Vacuum casting is a popular manufacturing method used by many workshops in the machining industry. Vacuum casting is the usual go-to method of manufacturing to create small batches of resin parts very quickly with the same efficiency of larger production runs.
You can get the same quality product you would get in an industrial run at just a ration of the expense. Vacuum casting is also prominently used top create prototype tests of larger products. It can also be used for producing the small components of a larger mechanism.
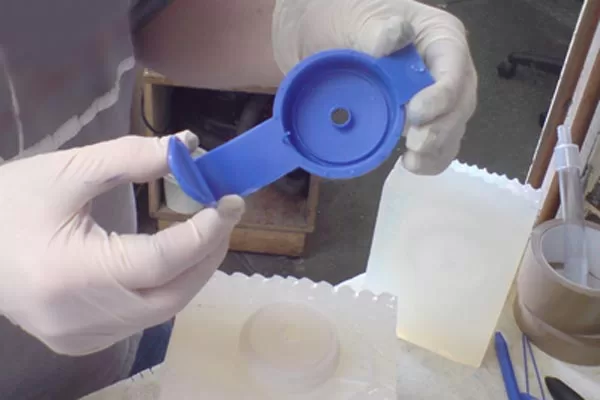
Vacuum casting product
A Sought After Procedure
This procedure is held in high regard to achieve high standards of quality since it can deliver exact replicas of anything that is created using a master mold. All of the secrets of vacuum casting are contained in the inner chamber. The empty space is where our product comes to be in a compression process that removes bubbles and other impurities that come in the molten resin.
Vacuum casting can deliver a lot of detail on the surface of any product, especially if you use molten plastics. You’ll be able to shape blemish-free surfaces and make your products with the desired properties. Retooling something was never easier, especially if you need great detail in your replicas.
With vacuum casting, you can create your own mold using expensive procedures. The enhanced features can help you polish up the finished product. This quite useful if you are working on a small run of something that is out of print or no longer being produced by a larger manufacturer.
Creating Prototypes Using Vacuum Casting Procedures
If you are looking to build the simplest, most functional prototype, vacuum casting is the best route you can take. Most workshops are pretty familiar with the procedure and they can even combine with their latest technology in 3D printing to create a pattern of your idea.
Working with someone who manages all the stages of your project is a plus. Vacuum casting is very versatile but it’s also very delicate. It’s true that the machining capacities of most workshops can handle it without human intervention. But you need to make sure to work with someone who handles everything from the earliest stages of your CAD model until the final run is delivered.
The time it takes to make your product depends on the features you order in your products. You also need to make sure the dimensions are right. Larger products will require a lot more of work, so make sure the cast is done right. The best workshops usually have you on the call to discuss every single detail about your product. As you can guess this also affects the final budget of the products, that’s why it’s so important to plan ahead for everything.