Silicone rubber molding has become an increasingly popular choice for businesses that require low-volume production runs. This process is ideal for producing high-quality, precision parts that meet strict tolerances, without the need for expensive tooling or equipment.
In this blog post, we’ll explore the importance of silicone rubber molding in low-volume production and how NICE Rapid has become a leading expert in this field.
Benefits of Silicone Rubber Molding
Silicone rubber molding offers several benefits for low-volume production, including:
Cost-effectiveness
Silicone rubber molding is a cost-effective solution for producing small to medium-sized production runs. Unlike other manufacturing processes, such as injection molding, silicone rubber molding does not require expensive tooling or equipment. This makes it an ideal solution for businesses with limited budgets. Additionally, silicone rubber molding can produce complex shapes and designs with high accuracy and consistency. Silicone rubber is also durable and resistant to heat, chemicals, and weathering, which reduces the need for maintenance and replacement. Therefore, silicone rubber molding can save time and money in the long run.
Precision
One of the advantages of silicone rubber molding is that it can produce parts with high precision and tight tolerances. This means that the parts will fit exactly with the specifications and requirements of the product. Silicone rubber molding is ideal for businesses that need high-quality, precision parts for their products, such as medical devices, electronics, automotive components, and more.
Flexibility
One of the advantages of silicone rubber molding is its flexibility. Flexibility refers to the ability to design and produce parts that are customized to the requirements of each project, using a variety of materials and colors. Unlike other manufacturing methods that have fixed molds and limited options, silicone rubber molding can create complex shapes and sizes, as well as incorporate different features and functions. This gives businesses more control and creativity over their products, and reduces the need for secondary operations or modifications.
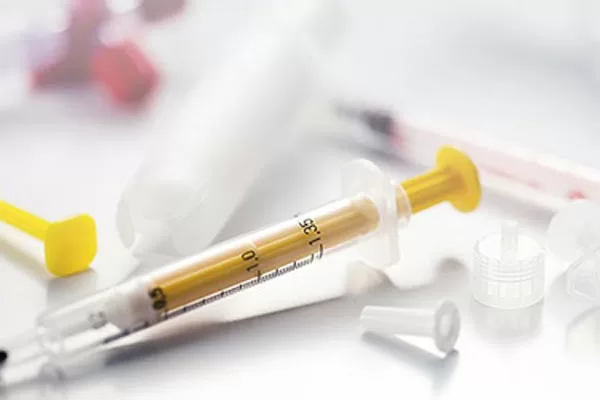
Silicone medical parts
Applications of Silicone Rubber Molding
Silicone rubber molding has a wide range of applications in various industries, including:
Medical devices
Silicone rubber molding is commonly used to produce medical devices, such as seals, gaskets, and tubing. This is because silicone rubber is biocompatible, non-reactive, and can withstand a wide range of temperatures and sterilization methods.
Automotive
Silicone rubber molding is also used in the automotive industry to produce components such as seals, gaskets, and hoses. Silicone rubber can withstand extreme temperatures and is resistant to chemicals, making it ideal for use in engine components.
Electronics
Silicone rubber molding is used in the electronics industry to produce components such as keypads, gaskets, and seals. Silicone rubber is an excellent insulator and can protect electronic components from moisture, dust, and other contaminants.
NICE Rapid: An Expert in Silicone Rubber Molding
NICE Rapid is a leading provider of silicone rubber molding services, with years of experience in this field. Their team of experienced technicians and qualified managers can help businesses determine if silicone rubber molding is the right solution for their specific production needs.
NICE Rapid uses state-of-the-art equipment and techniques to produce high-quality, precision parts that meet strict tolerances. They also offer a wide range of materials, including medical-grade silicone rubber, to meet the unique needs of their clients.
Conclusion
Silicone rubber molding is an excellent solution for businesses that require low-volume production runs. It offers several benefits, including cost-effectiveness, precision, and flexibility. With the help of an experienced provider like NICE Rapid, businesses can leverage the benefits of silicone rubber molding to meet their production needs.