and repeat them flawlessly across thousands of units.
- Laser Cutting: Laser technology has transformed cutting processes, enabling the creation of intricate patterns with incredible accuracy and minimal waste. This technique is particularly valuable for industries requiring high precision, such as aerospace and electronics.
- Sustainability: Modern fabrication methods focus on reducing waste and energy consumption. Efficient material use and recycling initiatives align with global sustainability goals, making sheet metal fabrication an environmentally responsible choice.
Applications Across Industries
Sheet metal fabrication plays a pivotal role in a diverse range of industries, thanks to its adaptability and the durability of the final products.
- Automotive: From the sleek curves of body panels to the structural integrity of chassis components, sheet metal is essential to automotive manufacturing. Its strength and lightweight properties contribute to improved fuel efficiency and vehicle safety.
- Aerospace and Defense: In aerospace, precision and reliability are non-negotiable. Fabricated sheet metal components, such as airframe structures and engine parts, must meet the industry’s rigorous standards for performance and durability.
- Electronics and Technology: As electronic devices become smaller and more complex, the demand for intricate metal parts continues to grow. Sheet metal fabrication provides the precision and scalability needed to create everything from electronics enclosures to server racks.
- Construction and Architecture: Sheet metal finds widespread use in architectural projects for roofing, cladding, and structural elements. Its versatility allows architects to create innovative and aesthetically pleasing designs without compromising on durability.
- Renewable Energy: The renewable energy sector relies on sheet metal fabrication for creating durable components for wind turbines, solar panel frames, and battery enclosures. These components must withstand harsh environments and provide long-lasting performance.
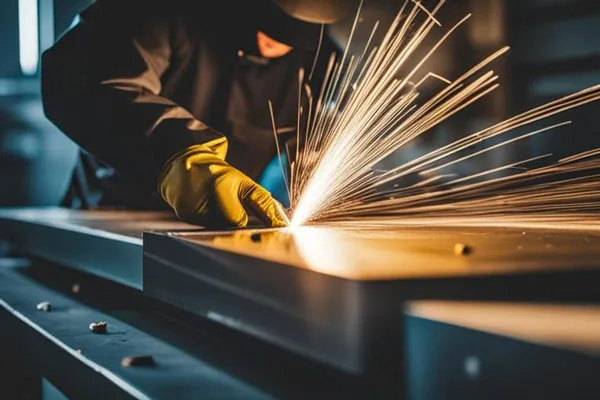
Sheet metal welding
Innovations Shaping the Future
Sheet metal fabrication is constantly evolving to meet the demands of modern industries. Here are some of the key innovations driving its future:
- Additive Manufacturing: Integrating additive techniques, like 3D printing, with traditional fabrication methods is opening up new possibilities for creating complex geometries that were previously impossible.
- Advanced Materials: Emerging materials, such as high-strength alloys and lightweight composites, are expanding the capabilities of sheet metal fabrication. These materials offer enhanced performance while reducing weight and cost.
- Digital Twins and Simulation: Using digital twins, manufacturers can simulate and optimize fabrication processes before production even begins. This technology improves efficiency, reduces waste, and shortens development cycles.
- Industry 4.0 Integration: The Internet of Things (IoT) and data analytics are enabling smarter, more connected fabrication systems. Real-time monitoring and predictive maintenance ensure that machines operate at peak efficiency, reducing downtime and costs.
Benefits of Sheet Metal Fabrication
Sheet metal fabrication offers a compelling array of advantages that make it a go-to solution for manufacturers:
- Durability: Fabricated sheet metal components are built to last, capable of withstanding extreme conditions, from high temperatures to mechanical stress.
- Cost-Effectiveness: Modern techniques minimize material waste and labor costs, making fabrication an economical choice for projects of all sizes.
- Flexibility: Sheet metal can be shaped into virtually any design, accommodating a wide range of applications and bringing creative visions to life.
- Sustainability: Recyclable materials and energy-efficient processes make sheet metal fabrication an environmentally responsible choice.
Shaping the Future
As technology continues to advance, sheet metal fabrication is poised to remain a cornerstone of manufacturing. From enabling precision in aerospace components to supporting sustainable energy solutions, this process is essential for meeting the demands of tomorrow’s industries.
Manufacturers that embrace innovation in sheet metal fabrication will gain a competitive edge, delivering high-quality, customized solutions that push the boundaries of design and performance.
Conclusion
Sheet metal fabrication is more than just a manufacturing process; it’s a gateway to innovation, sustainability, and excellence. By leveraging advanced technologies and materials, businesses can bend and shape the future, creating products that define the cutting edge of their industries. Whether you’re crafting intricate electronics enclosures or durable automotive parts, sheet metal fabrication is the key to turning bold ideas into reality.