The rapid prototyping process involves the production of components for use in prototype models before entering the mass production phase. Manufacturing partners can produce prototype components in a variety of surface finishes, depending on customer requirements.
There are plenty of finishing techniques, from spray painting and anodizing to manual trimming. The aim of the finishing process is to match brand or product requirements. With a wide range of finishing services, settling on the right choice for your project might seem overwhelming.
This post unpacks the finishing processes available for rapid prototyping projects.
What Is the Purpose of Surface Finishing?
Enhance the Look & Feel of the Finished Product – Surface finishes allow manufacturers to choose the ideal finishing option to create the right look and feel in the final product. There are options to add textures, graphics, and color to improve aesthetics.
- Preserve Functionality & Appearance – Surface finishes can improve component service life and longevity while preserving its surface and color.
- Maintain Production Quality – Component surface finishes conform to customer specifications and create a functional surface.
Production processes involving SLA components impart a high-quality finish for surfaces during manufacturing. Going forward, manufacturers looking to create a part for prototypes and concept designs require a “production finish.”
Where simple 3D parts are required for concept modeling purposes, achieving a high-quality standard finish in a short timeframe with minimal hand finishing is possible. It’s also possible to achieve a high-quality production finish with SLA parts and other 3D printing manufacturing processes, such as FDM or SLS, and with vacuum-casted or CNC components.
The outcome depends on if the prototyping manufacturer has the in-house facilities and skills to offer a complete surface finishing service. The requirements and specifications for achieving a production quality finish through the following processes.
- Surface texture & smoothness – Blasting and sanding impart different finishes.
- Color matching – Hand or spray painting, including RAL or Pantone matching.
- Tinting – Determined by the resin used in the production process.
- Coatings – Shielding, plating, and durability coatings.
- Functional elements – The addition of a functioning assembly or inserts.
Many rapid prototyping companies produce SLA components with a “normal” or standard” surface finish. However, guidelines for these finishes can vary between manufacturing partners. So, it’s advisable to research what the manufacturer considers standard or normal finishes.
Typically, the faster the production turnaround for the prototype, the lower the quality of the surface finish. However, these finishes are usually suitable for prototyping projects requiring one-off components for modeling and proof-of-concept.
The type of resin used in production determines whether the manufacturer can implement a tinted or clear surface finish for production components. Before undertaking and approving production processes, the customer must enquire about resin properties and range before approving projects.
The more detail in the finish, the higher the production costs and the longer the lead time required to produce and finish the tooling.
Let’s unpack the common types of surface finishing available to prototyping projects.
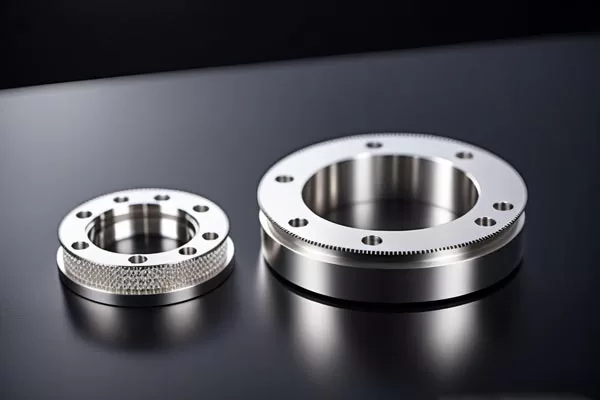
Bead blasting cnc parts
Spray or Hand Painting
Manufacturers offer a range of painting finishes for prototype production. Effective surface preparation before going to paint is the key to successful finishing using this technique. Ensuring proper surface preparation achieves an appropriate foundation for painting and the best results for prototype components.
It’s critical for manufacturers to use adequate masking strategies to ensure tight, clean lines during painting. It’s also important for manufacturers to utilize high-quality paints and coatings suitable for the component’s surface.
Painted surfaces come in various finishes providing different visual effects to the final component. Some of the painted finishes available include the following.
- Soft-touch
- Semi-gloss
- High-gloss
- Matte or Flat
- Satin
Pad Printing
This printing method allows for the easy transfer of 2D images onto 3D objects. This production technique utilizes silicon pads to collect and transfer inks from printing clichés to production components.
The manufacturer tailors the pads to the size and shape of the component’s geometry. It’s possible to add custom colors and artwork featuring several different color finishes. Pad printing is a durable process and assists with product branding, identification, and decoration.
Pad printing offers manufacturers a flexible option they can apply to several surface designs, including the following.
- Convex, concave, spherical, cylindrical, and flat surfaces.
- Textured surfaces and compound angles.
Surface Finishing Treatments
Surface finishing treatments utilize industrial processes that alter material surfaces to achieve the desired look for components. These surface treatments are typically used to improve chemical or corrosion resistance, remove surface flaws like burrs, or improve the final aesthetic of finished parts.
There are several surface treatment options for rapid prototyping projects.
- Bead blasting.
- Anodizing.
- Brushing.
- Electro-polishing.
- Copper Shielding.
- Hydro-graphics.
- Mold-tech texture.
- Plating.
- Passivating.
- Tumbling.
- Vapor honing and polishing.
The Final Thought
Selecting the right manufacturing partner for your rapid prototyping project is crucial. Since finishing grades can vary between manufacturers, assessing partners and the results they can offer for your prototypes is essential for success.