In modern manufacturing, where precision and efficiency reign supreme, Computer Numerical Control (CNC) machining has become indispensable. It has revolutionized how we produce components, enabling the creation of intricate parts with unparalleled accuracy.
While traditional 3-axis CNC machining has long served as the industry standard, 5-axis machining, with its unparalleled precision, has ushered in a new era of possibilities, pushing the boundaries of what is achievable in manufacturing.
The Evolution of 5-Axis Machining
At its core, CNC machining involves using computer-controlled machines to remove material from a workpiece and transform it into a desired shape. In 3-axis machining, the cutting tool moves along three linear axes (X, Y, and Z), allowing for the creation of relatively simple geometries.
However, 5-axis machining takes this concept to the next level by incorporating two additional rotary axes (A and B). This enables the cutting tool to approach the workpiece from virtually any angle. This added flexibility unlocks a world of advantages, particularly when it comes to complex and intricate parts.
Key Advancements in 5-Axis CNC Machining
The continuous pursuit of excellence in manufacturing has driven significant advancements in 5-axis CNC machining technology. Let’s delve into some of the key breakthroughs that have propelled this field forward:
- Improved Machine Tool Design and Rigidity: Modern 5-axis machine tools are engineered with enhanced rigidity and stability, minimizing vibrations and ensuring precise tool movements even during complex machining operations.
- Enhanced Cutting Tool Technology: The development of advanced cutting tools, such as those with multiple cutting edges and specialized coatings, has further expanded the capabilities of 5-axis machining, allowing for faster material removal rates and improved surface finishes.
- Advanced Software and Simulation Capabilities: Sophisticated software tools enable seamless programming and simulation of 5-axis machining operations, reducing errors and optimizing toolpaths for maximum efficiency.
- Integration of Automation and Robotics: Incorporating automation and robotics into 5-axis machining processes has streamlined production, minimized human intervention, and increased overall productivity.
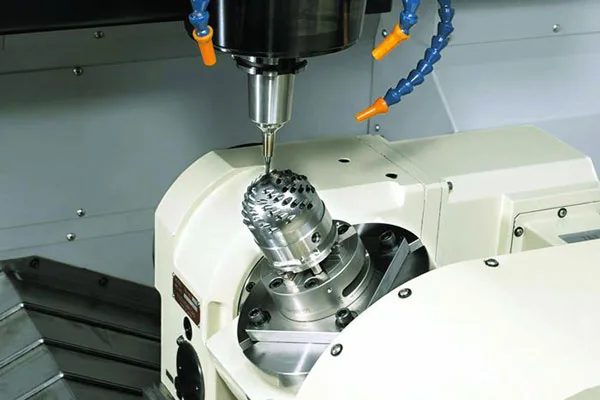
5 axis cnc machines
Applications and Benefits of 5-Axis Machining
The versatility and precision offered by 5-axis CNC machining have applications in various industries, inspiring innovative solutions and pushing the boundaries of what is possible in manufacturing. Let’s explore some notable examples:
- Aerospace: The aerospace industry demands components with complex geometries and tight tolerances. 5-axis machining excels in producing intricate parts such as turbine blades (the rotating part of a turbine that extracts energy from a fluid flow and converts it into useful work), engine components, and structural elements.
- Automotive: From engine blocks to transmission components, 5-axis machining is crucial in manufacturing critical automotive parts that require high precision and performance.
- Medical: The medical field relies on 5-axis machining to create intricate implants, prosthetics, and surgical instruments with exacting specifications.
- Mold-Making: The ability to machine complex shapes and contours makes 5-axis machining ideal for producing molds used in injection molding die casting, and other manufacturing processes.
Beyond its industry-specific applications, 5-axis machining offers several overarching benefits:
- Complex Geometries and Intricate Parts: The multi-axis capability of 5-axis machines allows for creating parts with complex curves, undercuts (features that are not accessible from the top of the part), and intricate features that would be impossible or extremely challenging to achieve with traditional 3-axis machining.
- Reduced Setup Time and Increased Productivity: 5-axis machining significantly reduces setup time and increases overall productivity by eliminating the need for multiple setups and repositioning of the workpiece.
- Improved Surface Finish and Accuracy: The ability to approach the workpiece from various angles enables 5-axis machines to achieve superior surface finishes and tighter tolerances, resulting in higher-quality parts.
- Greater Design Freedom and Flexibility: 5-axis machining empowers designers and engineers with greater freedom to explore innovative designs and complex geometries, pushing the boundaries of what is possible in manufacturing.
Future Outlook
As technology advances rapidly, the future of 5-axis CNC machining looks promising. We can anticipate further advancements in automation, with robots and cobots playing an even greater role in machine tending and material handling.
Artificial intelligence (AI) and machine learning will likely be integrated into 5-axis machining processes, enabling predictive maintenance, process optimization, and adaptive machining strategies.
Furthermore, adopting sustainable practices, such as using energy-efficient machines and eco-friendly cutting fluids, will become increasingly important in the years to come. The future of 5-axis CNC machining is bright, with exciting advancements on the horizon.
Conclusion
5-axis CNC machining represents a paradigm shift in manufacturing, enabling the creation of complex and precise parts that were once deemed unattainable. With its ability to streamline production, reduce costs, and enhance product quality, 5-axis machining is poised to shape the future of manufacturing across various industries.
As technology continues to evolve, we can expect even greater advancements in this field, unlocking new possibilities and driving innovation in the years to come.