Embarking on the journey of crafting your own custom silicone molds can be an exhilarating endeavor. The world of silicone molding holds the promise of turning your creative visions into tangible masterpieces, but, like any craft, success lies in careful planning and preparation. In this comprehensive guide, we’ll take you through the intricacies of silicone molding, offering insights, tips, and tricks to ensure your foray into this versatile artistry is nothing short of a triumph.
Step 1: Concept
The genesis of any silicone molding project is a clear and inspired concept. Whether it’s drawn from a sketch, a photograph, a sculpture, or an everyday object, having a reference is crucial. Consider the size, shape, and level of detail of your envisioned mold, as these factors will influence the materials needed. This initial step sets the stage for the entire creative process.
Here are some things to keep in mind when developing your concept:
- Size: The size of your mold will determine the amount of silicone you need, as well as the size of your workspace.
- Shape: The shape of your mold will determine the type of mold release agent you need, as well as the complexity of the mold-making process.
- Level of detail: The level of detail in your mold will determine the type of silicone you need, as well as the amount of time and effort required to create the mold.
Once you have a clear concept in mind, you can begin to gather the materials and tools you will need to create your mold.
Step 2: Model
With your concept in mind, the next step is to materialize your vision into a physical model. Materials such as clay, wood, plastic, metal, or resin can be employed to bring your model to life. The model should be impeccably smooth and devoid of cracks or holes that might trap air bubbles during the silicone molding process. Compatibility with the chosen silicone is also a key consideration to prevent curing issues.
Here are some additional tips for creating a successful model:
- Use a high-quality modeling material that will hold up to the molding process.
- Make sure the model is accurately sized and proportioned.
- Smooth out any rough edges or imperfections.
- Remove any air bubbles from the model before molding.
- Test the model with the chosen silicone to make sure it is compatible.
Once you have created a successful model, you can move on to the next step: creating a mold.
Step 3: Mold Box
Creating a mold box is the pivotal stage where your model finds its containment. The mold box will be the final shape of your resin cast, so it is important to make sure it is the correct size and shape. You can use materials like cardboard, wood, or plastic to craft a box slightly larger than your model, allowing ample space for complete silicone coverage.
Once you have constructed your mold box, you will need to seal any gaps or seams to prevent leakage during the silicone pouring stage. You can do this by using a sealant like silicone caulk or duct tape.
Here are some tips for creating a mold box:
- Make sure the mold box is sturdy and will not collapse under the weight of the silicone.
- Use a level to make sure the mold box is flat.
- Seal any gaps or seams with a sealant like silicone caulk or duct tape.
- Be careful not to create any sharp edges on the mold box, as these could damage the silicone.
Step 4: Silicone
The star of the show is silicone—a rubber-like material consisting of a base and a catalyst. Carefully follow the manufacturer’s instructions to achieve the correct mixing ratio. Wearing gloves and working in a well-ventilated area is essential due to the sticky and messy nature of silicone.
Silicone is a versatile material that can be used for a variety of purposes, including creating molds for resin projects. It is available in a variety of colors and consistencies, so you can choose the perfect one for your project.
To use silicone for resin casting, you will need to mix the base and catalyst according to the manufacturer’s instructions. Once the mixture is ready, pour it into the mold and allow it to cure. Once the silicone has cured, you can remove the mold from the resin and use it to create your project.
Here are some tips for working with silicone:
- Wear gloves to protect your hands from the sticky silicone.
- Work in a well-ventilated area to avoid inhaling the fumes from the silicone.
- Clean up any spills immediately to prevent the silicone from hardening.
- If you need to thin the silicone, you can add a small amount of isopropyl alcohol.
- Be patient! Silicone takes time to cure, so don’t try to rush the process.
With a little patience and care, you can create beautiful and unique resin projects using silicone.
Step 5: Pouring
Pouring the prepared silicone into the mold box requires a steady hand and a meticulous approach. Starting from one corner and progressing methodically across the mold box, pour slowly to avoid the formation of air bubbles. Techniques like pouring from a height or gentle tapping of the mold box can further mitigate the risk of air entrapment.
Here are some additional tips for pouring silicone into a mold box:
- Use a funnel to help guide the silicone into the mold box. This will help prevent spills and make it easier to control the flow of silicone.
- Pour the silicone slowly and steadily. This will help to prevent air bubbles from forming.
- If you see any air bubbles forming, use a toothpick or skewer to gently pop them.
- Once you have finished pouring the silicone, tap the mold box gently on a flat surface to help release any air bubbles that may be trapped.
- Allow the silicone to cure completely before removing it from the mold box.
Step 6: Curing
Allowing the silicone to cure is the most patient phase of the mold-making process. This is the time when the material solidifies into a rubbery mold. Curing times vary based on the type of silicone, brand, and environmental conditions. It is important to adhere to the manufacturer’s instructions for curing times, as curing too quickly or too slowly can result in a defective mold.
During the curing process, it is important to avoid any disturbance to the mold box. This can cause the silicone to crack or deform, which will ruin the mold. If you need to move the mold box, do so carefully and slowly.
Once the silicone has cured, you can remove it from the mold box. Be careful not to damage the mold when you remove the silicone. If the silicone is stuck to the mold, you can use a heat gun or hair dryer to soften it. Once the silicone is soft, you can carefully remove it from the mold.
Now that you have a mold, you can use it to cast your project.
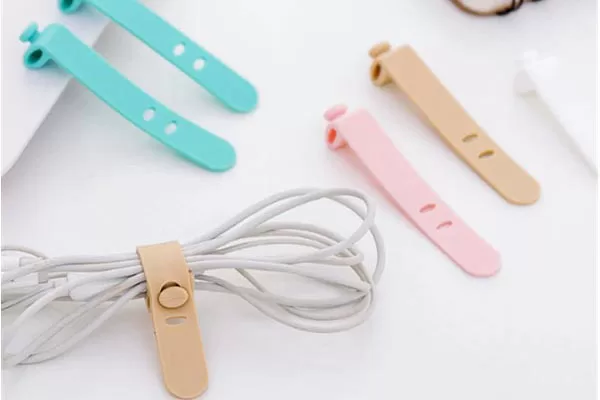
Silicone cable ties
Step 7: Demolding
Once the silicone has fully cured, you can de-mold your model. To do this, carefully remove the mold from the mold box. Trim away any excess silicone that may have overflowed. Then, carefully separate your model from the silicone mold, taking care not to cause damage. For multi-part molds, you may need to use a knife or scissors to cut along seam lines.
Here are some tips for demolding:
- Work in a well-ventilated area.
- Wear gloves to protect your hands.
- Use a sharp knife or scissors to cut along seam lines.
- Be patient and gentle.
- If you are having trouble demolding, try heating the mold slightly to soften the silicone.
Once you have successfully demolded your model, you can clean it and paint it as desired.
Step 8: Casting
Congratulations! You’ve successfully created your custom silicone mold. Now, the mold becomes the vessel for casting various materials—resin, plaster, wax, soap, chocolate, and more.
To cast your chosen material, follow these steps:
- Prepare your casting material according to the manufacturer’s instructions.
- Pour the casting material into the mold, leaving about 1/2 inch of space at the top.
- Allow the casting material to cure completely, according to the manufacturer’s instructions.
- Carefully de-mold the casting, being careful not to damage the mold.
- Finish your casting as desired.
Here are some tips for successful casting:
- Use a clean, dry mold. Any dirt or grease on the mold will prevent the casting material from adhering properly.
- Pour the casting material slowly and evenly into the mold. This will help to avoid air bubbles.
- Allow the casting material to cure completely before demolding. If you de-mold the casting too early, it may be damaged.
- Be careful when demolding the casting. Use a sharp knife or razor blade to loosen the casting from the mold, being careful not to damage the mold.
- Finish your casting as desired. You can paint, sand, or polish the casting to create a finished product.
With a little practice, you’ll be able to create beautiful and unique castings using your custom silicone mold.
Step 9: Finishing
The final touch involves perfecting your casted object. Trim away excess material, sand down any rough edges, and unleash your creativity through painting or decorating. A clear coat or varnish can be applied for added protection against scratches or stains.
Here are some tips for finishing your cast object:
- Trim away excess material. Use a sharp knife or scissors to trim away any excess material from your casted object. Be careful not to damage the object itself.
- Sand down any rough edges. Use fine-grit sandpaper to sand down any rough edges on your casted object. This will help to create a smooth, polished finish.
- Paint or decorate your object. Once you have trimmed and sanded your object, you can paint or decorate it however you like. You can use acrylic paint, spray paint, or even fabric paint to create your own unique design.
- Apply a clear coat or varnish. A clear coat or varnish can help to protect your casted object from scratches and stains. It will also help to give your object a glossy finish.
Conclusion
In conclusion, you’ve now navigated the intricate process of crafting custom silicone molds, from conceptualization to creation. We trust this guide has been both enjoyable and informative, providing you with the knowledge to embark on your silicone molding adventures. If you have any questions or insights to share, please feel free to leave them in the comments below. Happy molding!