In some specific weather conditions, even the most robust and tough metals are susceptible to corrosion. This can only take place when there is a reaction between the metal itself and the environment.
The corrosion will turn the metal surface of the metal into sulfide, hydroxide, and metal oxide. Every metal is susceptible to a certain degree of corrosion, though the reaction is not the same for every material; others react differently.
But the good news is, by using certain steps. Corrosion can be easily minimized by using certain steps, some of these steps include material selection, excellent product design as well as application on the surface treatment.
Minimizing corrosion
Some steps can be taken to minimize corrosion, most of these steps can either come before or after the manufacturing process. It’s also quite possible to minimize or fully reduce corrosion once the products are in use.
Using some of these steps does not mean they will last for eternity but it will enhance their strength and stability especially when it comes to CNC machining parts and products.
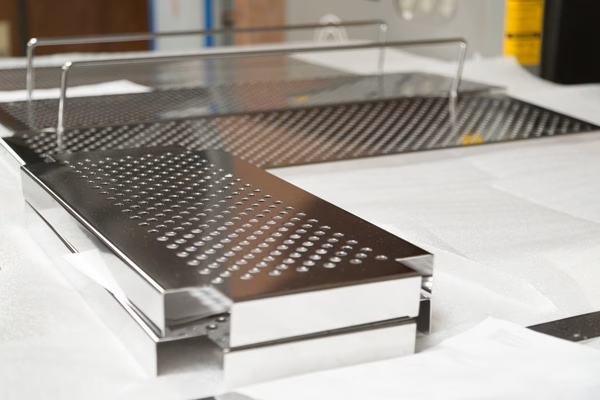
Electropolished shelving units
Choosing strong and robust materials
It’s a known fact that no metal material is virtually indestructible, but if the intended parts or products will come into contact with corroding substances or moisture; then it’s obvious that you should look for a corrosion-resistant material.
Stainless steel: The stainless-steel metal contains iron; iron can be easily oxidized to turn into rust. But it’s worth mentioning that steel has a relatively higher chromium content which is highly resistant to rust. Chromium creates a protective layer of chromium oxide on the surface
Aluminum: Aluminum doesn’t have iron; hence it won’t rust. The metal has a protective layer of aluminum oxide which forms on the surface of the part when there is contraction due to moisture thus preventing further corrosion.
Creating eco-friendly parts
The part materials will generally affect corrosion resistance, but it’s important worth noting that so do the texture and shape. Therefore, engineers and designers must factor in certain design features which will either encourage or discourage corrosion using the CAD design.
The design feature that traps air and moisture must be avoided at all cost, the parts must also not have deep crevices where airflow and moisture content thrive in.
Application of anti-corrosion coating
Application of this thin layer of coating has the ability to prevent further coating, by doing so moisture and air plus other corrosive substances do not come into direct contact with the metal unless there is wear and tear to the coating.
After a certain period, the coating can also be reapplied thus keeping further corrosion at bay. For those who are looking for cheaper ways of keeping corrosion at bay,, primer is the perfect solution.
Powder coating also has the capability of creating a protective layer of mainly plastic material that will enhance the look and appearance of your metal parts. Some of these powder coatings comprise of nylon, epoxy just to mention a few.