The vacuum casting or Urethane Casting process is known for manufacturing injection molded parts in small quantities. It can manufacture parts with the quality of injection molding process without much financial investment on tooling.
The process involves producing parts under vacuum using plastic or rubber components from silicone molds. The parts made using vacuum casting are highly accurate, with high fidelity to the pattern in terms of profile and texture.
The Vacuum Casting Process
The vacuum casting process starts with the creation of the master model using stereolithography. Once the SLA model is completed or finished to achieve the customer’s specification on the surface texture. There is another option for the master model. A customer may be the component for casting and no initial processes are carried out at this stage. This is called the master pattern.
The master pattern is fitted with a casting grate and suspended in a mold casting frame. It is then poured over with silicone material to make the silicone mold. The whole setup is then cured in the heating chamber and removed by cutting along the parted line.
After this process, the master pattern is taken out of the mold, poured with a new resin to be cast, and sealed closed. This mold is returned to the heating chamber and cured. At this stage, a final product is ready for finishing and the silicon mold is ready for reuse.
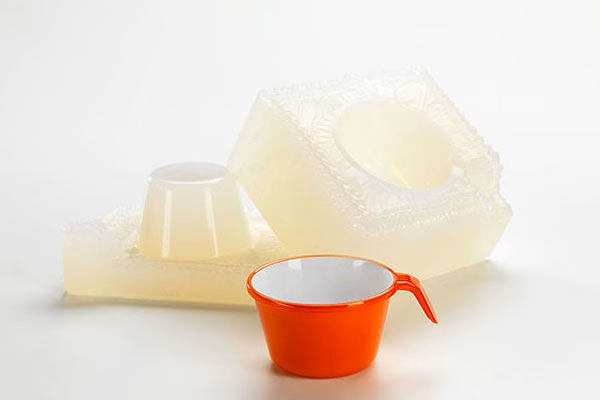
Vacuum casting cups
Benefits of Vacuum Casting
This manufacturing process is a preferred technique for prototyping because of its many advantages. Let us take a good look at some of them.
- Fast production: The silicone molding used in vacuum casting is easy to make (even in one day). Therefore, it is more timesaving compared to CNC machining or 3D printing.
- Low production cost: The tooling used in other production processes like aluminum is more expensive than silicone. Another cost factor is the amount of cut material when using the subtractive way of creating a mold. With vacuum casting, you can copy parts without material wastes.
- Simulation of materials: With polyurethane, you can simulate most material properties. It also achieves the same effect as other manufacturing techniques.
- Consistency: Part consistency is critical for testing. Using vacuum casting will ensure that every part copies the features of the master model.
- Excellent surface finish: Unlike 3D printing or CNC machining, vacuum cast parts do not require further finishing.
Limitations of Vacuum Casting
While there are plenty of benefits that manufacturers can enjoy by using vacuum casting it also has its limitations.
- Restriction on Production Volume: Vacuum casting is not designed for high volume production as the silicone mold has a short lifespan. The maximum it can produce is up to 50 parts. Further usage can result in shrinkage and inaccuracy.
- Loose Tolerance: Aside from shrinkage of the silicone mold, vacuum casting is not ideal for creating precise parts.
- Continuous Flaw: Molding can result in continuous flaws. However, unlike in CNC machining or 3D printing, you cannot check and improve on the parts separately. The master model and the silicone mold are the two factors that are connected to the flaw. The cost of production will be high if flaws happen.
- Potential Hollowness or Bubble Issue: Another risk in using vacuum casting is in curing. Here the outer side cools faster than the center. It is an issue when creating a part with thick walls.
Vacuum casting has its shortcomings. However, it is very useful in rapid prototyping for its speed in production, low cost, and low volume. Furthermore, for small companies, low volume production using vacuum casting can help them with cash flow and iterations of the products.