Vacuum casting is one of the rapid prototyping techniques manufacturers used to create prototypes to test and evaluate a product design. What this manufacturing method offers is its versatility. Vacuum casting is one of the most versatile of all the prototyping processes because it offers a wide range of properties in its produced parts and to the applications where these parts will be used.
We can find different kinds of vacuum-casted products around us, from food to cosmetics, to electronic products. It only shows how beneficial vacuum casting is to businesses across different industries.
In this article, we will enumerate these benefits and why you should consider using vacuum casting for your business.
Benefits of Vacuum Casting
The properties of the resulting prototype parts from vacuum casting closely resembles that of final products. That makes it ideal for testing and presentation purposes, as well as small production runs of production parts.
Low-Volume Manufacturing
Vacuum casting is the perfect option when you need quality plastic components in a small volume. With vacuum molding, you can make a prototype and produce high-quality plastics parts. Because there is less tooling needed in the process, it can help manufacturers save costs.
This manufacturing technique is best for research and development because it is inexpensive and has a quick turnaround time. It is ideal for various applications like consumer products, construction, display, automotive, and packaging.
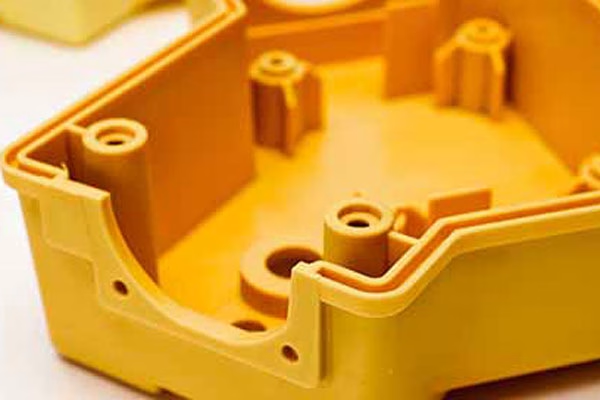
Vacuum casting molds
Precision
Another benefit that you can get from vacuum casting is precision. It shows high-fidelity to the design as they are more precise and a perfect fit. If you are going to make a plastic case for your smartphone, you should not only choose the best design for the unit, but it should also fit well. The vacuum casting process lessens the error during the production stage and eradicates the chances of rejection of your finished product. This is highly beneficial to small businesses because you can cut down on costs and rejects.
Cost-Effective
There is minimal tooling required in vacuum casting. As such, you don’t need to invest a lot. The process does not also require high pressure. Thus, it does not require any high-quality or sophisticated tools. Furthermore, they can also benefit from the low cost of material needed for creating molds, and the scraps from the finished products are 100% recyclable.
Range of Finishes
Since the vacuum-casted products have smooth finishes, there is no need for further processes. At the same time, you can also create products with different surface textures because it can copy the finishes of the master model.
Multiple Uses
Vacuum casting can produce different prototypes ideal for assembly-testing, research and development, functional parts testing, design improvements, and marketing purposes.
Conclusion
Vacuum casting is an effective prototyping method that can benefit small to medium businesses. It is an effective method for rapid prototyping because the resulting product can closely resemble the master model. It is typically used for short batch runs of prototypes for testing and evaluation.