Rapid prototyping requires fast production of parts to assess the viability of offering them to the market. After prototyping, fast distribution relies on fast production strategies designed to deliver results.
Single and multi-cavity injection molding offers the best of both worlds to manufacturing. It’s not about comparing these production methods against each other in just a performance sense. We need to understand the differences between them to get an accurate understanding of their role in production.
The Differences Between Single & Multi-Cavity Molds
Injection molding is relatively new to production and got its start at the turn of the century. It’s been a long road since those times. The introduction of computerized systems, improved supply chains, and access to more resources led to rapid economic expansion. Improved technology became a big driver in the rapid adoption and spread of injection molding in commercial manufacturing processes.
Today, injection molding makes a huge variety of products, from aerospace parts to toothbrushes. Its versatility made it easy to replicate effects fast, with volumes in the millions. How many parts per cycle isn’t always the reason to use injection molding in the production phase alone. While it’s ideal for high-volume production, it’s not so great for prototyping.
That’s where single-cavity molds come in. Single cavity molds are great for manufacturing custom components for prototypes without dedicating themselves to production immediately.
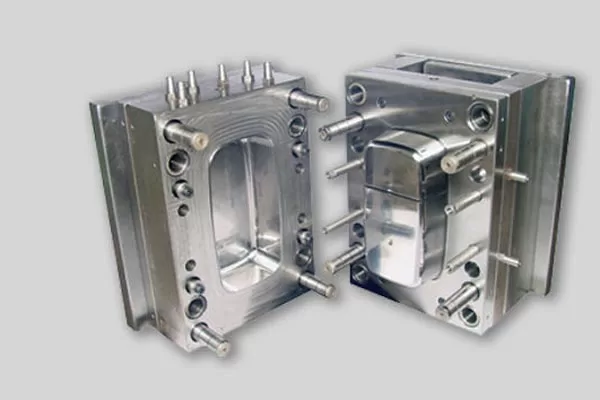
Single cavity injection mold
What are the Pros of Single-Cavity Molds?
- Single-cavity molds are ideal for the following project and production scenarios.
- Manufacturers single components for prototyping.
- Ideal for low-volume prototyping projects.
- Single molds are more affordable to manufacture due to smaller tool sizes.
- Easy design and manufacturing.
- Suitable for daily quality control strategies.
- Short timeframes for development and production.
- Seamless move from prototype to production.
What are the Pros of Multi-Cavity Molds?
When you have the product demand to enter a high-volume production, a multi-cavity mold comes into the picture. When you need millions of replications and the highest cycle time, look at multi-cavity molds. Here are some of the advantages of using this production technology.
- Shorter lead time per batch from order date.
- High-volume production capacity (parts per cycle).
- The high success rate in production with fewer failures.
- Minimal product waste.
- Lower production costs through economies of scale.
- Suitable for molding multiple unique parts for a single assembly or identical parts per cycle.
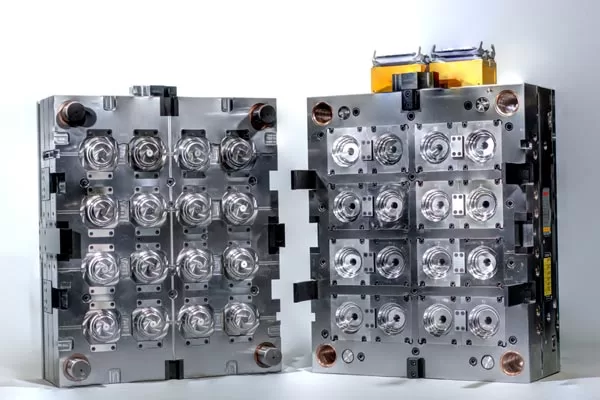
Multi cavity injection molds
Are There Drawbacks to Multi-Cavity Molding?
While multi-cavity molding is certainly a miracle tech for mass production purposes, in prototyping, it has some disadvantages.
The multi-cavity design and manufacturing process takes more time to create, tool and set up. So, you have a longer lead time for the mold.
The cavities in the mold require a lengthy quality inspection to make them suitable for mass production.
Damage to one part of the mold may result in the need for retooling the entire mold. (You can ask the manufacturer to make the mold cavities modular for easy replacement and to lower costs.
Multi-cavity molds require a larger tooling investment than single-cavity molds.
In Closing – Examine Market Conditions and Consumer Demand
Manufacturers should consider their production requirements before executing their mold design and system. What is your demand forecast for your product and market? What production requirements do you need to make the project work? What growth potential is there for the product?
Is your market and demand volume susceptible to exterior forces beyond your control? Government export or import tariffs, supply chain issues, logistical changes? What kind of quality do you expect from the production process? These questions make a huge impact on your needs.
Your market data and forecasting may dictate which is the better strategy. But choosing without a discussion with production specialists is detrimental to the company long-term.