Sheet metal is a versatile material used in countless applications, from consumer electronics to aerospace components. It refers to metal formed into thin, flat pieces, typically less than 6mm thick. Sheet metal fabrication involves various processes to cut, bend, and shape these sheets into desired forms. While the fundamental principles remain the same, sheet metal fabrication is constantly evolving with new technologies and techniques. This article explores the latest advancements and trends shaping the future of sheet metal work.
Laser Cutting of Sheet Metal
Laser cutting is a precise and efficient method for cutting sheet metal. It uses a high-powered laser beam to cut through the material, creating clean edges and intricate shapes.
Advantages of laser cutting for sheet metal:
- High Precision: Achieve tight tolerances and intricate cuts with minimal heat-affected zone, which refers to the area around the cut where the metal’s properties may be altered due to the heat of the laser.
- Versatility: Cut various sheet metal materials, including steel, aluminum, and stainless steel.
- Speed: Laser cutting is a fast process, ideal for high-volume production.
- Automation: Laser cutting machines can be automated for increased efficiency and productivity.
Laser cutting is a valuable tool for sheet metal fabrication, enabling the creation of complex parts with high accuracy and speed.
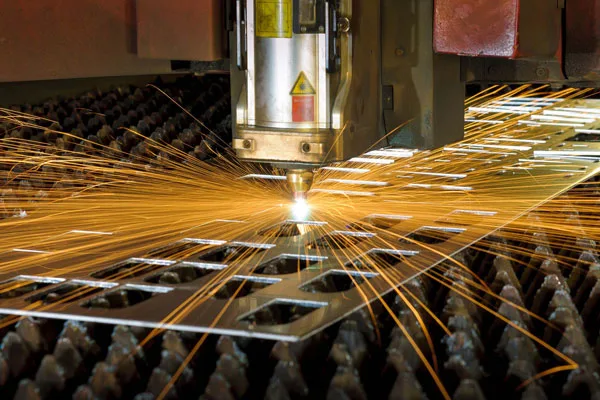
Laser cutting
Press Brake Bending for Sheet Metal
Press brake bending is a fundamental process in sheet metal fabrication. It involves using a press brake machine to bend sheet metal into various angles and shapes.
Here’s why press brake bending is essential:
- Press brake bending offers a world of possibilities. With this technique, you can create a wide range of bends, from V-bends to U-bends and even complex curves. This versatility empowers you to bring your design ideas to life in sheet metal.
- Precise Angles: Achieve accurate bend angles for precise part geometry.
- Efficient Production: Press brakes can be automated for high-volume sheet metal
Press brake bending is a crucial process for forming sheet metal components used in various industries.
Sheet Metal Forming with Hydroforming
Hydroforming is an advanced sheet metal forming technique that uses highly pressurized fluid to shape the material within a die.
Benefits of hydroforming for sheet metal:
- Complex Shapes: Create complex shapes and contours, such as irregular curves or deep drawn parts that are difficult to achieve with traditional bending methods.
- Improved Strength: Hydroforming can increase the strength and stiffness of sheet metal
- Reduced Tooling Costs: Hydroforming often requires fewer tools compared to stamping, reducing tooling costs.
Hydroforming is a valuable technique for producing complex sheet metal components used in automotive, aerospace, and other industries.
Automation and Robotics in Sheet Metal Fabrication
Automation and robotics are transforming sheet metal fabrication, improving efficiency, productivity, and safety.
How automation is used in sheet metal work:
- Robotic Welding: Robots can perform precise and consistent welding of sheet metal
- Automated Bending: Automated press brakes and bending machines increase bending speed and accuracy.
- Material Handling: Robots can handle and transport sheet metal sheets and parts, reducing manual labor.
By integrating automation, sheet metal fabrication shops can increase production capacity and improve overall efficiency.
Sustainable Practices in Sheet Metal Fabrication
Sustainability is not just a trend, it’s a responsibility. In sheet metal fabrication, manufacturers are adopting practices to minimize waste and reduce their environmental impact. By doing so, they are not only improving their own operations but also contributing to a more environmentally responsible manufacturing sector.
Sustainable practices in sheet metal work:
- Material Optimization: Optimize designs to minimize material usage and reduce scrap.
- Recycling: Recycle scrap sheet metal and use recycled materials whenever possible.
- Energy Efficiency: Implement energy-efficient equipment and processes, such as LED lighting, high-efficiency motors, and process optimization, to reduce energy consumption in sheet metal fabrication.
By adopting sustainable practices, sheet metal fabricators can contribute to a more environmentally responsible manufacturing sector.
Sheet metal fabrication is a dynamic and evolving field. By embracing new technologies, automation, and sustainable practices, manufacturers can improve efficiency, productivity, and competitiveness in the global marketplace. As the demand for complex and high-quality sheet metal components continues to grow, the industry will continue to innovate and adapt to meet the challenges and opportunities of the future.