Metal injection molding (MIM) is a rapid prototyping and production process suited to high-volume production applications with intricate components or complex shapes. It’s one of the most frequently used manufacturing processes in modern prototyping and mass production.
The high-efficiency and cost-effective properties of MIM make it a highly popular process. MIM has limitations, with molds holding up to 100 grams of material per “shot.” However, every shot can apply to several cavities.
This feature allows the simultaneous manufacturing of many small components, cutting production costs. Feedstocks used in the MIM process consist of a variety of metals, the most common of which is stainless steel.
After molding, the manufacturer removes the binding, and the metal components undergo refinement to optimize the durability and strength of the molded materials. As a result of this manufacturing process, the item may shrink up to 15% after cooling.
This post unpacks everything you need to know about MIM and how it suits prototyping and manufacturing applications.
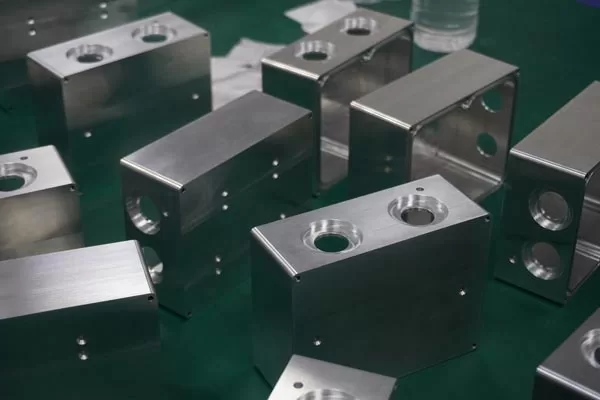
Metal injection molding parts
Is The Metal Injection Molding Process Complicated?
MIM was popularized as a prototyping and manufacturing process in the mid-1950s. The 1990s led to many innovations in the MIM industry, refining the process for optimal use in prototyping and mass-production projects.
The MIM process involves the following steps.
Step 1 – Preparing Feedstock
The MIM process incorporates materials such as metallic powders and thermoplastic binders. The binder provides an intermediary aid during production, and manufacturers must remove it after injection molding.
The properties of the powders determine the features and properties of the molded components in terms of their strength, corrosion resistance, and other physical characteristics. The manufacturer blends the metal powders and works in a plasticized binder material at elevated temperatures using a shear roll extruder or kneader.
The resulting intermediate material is known as the “feedstock.” Typically, this material is coarse, featuring granule sizes in millimeters to satisfy plastic injection molding requirements. Manufacturers have the option of buying prepared feedstock that’s ready to mold. This material is readily available from international suppliers.
If a MIM manufacturing partner has the required skills, they can make the feedstock in-house using raw materials. This approach saves on costs, but not all manufacturers have the skills to pull it off successfully.
Step 2 – Injection Molding
The injection molding process forms the initial “green parts” in the same manner as forming plastic components. The variety of component geometries produced by this process stage is similar to the variety of plastic parts available through conventional injection molding.
Step 3 – Removing Binder
After completing the injection molding stage of the process, the manufacturer must remove the binder material. This approach serves to create parts with interconnected pore networks without damaging their shape.
After removing the binder, manufacturers will find some binder remaining in molded components holding the metallic particles together. However, the pore network permits evaporation of the remaining binder in the first stages of sintering when the sintering necks begin to expand between metallic particles.
Step 4 – Sintering
The final sintering stage of the process eliminates the majority of pore volume previously occupied by the binder material. As a result, MIM-manufactured components experience a degree of shrinkage during the sintering process. Depending on the material, the parts might shrink by 15% to 20%.
The sintered MIM parts may require further processing by traditional metalworking practices such as surface or heat treatments in the same manner as wrought or cast components. In specific applications, such as the aerospace, automotive, and medical sectors, manufacturers implement “Hot Isostatic Pressing” (HIP) to remove residual porosity from the material.
MIM parts are typically small components, making it a cost-effective manufacturing process for prototyping projects.
The Advantages of Metal Injection Molding
MIM offers manufacturers several benefits and advantages compared to other rapid prototyping processes like CNC machining. It’s highly efficient, and the technology makes it easy to produce complex metallic components that would otherwise be impossible to create with other prototyping and fabrication processes.
The properties of MIM components are similar to wrought alloys, allowing the manufacturing of a variety of shapes and features with minimal material waste.
MIM offers a cost-effective prototyping and manufacturing process when producing small parts in high-volume production environments. It reduces the time spent in manufacturing, resulting in a fast turnaround of prototypes and mass-manufactured parts.
Both production and finishing times are short, making it one of the most popular manufacturing methods. Some products manufactured using MIM processes include the following.
- Watch casings.
- Laptop hinges.
- Cell phone plugs.
MIM is suitable for producing prototypes and mass-producing parts in several industries, including aerospace, dental/medical, firearms, commercial, automotive, and industrial applications. It’s common to find MIM as the go-to choice for manufacturing metallic components due to the speed and ease of the manufacturing process and the high-quality results the method provides.
Considerations for Metal Injection Molding
MIM prototyping and manufacturing processes are ideal for a range of applications. One of the more common considerations with MIM is the wall thickness of the finished prototype or mass-produced component.
Products with thin walls of less than 100 micrometers are ideal for manufacturing with metal injection molding. MIM is also worth considering for companies looking to improve their environmental impact and reduce their impact on local resources.
Older generations of injection molding technology are inefficient and generate emissions. Toxic chemicals, like formaldehyde, are commonly a side-effect of traditional prototyping and mass-production processes.
The next-generation MIM machines rely on updated technology and run cleaner, producing less waste than production methods like CNC machining. We can expect MIM processes to become more efficient and greener as we move forward into the next era of manufacturing technology.
Wrapping Up – Choose a Reputable MIM Firm
Choosing the right MIM partner for your prototyping and mass manufacturing projects is crucial. Look for a production partner offering access to the latest MIM technology and skilled operators who understand the nuances of MIM processes.
While MIM is a widespread manufacturing technique, you’ll experience different results between firms, depending on their knowledge and skills of MIM processes. Choose a partner with a solid track record of producing MIM components with high-quality results.