Rapid prototyping is a method of producing low to medium quantity volumes of product using a tooling mold and the injection molding process, with the mold being made of multiple materials, such as silicone, aluminium and P20 steel. Once the mold has been produced, it can then be filled with various plastics materials to create the molded product as many times as is required. NICE Rapid is a rapid tooling and prototyping specialist, who has been at the forefront of development in the field for many years.
Skillfully ensuring that the tool is designed in the most efficient manner, as well as allowing the injected plastics material to flow into the mold at its optimum rate, is the job of the production engineer. They oversee the whole job and ensure compatibility with company, customer and international standards. Some of the benefits of manufacturing in China are reduced costs compared to similar production processes in Europe or the U.S., as well as a well-developed logistics network and skilled, qualified staff. All of the above will ensure that your product is produced exactly as you have requested, at the most cost effective price and within an efficient time scale.
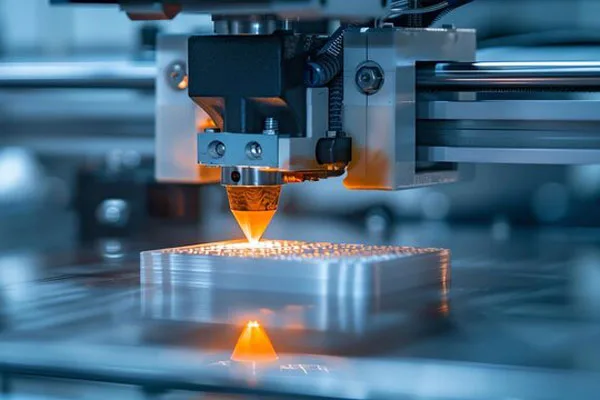
3D printing mahcines
Initially, designs are sent to us by the customer in CAD file format. On receiving this file, a process engineer reviews the information and ensures that all of the parameters specified by the customer are actually possible to manufacture. As well as this, the engineer also provides helpful suggestions on improving the design, for example by altering the flow of injected plastic into the mold so as to reduce the appearance of ‘flow lines’ in the finished produced and ensuring ‘sink’ does not occur around unsupported structures. Such attention to detail allows the finished product to be produced quickly and to the exact requirements of the customer and, most importantly, to do the job that it is designed to do, safely and effectively.
Rapid tooling is a lot quicker as a method of production than the standard tooling process. This is due to the efficient manner in which the initial CAD design is processed, as well as the smaller production volumes generally produced in a rapid tooling environment. Generally, first samples are produced within around 15 days from receiving the CAD file and this can even be faster, depending on the workload of the company. Efficiencies in designing the tool itself can also lead to larger production runs using the same tool, therefore, reducing costs and providing even further efficiencies of scale.