Otherwise known in the industry as polyurethane or urethane casting, the vacuum casting process for prototyping utilizes silicone molds to manufacture rubber and plastic components under a vacuum. This rapid prototyping and manufacturing process is highly adaptable to production and used in complex part design with materials like cast nylon or polyurethane resin.
The vacuum created during production produces a bubble-free, high-quality casting featuring a smooth surface without blemishes. The result is a solid component, ideal for projects requiring stringent quality controls.
Common Vacuum Casting Applications
Vacuum casting is popular in several industries. Manufacturers can implement this process in mold tooling production for the following sectors.
- Packaging in the food and beverage industry
- Cases for mobile phones and sunglasses cases
- Household products
- Automotive parts
- Fixtures and fittings
What Materials are Suitable for use in Vacuum Casting Projects?
Vacuum Casting is used in prototyping or mass production, with similar results to 3D printing. Typically, vacuum casting projects use polyurethane-based resins to emulate material textures. Vacuum molds feature construction with silicon material using a 3D printer.
Rubber is highly tear-resistant and flexible, making it ideal for manufacturing components like gaskets or seals. Polycarbonates are suitable for producing shock-resistant components. A manufacturing partner can recommend the right materials for your project.
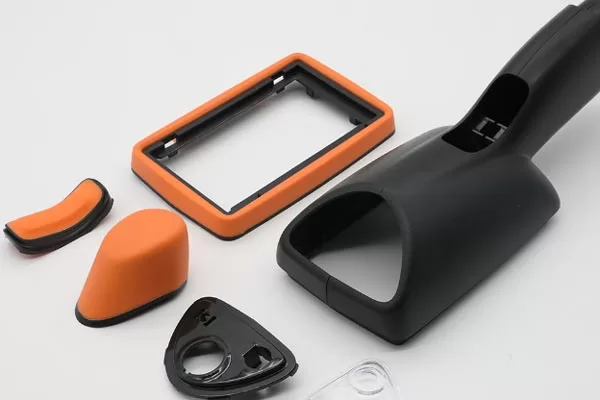
Vacuum casting products
Basic Design Guidelines for Managing Vacuum Casting Projects
Vacuum casting offers manufacturers a cost-effective production process, provided they optimize manufacturing procedures around this technology. Setting up an efficient production run requires following a set of best practices to ensure product quality, consistency, and cost efficiency.
Here are a few examples of production guidelines used in vacuum casting applications.
Select the Correct Draft Angle
The draft angle refers to the taper on the mold’s sidewalls. Manufacturers must strive to include the highest design angle to improve components extraction from the tool. As a general guideline, you require a greater taper angle for rough or deep surface textures.
The draft angle plays a critical role in maintaining the cost of vacuum-casted parts in production runs. Ensuring you have the right draft angle deters issues with de-molding, resulting in expensive repairs that add to production costs.
Ensure the Even Distribution of Material Along Radii
Manufacturers can cut project and production costs by using larger radii when creating corners to ensure better material distribution. Typically, you’ll find the most important radius at the bottom of your draw.
Set the Ideal Draw Ratio
The draw ratio defines the relationship between the length and depth of the casted components’ shape. The taller or deeper the molded portion, the greater the thickness required in the material sheet when starting the project. For the best finish, ensure you don’t use deep or tall elements too similar to each other.
Watch the Undercut Depth
These project characteristics can prevent you from extracting the component from the tooling. So, keep any undercuts under 15mm in depth. Remember the draw ratio when designing undercuts into products to ensure the production process runs smoothly.
Include Points of Reference
All production components should feature reference points, allowing production partners to compare results between controlled surfaces or points. Examples include drilled hole centers and cut-outs.
Attach Ribs & Bosses
Manufacturing partners must include ribs to support flat surfaces. They’re manufactured separately before being glued to the original components. The same applies to internal bosses. They’re independently machined and added. This process also adds to project costs in prototyping and production processes.
Surface Textures
Different projects require different textures depending on the functionality or final appearance of components. Manufacturers can change surface textures by using raw materials with pre-formed surfaces or by texturing the tooling’s surface. These textures require greater draft angles in tooling setup, leading to an increase in production costs.
Machining of Holes, Cut-Outs, & Vents
Manufacturers calculate trimming measurements by referencing the component’s molded side. Surplus materials are machined for a high-quality finish for design features like holes, cut-outs, trim, and vents.
Understanding Tolerances & Costs
The tighter the tolerances in production components, the higher the costs and longer lead time for the project. Keeping to looser tolerances mitigates these factors, allowing for faster prototype production. When using machined aluminum molds, use tolerances of 0.25mm on the first 25mm of the mold. Tighten things up by 0.25mm for each concurrent 250mm section moving forward.
In Closing – What are the Advantages of Vacuum Casting?
Vacuum casting offers several benefits to rapid prototyping projects.
- High-quality results for rapid prototyping processes.
- High accuracy and precision of casted parts.
- Exceptional detail in finished components.
- Reduced costs for mold tooling.
- Reduced production time for mold tooling.
- Wide range of polyurethane resins available for mold casting.
- Create high-quality surface textures in component manufacturing.
- Vacuum casted molds are highly durable and suitable for 20+ copies.
- Acts as a bridge to mass production.
- Reduces project production costs.
Ensure you choose a production partner skilled in vacuum casting processes to eliminate manufacturing bottlenecks and extensions to lead times.