Plastic injection molding and Liquid Silicone Rubber (LSR) are two amazing technologies. This dynamic duo is responsible for a whole new wave of products entering the market in recent decades.
One of the most successful inventions is the silicone cup. Whether it’s a standard coffee mug or a collapsible camping mug, silicone molding makes any cup design possible.
But how do manufacturers produce them in so many different colors? What’s the secret?
What Is a Silicone Cup?
A silicon cup features a design and construction with food-safe silicon that’s non-toxic and safe to use. This synthetic rubber is suitable for a wide variety of molding applications and is known for its durability, flexibility, and heat resistance. From medical devices to kitchen utensils, injection molding offers so much potential for manufacturing and design innovation.
Silicone Cup Manufacturing Processes
The versatility and safety of silicon cups make them high-demand products. Understanding how manufacturers produce silicon cups can assist you with making an informed decision on the right manufacturing partner for your production project.
There are several manufacturing methods used in silicon cup production.
- Liquid silicone rubber (LSR) injection molding
- High-consistency rubber (HCR) molding
- Compression molding
- Transfer molding
- Extrusion
Each method has pros and cons, but injection molding is the most common and popular choice for manufacturing projects. You get excellent accommodation for design complexity, high production volume, and color variation.
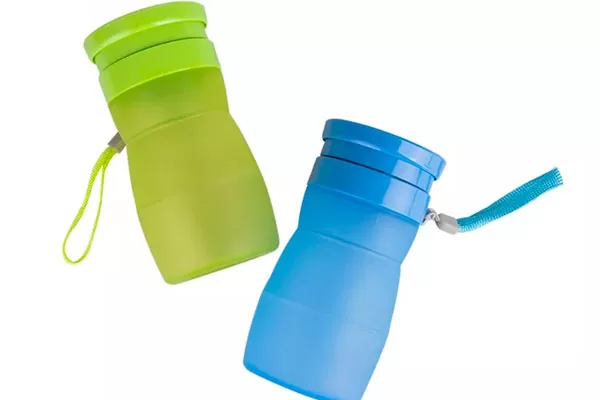
Silicone cups
LSR Liquid Silicone Rubber Injection Molding for Silicon Cups
LSR molding is the most popular production method for manufacturing silicone products, like cups. You get plenty of variation, allowing you to design any cup, even those with fine details and complex shapes. LSR involves injecting liquid silicone rubber into a pressurized, heated mold.
After the rubber solidifies and cures, it takes the shape of the mold, resulting in the finished product. The manufacturer benefits from repeated quality and high-precision manufacturing processes, making it the best choice for mass-production projects like silicon cups.
Some of the pros of using LSR injection molding are the following.
- Consistency and precision.
- Fast cycle time offers scaled production rates.
- Minimal material waste.
- Ideal for complex patterns and designs.
The ability of mass production through LSR molding processes makes it attractive to companies. Another great advantage of LSR is its ability to accommodate the manufacturing of different colored parts.
How Do Manufacturers Color Plastics & Silicone?
Manufacturers can produce silicon cups in dozens of colors to suit anyone’s taste. But how do they do that? The injection molding process allows for different color batches in production runs, allowing for a variety of final colors for any product.
Here are some methods manufacturers use when coloring their materials for silicon cup production runs.
- Masturbating – The manufacturer premixes colors with material resin but doesn’t fit into the molded plastic parts. This process requires uncolored rubber or plastic to scale it down to 2% of the material volume before use.
- Compounding – The manufacturer premixes resin with several color options before placing the mixture into the molding materials.
- Dry Pigment Mixing – The manufacturer mixes dry pigment powder into the pellets in the injection molding machine in a 2% material/color ratio.
- Solvent Coloring – Involves spraying uncolored material pellets with a solvent featuring infusion with the required pigment at a 2% ratio.
Conclusion
Silicon cups are a safe, durable, affordable container option for consumers. It offers less environmental impact than other production methods and is an alternative to traditional materials like ceramic and glass.
By learning the manufacturing processes, design considerations, and quality control measures involved in silicon cup manufacturing, consumers and companies can make informed decisions on choosing the right manufacturing partner for their production requirements.