Sheet metal is a versatile material because you can make it into different forms. This versatility is also the reason why there is an increasing demand for its different fabrication processes. One of these processes is sheet metal bending.
The fabrications type may sound simple and it may involve bending the sheet metal into the desired form but there are many processes involved to make this happen. If you want to know if sheet metal bending is the right technique for your project, then you better read this article.
What is Sheet Metal Bending?
Sheet metal bending is a process that involves using force to form or shape a piece of metal. The external force applied to the material changes its external features while keeping the length and shape of the metal.
In sheet metal bending, the malleability of the metal impacts how it can be processed into different forms. The process is essential in the metal processing industry owing to its many applications. It is used in manufacturing engine parts and automotive parts.
Here are five of the best processes that should be observed in sheet metal bending.
1. Reducing Displacements
In bending sheet metal, you need to have an ergonomic work area around the press machine to facilitate easy loading and unloading of the materials. There should be a short distance between the hydraulic press and the sheet metal for easy access.
Also, all the materials needed in the bending process must be prepared ahead of time. Being organized can help you save time in completing the process.
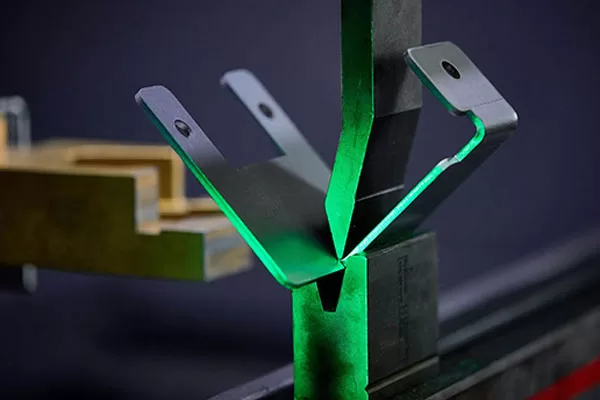
Sheet metal bending
2. Choosing the Right Press
There are manually operated hydraulic presses for bending sheet metal, but this machine is already outdated. A more effective workflow has modern hydraulic presses in different models including Elec-draulic II, Elec-draulic II, Single Phase Dura-Presses, and the Three Phase Dura-presses. These machines operate on electric power and come in different strengths and sizes.
3. Create a Standard Operations Manual
It does not matter whether you are working alone or as a team of operators, you need to write down the standard bending procedure to maintain the consistency of your products. Create a step-by-step guide about the machining operations. It will also help them answer any possible questions when dealing with sheet metal.
4. Being Proactive
The sheet metal bending process may be simple but several issues may come up. Hence, all operators should take a proactive approach when they are on the shop floor. For example, when the production is slow, they should find out the root cause of the problem. If the problem keeps on repeating, try to address the issue. By being proactive, they can address any potential issue before they become full-blown problems.
5. Learn and Communicate
Metalworking is an ancient process but there is still a lot to learn. The technology is evolving and even if the operator has plenty of years of experience in bending metal there are new techniques to learn to improve productivity.
Should you have further questions about sheet metal bending or you have a project requiring the process, get in touch with the experts at Nice Rapid. They are happy to discuss the project with you.