Molded plastics are utilized in various commercial and industrial applications. However, molding processes influence the efficiency and quality of rapid prototyping projects. In broad terms, injection molding produces parts featuring construction with molten thermoplastic resin shaped in a mold and then hardened.
The elevated pressures in the molding process cause the plastics to take the mold’s shape, creating the final molded component. As in die casting of metals, customized plastic injection molding for rapid prototyping typically makes parts requiring no additional finishing work. They’re ready for immediate assembly.
Reaction injection molding (RIM) describes a subset of specialized injection molding techniques utilizing a chemical bond between plastics, forming a polymer blend before being injected at temperature and pressure into the mold.
Manufacturers implementing RIM prototyping techniques must examine specific attributes of the technology that set it apart from others used in standard injection molding techniques. One of the core differences between them is in the nature of plastic polymerization.
This process can yield characteristics distinct from the base materials. RIM can fabricate complex shapes and large parts, making it ideal for use in industrial applications requiring the production of bulky prototype parts.
Similarly, issues with production cycle rates, cost-efficiency, and mold design influence a decision to use this prototyping technique.
Plastics Used in RIM Process
RIM is capable of prototyping parts in several plastics and polymers, including polymides, polyurethanes, and composites. These RIM materials have varying characteristics that depend on the ratio between base substances and additives used in polymerization.
Different ratios yield changes in elastomeric qualities. These outcomes will determine the prototyped parts’ ability to stretch under low-stress situations before returning to their original shape. This range of flexibility and degree of resilience affects the flexibility of composite, solid, and structural foams, which are the primary materials used in polyurethane prototype fabrication.
Since this process involves the use of molten plastic, we can consider RIM as a category of liquid injection molding. One of the liquids used in the process is infused with short fiber resin or carbon fillers, increasing the prototype parts’ stress-to-strain ratio while lowering the degree of expansion and contraction under changes to thermal conditions.
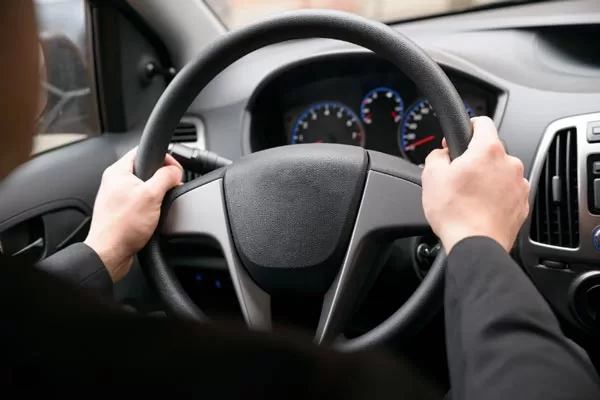
Steering wheels
Unpacking the Reaction Injection Molding Process
RIM involves a multi-phase process with different procedures from standard injection molding practices. To start, two or more types of plastic, such as a resin compound polyisocyanate, are usually poured into individual reactant tanks featuring feed-control mechanisms and temperature-control systems.
The liquids are released into the supply lines, channeling into the metering chamber, which regulates pressure levels and circulates the plastic in the mixing head.
The mixing head pressurizes the mold to between 1,500 and 3,000 psi. As the pressure rises, it uses the resulting impingement to blend plastics. After mixing the reactants, the system injects them into the mold under high pressure and at tremendous speed.
When the mold is full, the mixing head stops releasing reactants. The exothermic chemical reaction created inside the mold results in the effect of plastic polymerization.
After the polymer cures or solidifies, it’s ejected in the shape of the finished prototype component. RIM technology achieves this result with low temperatures, making it compatible with many resins and polymers.
Apart from the heat required to melt the plastic pellets, injection molding techniques are relatively low-heat. Rather than rely on reactions from thermal energy, RIM creates chemical energy through polymerization reactions.
The molds in RIM processes feature design and construction with stainless steel, nickel, or aluminum. The operator clamps the mold closed in a low-weight press during the start of the production process.
The curing time for polymers is usually under a minute, allowing for rapid turnover and the ability to function in mid-volume and mass-production environments.
Industrial RIM Applications
Due to the low processing and injection temperatures and pressures involved with the process, RIM is ideal in production scenarios for molding large parts with smooth finishes and variable wall thicknesses.
Manufacturers can benefit from high turnover rates, making it an effective rapid prototyping solution for low to mid-volume projects. Rim components also feature improved tensile strength, solvent resistance, and temperature resistance.
However, under prolonged exposure to UV rays in sunlight, polymer-based parts will degrade, and machining or tooling costs are high for producing polymer products.
Automotive manufacturers are an example of using RIM in mid-volume manufacturing processes. RIM is used in the production of side panels, steering wheels, gauges, armrests, dashboard consoles, bumpers, and body frames.
Some RIM components have elastomeric properties, making them ideal for use in household appliance manufacturing. You’ll find this process used in the production of recreational supplies and heating and cooling units.
RMI offers the chance for consolidation of parts, enabling the streamlining of fabrication processes while eliminating the need for additional tooling. Some manufacturers utilize this advantage of RMI technology to craft in-metal components, such as hinges and frames.
However, it’s important to note RMI isn’t the ideal solution for mass production at high volumes. It’s not the right process for smaller, mass-produced components. Building the molds is expensive, and they have little longevity under high-volume production runs.
Additionally, small errors with pressure calibration in the mixing head can lead to wide variances in the volume of material injected, leading to cracking after curing.
Understanding if RIM is Right for Your Project
Considering the complex design capabilities, impressive strength-to-weight ratio, and smooth finish produced by RIM components, the process is mostly reserved for large component prototype manufacturing, not smaller parts.
Reaction injection molding is effective and efficient in appliance assembly or reduced-volume vehicles. However, prototyping projects with high volumes of small parts are better serviced by other prototyping processes.
What Is Reaction Injection Molding – Key Takeaways
- Reaction Injection Molding is cost-effective for parts measuring >0.5 m2.
- RIM is low-cost tooling that suits different volume and size requirements.
- Small runs for prototyping projects and flexible ordering to match build rates.
- Customization with several finishes and colors.
- Parts conform to UL94 V0 standards and compliance ratings.
Choose a partner in RIM rapid prototyping with a good track record and a focus on customer service. Your production partner should recommend a RIM process where applicable to your project.