Today, it seems as if everything is becoming disposable. As a result, people are constantly looking for ways to avoid cleaning up after themselves, from plastic water bottles to Ziploc bags. While this mentality may be convenient in the short term, it is not always the best solution for the environment or our wallets.
Plastic injection molding is one way to create durable and long-lasting products without hurting the planet. Here are just a few of the benefits of using this manufacturing process:
1. Injection molding can create exceptionally durable and aesthetically pleasing products.
In injection molding, melted plastic is injected into a mold, where it cools and hardens to take on the desired shape. This process can be used to create durable and aesthetically pleasing products.
In addition, injection molding can create products with complex shapes and features that would be difficult or impossible to produce using other methods. As a result, injection molding is an extremely versatile manufacturing technique that is used in a wide variety of industries.
Injection molding is also relatively quick and efficient, making it an ideal choice for mass production. Thanks to its many advantages, injection molding will continue to be a popular manufacturing method for years.
2. It is an environmentally friendly process that uses minimal resources.
Recycling is not only good for the environment; it’s also good for your wallet. It’s an environmentally friendly process that uses minimal resources and helps reduce the amount of waste sent to landfills each year.
Recycling conserves energy and natural resources, reduces pollution, and creates jobs. So next time you’re about to throw away that soda can or water bottle, think twice—you might be surprised at how easy it is to recycle.
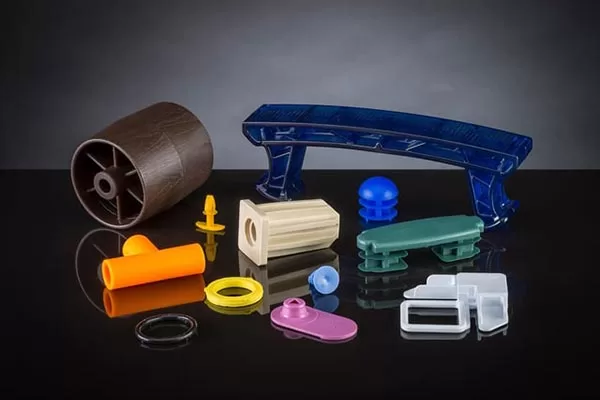
Plastic products
3. Injection molded parts can be made quickly and efficiently with little waste.
Injection-molded parts are often used in applications where speed and efficiency are key. The injection molding process involves injecting molten material into a mold cavity, allowing it to cool and solidify. In contrast to other manufacturing methods, injection molding is relatively quick and requires little material waste.
In addition, the process can be easily automated, making it ideal for high-volume production. As a result, injection molded parts are often used in various industries, from consumer electronics to automotive applications.
4. The final product is uniform and of high quality.
If you’re looking for a more sustainable way to produce your products, injection molding may be the perfect solution!
Final Thoughts
The modern world is full of plastics. From food packaging to medical equipment, it’s everywhere. And it’s not going anywhere anytime soon. A big reason for this is that plastic is extremely versatile. It can be molded into all shapes and sizes, which is why it’s used in everything from toys to car parts.
The process of making these products is called plastic injection molding. And it results in a final product that is uniform and of high quality. Injection molding is done by melting plastic pellets and injecting them into a mold. The molten plastic then cools and hardens, taking on the shape of the mold.
The process can be repeated, allowing for the mass production of high-quality plastic products. So, the next time you pick up a plastic toy or eating utensil, remember that it results from a fascinating manufacturing process.