The process remained unchanged and it involves putting the rubber compound into a mold that takes the shape of the intended product. Its resulting product is slightly larger than what would be its final shape. Compression molding uses pressure and heat to thermoset the plastic resin or rubber into its form. A process called vulcanization takes place, and that gives the rubber resin the ability to take the shape of the mold. The part extracted from the molding tool tends to shrink until it reaches the standard size.
Compression molding is used in making a variety of products, including wellington boots, seals, gaskets, machinery parts, even the door stopper that you used and the feet of your chairs. This process can use the mold multiple times, and thus it is appropriate for medium to large volume production.
Here are some of the benefits and drawbacks of using the compression molding process to see if it’s right for your company and your product.
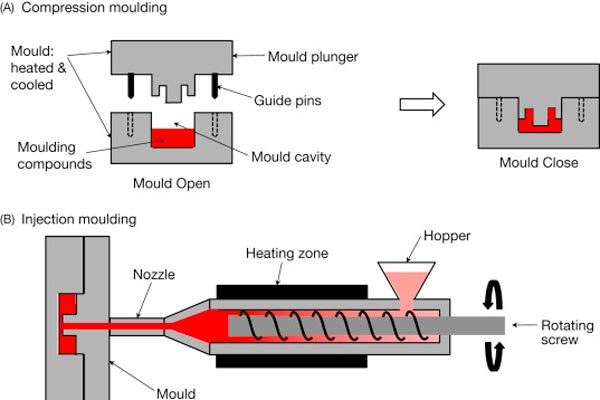
Compression molding process
Benefits of Using Compression Molding
- It has a low tooling cost. Because compression molding does not involve injection or transfer in its cycle, the tooling requirement is lesser compared to other molding processes. There are no complicated features needed other than the cavity that will mold the material.
- It is best for small production requirements. The cost of the molding tool and setting up the process is relatively, and therefore, it can match the budget for short production runs.
- There are no sprues, runners, or gates needed in compression molding. Other molding processes may use gates, runners, and sprues for the materials to pass through before it can enter the cavity, but compression molding does not require any of them. You will have additional cost savings on your material because it will go directly into the mold.
- It is the best method for manufacturing large parts. Compression molding can accommodate a large chunk of material because it goes directly to the cavity. There is also no limit on the weight of the part to be manufactured compared to injection molding.
The Drawbacks of Using Compression Molding
- There is a more significant waste. This method is not as precise as injection molding, and therefore you should expect the cavity to be overfilled. It also needs to remove the excess air from the cavity with the excess material; this contributes to more significant wastage. Waste from compression molding cannot be reused too.
- It has a high labor cost because it needs more workforce as it does not run on full automation.
- It has a slower processing time. The thermal conductivity of resin and rubber is poor, leading to slower curing speed.
- It cannot accommodate complex geometries. Compression molding is more appropriate for a product that has more straightforward and larger products.
- It is prone to contamination. The uncured compound used in this process can pick up dirt that will be pressed and cured by the surface.
The process of compression molding can be ideal for manufacturing your products if it is used appropriately, with all the aspects of the requirement adequately scrutinized.