Silicone molding is a remarkable and highly adaptable method for crafting molds suitable for an extensive range of materials, including resin, concrete, wax, and even metal. The allure of silicone molds lies in their ability to impeccably reproduce intricate details and their remarkable durability. These qualities make silicone molding an ideal choice for a multitude of applications, from prototyping and crafting jewelry to fabricating awe-inspiring special effects.
While the basics of silicone molding are fairly straightforward, there exists a realm of advanced techniques that can elevate the quality of your molds to new heights. Let’s delve into these advanced silicone molding techniques that have the potential to transform your creative process.
Mastering Degassing for Flawless Molds
Degassing is a critical step in the silicone molding process, as it involves the removal of air bubbles from the silicone rubber prior to pouring. These pesky air bubbles can lead to defects in your mold, such as voids and surface imperfections. There are various methods for degassing silicone rubber, including the use of a vacuum chamber or alternative techniques like applying heat or utilizing a centrifugal degassing machine.
The Magic of Inhibition
Inhibition is the art of preventing silicone rubber from adhering to specific surfaces. This technique is especially valuable when crafting molds of objects with intricate undercuts or complex geometries. To inhibit silicone rubber, various materials can be used, such as mold release spray, soap, or even the trusty Vaseline.
The Significance of Parting Lines
Parting lines are the seams where two or more pieces of a mold come together. When designing a silicone mold, it is important to place the parting lines strategically to minimize the amount of post-curing finishing work that needs to be done. The parting lines should be placed in areas where they will not interfere with the final product, and they should be as smooth and even as possible. If the parting lines are not placed correctly, it can be difficult to remove the finished product from the mold, and it can also create imperfections in the surface of the product.
Here are some tips for placing parting lines in a silicone mold:
- Place the parting lines in areas where they will not interfere with the final product.
- Make the parting lines as smooth and even as possible.
- Use a sharp tool to create the parting lines.
- Sand the parting lines after the mold has cured.
- Apply a release agent to the parting lines before pouring the silicone.
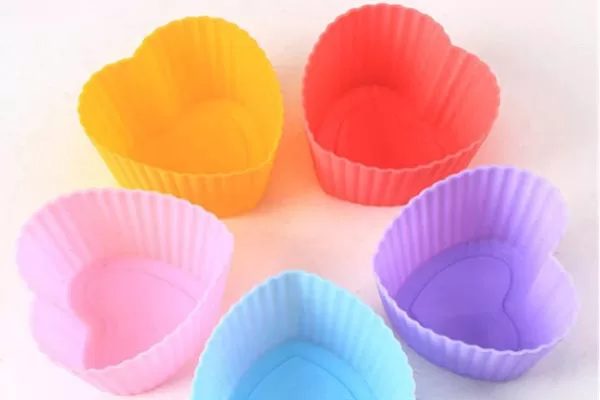
Silicone microwave cake molds
The Role of Mold Keys
Mold keys are small features that are incorporated into silicone molds to help with the alignment of different mold pieces during assembly. They are especially important when working with large and complex molds. Mold keys are typically made of a material that is harder than silicone, such as metal or plastic. They are designed to fit into corresponding slots in the other mold pieces, which helps to ensure that the pieces are aligned correctly when the mold is assembled. This can help to prevent leaks and other problems during the molding process.
Mold keys can also be used to help with the removal of the finished product from the mold. When the mold is opened, the mold keys can be used to pull the product out of the mold. This can help to prevent damage to the product.
Mold keys are an important part of the mold-making process. They can help to ensure that the mold is assembled correctly and that the finished product is removed from the mold without damage.
Reinforcing for Durability
Reinforcement can be added to silicone molds to make them more durable and less likely to deform. This is especially important for molds that will be used to cast heavy or abrasive materials. Reinforcement materials can include fiberglass cloth, metal mesh, or even other types of silicone rubber. The reinforcement is usually applied to the inside of the mold before the silicone is poured. This helps to distribute the weight of the material being cast more evenly and prevents the mold from cracking or breaking.
Embracing Multi-Part Molds
Multi-part molds are the solution for crafting molds of objects with intricate geometries or undercuts. These molds consist of two or more pieces that can be assembled and disassembled to allow for the easy removal of the cast object. This is in contrast to single-part molds, which can only be used to create objects with simple geometries. Multi-part molds are more complex to create, but they offer a number of advantages over single-part molds. They can be used to create objects with complex geometries, undercuts, and internal features. They also allow for easier removal of the cast object, which can reduce the risk of damage. Additionally, multi-part molds can be reused multiple times, which can save money in the long run.
The Science of Pressure Casting
Pressure casting is a technique that enhances the density and reduces voids in castings compared to traditional methods. This is achieved by applying pressure to the mold during the casting process, yielding superior results. Pressure casting is a more expensive process than traditional casting, but it produces castings with higher quality and greater strength. It is often used for casting complex shapes or for casting parts that must withstand high levels of stress.
The Art of Vacuum Casting
Vacuum casting is a technique that delivers castings with a refined surface finish and minimal bubbles. The key lies in evacuating air from the mold before pouring the casting material, ensuring a pristine final product. This is done by placing the mold in a vacuum chamber and then applying a vacuum. This causes the air to be sucked out of the mold, leaving a void. The casting material is then poured into the mold and fills the void. The vacuum helps to prevent air bubbles from forming in the casting material, resulting in a smooth, finished product.
Vacuum casting is a versatile technique that can be used to create a variety of castings, including jewelry, medical devices, and automotive parts. It is a precise and repeatable process, which makes it ideal for manufacturing high-quality castings.
Rotocasting: Crafting Hollow Wonders
Rotocasting is a method of casting that is used to create hollow objects. The mold is rotated while the molten material is poured into it, which causes the material to coat the inside of the mold and then drain out of the center. This method is often used to create objects with complex shapes or that need to be hollow, such as pipes, gears, and light fixtures.
Rotocasting is a relatively simple and inexpensive process, and it can be used to create a wide variety of objects. However, it is important to note that the objects created by rotocasting are not as strong as those created by other methods, such as sand casting or investment casting.
Perfecting Your Silicone Molding Process
These advanced silicone molding techniques open up a world of possibilities for creators. However, a few additional tips can further enhance your molding process:
- Opt for premium silicone rubber. Choosing high-quality silicone rubber ensures durability and top-notch castings.
- Adhere to the manufacturer’s instructions. Mixing the silicone rubber per the manufacturer’s guidelines is essential for a successful cure.
- Thoroughly degas the silicone rubber. Complete degassing eliminates air bubbles and defects in the mold.
- Pour with care. Slow and careful pouring minimizes the risk of trapping air bubbles.
- Cure in a dust-free environment. A clean environment prevents dust particles from marring your mold.
- Embrace mold release spray. Prevent unwanted adhesion by using mold release spray.
- Master multi-part molds with mold keys. In the case of multi-part molds, use mold keys to ensure a seamless assembly.
- Reinforce as necessary. For added durability and resistance to deformation, consider reinforcement.
- Consider pressure or vacuum casting. Achieve higher density and fewer voids in your castings through these advanced techniques.
With practice and dedication, you can harness the full potential of advanced silicone molding techniques, creating molds that excel in detail and precision.
In addition to these tips, it is also important to keep the following in mind:
- The type of silicone rubber you choose will affect the final properties of your mold. For example, some silicone rubbers are more durable than others, while others are more flexible.
- The thickness of the silicone rubber will also affect the final properties of your mold. A thicker mold will be more durable, but it will also be more difficult to remove the casting.
- The temperature of the silicone rubber will affect the curing time. A warmer temperature will speed up the curing process, while a cooler temperature will slow it down.
- The amount of silicone rubber you use will also affect the final properties of your mold. A larger mold will require more silicone rubber, and it will also take longer to cure.
With these tips in mind, you can create molds that are perfect for your needs.
Elevate Your Creativity with Advanced Silicone Molding
In conclusion, we have explored the tools and techniques that can transform your creative process as we conclude this journey into the realm of advanced silicone molding techniques. Silicone molding is not just a basic craft; it is a versatile and powerful art form that allows you to bring your most intricate and innovative ideas to life. The possibilities are endless, from inhibition and parting lines to pressure casting and vacuum casting.
By mastering these advanced techniques and adhering to best practices, you’ll create silicone molds that are not only functional but works of art in their own right. The precision, durability, and finesse offered by advanced silicone molding will set you apart as a master of your craft.
Whether you are a seasoned professional or just starting in silicone molding, these techniques will undoubtedly take your projects to the next level. As you delve deeper into this world of creativity, remember to always strive for continuous improvement, explore new ideas, and, most importantly, enjoy the art of silicone molding.
Ready to take your creative projects to new heights? Start your journey toward mastering advanced silicone molding techniques today. With dedication and practice, you can achieve incredible results. Unleash your creativity and turn your ideas into reality with the precision and artistry that advanced silicone molding affords.
So what are you waiting for? Dive into the world of advanced silicone molding and let your creativity run wild. Your next masterpiece is just a mold away.