There are three methods of sheet metal fabrication, each with several sub-methods. This post walks you through each method in detail.
1 Cutting Techniques for Sheet Metal Fabrication
Cutting is the primary phase of sheet metal fabrication. There are two types of cutting techniques: cutting with and without shear.
Non-Shear Cutting Techniques
Plasma Cutting
This thermal cutting method uses ionized gas (plasma). It creates oxidation zones and burrs at the cut area. It provides fast cutting and excellent repeatability on electrically conductive metals.
Laser Cutting
This method is suitable for non-ferrous metals, including stainless and mild steel. The first process involves using high-powered lasers to vaporize metal. The second is blowing nitrogen or oxygen gas with a cutting nozzle to prevent splashing the processing head.
Waterjet Cutting
This process utilizes high-pressure water streams (60,000 psi, with a velocity of 610m/s) to cut. It’s versatile and suitable for various soft and hard materials.
Shear Cutting Techniques
Shearing
This process is ideal for high-volume, straight-line cutting of soft materials like aluminum and brass. It applies shear force to the surface, splitting the material at the cut point. It’s ideal for cutting straight edges on sheets featuring rough edges.
Blanking
This process involves removing sheet metal from larger pieces of stock material with a die and punch. It’s ideal for economical part fabrication due to its dimension control, high repeatability, and accuracy.
Punching
This process utilizes shear force to punch holes in sheet metal. It’s ideal for making holes and cutouts, but properly matching the punching knives and dies requires more manufacturing time.
Sawing
This process utilizes a sawtooth tool to create friction and shear force, tearing apart the material. Band saws are ideal for materials like aluminum, brass, and non-ferrous metals. Horizontal band saws are suitable for cutting long bar stock, and vertical band saws are the better choice for cutting contours.
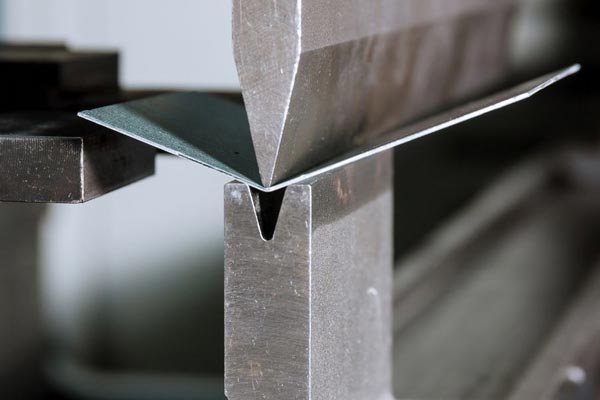
Sheet metal forming and bending
2 Forming Techniques for Sheet Metal Fabrication
Rolling
This process passes the material through rollers, reducing its thickness to a balanced consistency throughout the sheet. It involves hot and cold rolling techniques. Cold rolling occurs at room temperature, while hot rolling occurs at temperatures over the metal’s re-crystallization threshold.
Bending
This process is ideal for low to mid-scale production volumes. It deforms the surface, bending it at required angles using a rolling machine and press brakes. It’s suitable for materials like copper, spring steel, and aluminum 5052.
Stamping
This process incorporates forming and cutting processes with short fabrication methods for complex component fabrication. Stamping is a cold-forming method utilizing dies and presses to shape materials.
It’s compatible with low—and high-carbon steel, aluminum, copper, and brass. It’s a fast, cost-effective process requiring few tools and less labor than other methods. The process can be automated for repeatability, but operating costs are higher, and it’s challenging to make changes during the production process.
Curling
This process joins hollow, round rolls to the edges of sheets in three phases. Phases one and two form curves for curling, and the third closes the curl. Curls remove sharp edges from untreated workpieces, making them safe for handling while strengthening the material. However, they can result in material deformation and burring, requiring careful monitoring during the process.
Hemming
This process involves rolling sheet metal edges back onto themselves, forming areas with dual layers. It’s a two-phase process: The first phase blends the sheet and lowers it into the V-die. The second phase removes the material, placing it into the flattening die to flatten and shape the hem. Hemming strengthens the edges of parts and enhances appearance. It’s suitable for creating parts with high-level finishes. However, it can generate deformation in the material, resulting in dimensional variation.
3 Joining Techniques for Sheet Metal Fabrication
Riveting
This process drills holes into metal sheets, joining them with rivets. The operator inserts the rivet into the drilled hole and squashes its tail, deforming it to secure the sheets together. It’s suitable for non-ferrous metals like copper and aluminum. There are two forms of riveting. Cold riveting is better for lightweight and non-ferrous metals with diameters under 10mm. Hot riveting applies heat ranging from 1,000 to 1,100ᵒC to rivets greater than 10mm.
Welding
This process joins steel sheets using a torch to heat them to the melting point where they fuse. It’s a fundamental process implemented in the final phases of sheet metal fabrication and engineering. Fabricators use three types of common welding techniques in sheet metal fabrication projects.
- TIG – (Tungsten Inert Gas) welding.
- MIG – (Metal Inert Gas) welding
- SMAW – (Shielded Metal Arc Welding).
Each technique takes a different welding approach, but they all join metals through the process of melting edges and applying fillers to form metallurgical bonds between sheets.
In Closing
Depending on the project requirements, many fabrication projects can incorporate all three processes of cutting, forming, and joining. Choosing a full-service engineering service keeps the entire project in-house, reducing costs and manufacturing times.