Silicone products were first introduced into the medical industry in the 1950s. Over the last 70 years, more medical device manufacturing companies have turned to liquid silicone rubber (LSR) for product development and production.
LSR is popular with medical manufacturing due to its properties of biocompatibility with human fluids and tissues, its hypoallergenic nature, and its excellent performance across a range of applications. Its mold, bacteria, and chemical-resistant properties make it highly adaptable to demanding medical environments.
LSR is crack and scratch-resistant, and it doesn’t discolor. The material also allows the incorporation of glass, plastics, and composite materials into the design. The result is a reduction in manufacturing times and costs.
Medical and food-grade LSR materials have excellent stress resistance and tear strength, making them ideal for demanding applications like gaskets and seals. LSR goes beyond medical applications, and it’s a common material used in rapid prototyping and mass manufacturing projects across many industries.
The Advantages of Liquid Silicone Rubber Molding
Excellent Compression Characteristics
LSR has innate compressibility characteristics. This property of the material allows for the design of components that are otherwise unsuitable for plastic construction. LSR is easy to combine with other materials without priming.
No By-Product Generation
LSR doesn’t create by-products from production processes. The material’s molecular structure is ideal for a range of applications. The excellent bonding strength between oxygen and silicon atoms in the material prevents the polymers from degrading under high temperatures.
More Design Flexibility
Typically, LSR features design guidelines comparable to the use of thermoplastics. However, it offers more design freedom in specific areas. LSR offers product designers greater flexibility in projects because it has more forgiving properties than thermoplastics.
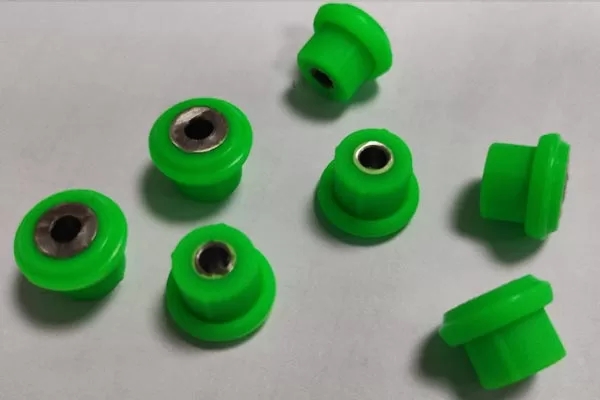
Silicone parts
Sink
LSR doesn’t have any issues with sink. The heat of the production process is enough to cure the materials. Since sink isn’t a problem, designers can use LSR for component manufacturing where certain features are thicker than the use of thermoplastics permits.
Planes
Planes running in the same direction as the mold typically require some draft to allow milling of the injection mold. When designing the mold, it’s important to leave one degree per inch of depth in the mold to stop scraping against the mold.
Undercuts
Undercuts in manufacturing processes present the most significant difference between LSR and other injection-molded materials. Manufacturers can shape and mold thermoplastics with undercuts. However, it requires a complicated manufacturing process. LSR production processes allow for complex methods like pick-outs and the use of actions to create the undercut and remove it from the mold.
In Closing – Why Use LSR in Your Rapid Prototyping or Mass Production Project?
Over the last decade, silicone manufacturers have made tremendous progress in creating new LSR formulations and manipulating the material’s properties. These advancements saw improvements in LSR performance, pricing, and processing stability.
These breakthroughs in LSR technology leveled the playing field for manufacturing. LSR also replaced many thermoplastics in various manufacturing processes. Here are a few of the industries that rely on LSR technology in product design and manufacturing.
- Healthcare and medical – endoscopy tubing, medical tubing, face masks, catheters.
- Automotive – O-rings, gaskets, seals, and LED lenses.
- Optics – Professional exterior lighting arrangements.
- Electronics – Protective sleeves, LED lenses, and lighting guides.
- Consumer goods – goggles, nose pads, ear buds, and headsets.
Individuals and companies must ensure they spend enough time researching and evaluating LSR material properties when choosing the right material for their rapid prototyping or mass manufacturing projects.
Selecting the right material is crucial in industries like healthcare, where safety and toxicity are a concern. To choose the right material for the task, designers must have clearly defined performance standards relating to material properties such as thermal resistance, durometer resistance, and elongation resistance.
Selecting the incorrect material for the prototype or project can cause problems with the prototyping phase and increase costs. LSR is usually more costly than other materials for prototyping and mass-manufacturing projects.
However, manufacturing with LSR offers several advantages unavailable with other polymers. It’s an especially beneficial material to use in high-volume manufacturing tasks. Its properties as a raw material make LSR the preferred choice for many manufacturing projects despite its higher cost compared to thermoplastics.
Its ability to suit automated production processes and the reduction of labor associated with manufacturing offsets the additional material costs. A single operator can monitor the entire production process, reducing the labor required for the project and saving on costs. One operator can attend to several injection molding machines in operation.
This cost-savings characteristic of LSR means that manufacturers see benefits from increases in the efficiency of the manufacturing process and a drop in labor costs. It’s the ideal production material for low and high-volume production projects.
LSR offers manufacturers cost-efficiency and consistency for various applications in many industries, such as designing and producing medical, automotive, infant care, consumer products, and electronics.