CNC machining is a rapid prototyping and production process using algorithmically controlled machines to remove material from workpieces. CNC machining is compatible with a wide range of industrial materials, including metals, composites, and plastics.
CNC machining allows the formation of complex shapes not available in other conventional machining processes. It allows for efficient, fast manufacturing suitable for mass production or rapid prototyping projects.
Manufacturers have options to use 3, 4, or 5-axis CNC machines for their projects. This article discusses the difference between 4-axis and 5-axis CNC machines.
The Benefits of 4 and 5-Axis CNC Machining
There are several benefits to using 4-axis and 5-axis CNC machining. Consider the following when selecting the CNC process for your prototyping project.
- 4 and 5-axis CNC machines can produce complex forms impossible to manufacture using conventional production methods.
- 4-axis CNC machines can work on several sides of workpieces in a single operation, making them ideal for mass-production projects.
- 5-axis CNC machines are ideal for cutting intricate designs into workpieces.
- Choose the right CNC process to suit the material you’re working with.
Typically, CNC machining, especially with 4-axis and 5-axis machines, can be costly compared to other manufacturing methods.
Using CNC machines adds costs to the project due to the expense of setting up the machine. The setup cost is the same if you’re producing a single component for prototyping projects or thousands of parts in mass manufacturing.
The increased precision and accuracy of 4-axis and 5-axis machining might justify the setup expense in prototyping projects.
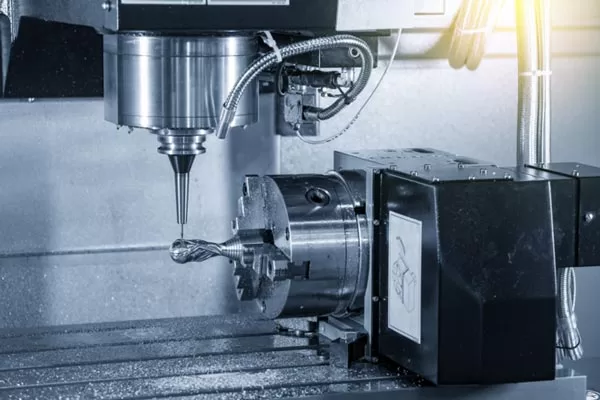
4 axis cnc machine
Understanding 4-Axis CNC Machining
4-axis CNC machining relies on four axes of motion when cutting workpieces. The 4th CNC axis lies perpendicular to the X, Y, and Z axes, allowing the CNC tool to move around the workpiece. 4-Axis CNC machining is ideal for manufacturing complex pieces since it can work on several sides of the material in a single operation.
- 4-axis CNC machines are good choices for achieving the following project objectives.
- Create Complex Shapes – Cutting intricate designs into workpieces without adjusting cutting tools.
- Machine Multiple Sides – The 4-axis CNC machine allows the cutting of several surfaces in a single operation. This makes it an ideal solution for mass-production applications.
Understanding 5-Axis CNC Machining
While 4-axis CNC machines can handle many prototyping projects, they have some limitations, especially in advanced design manufacturing involving intricate design components. In this case, we use the 5-axis CNC machine.
These CNC devices are so advanced the Department of Defense classified them as proprietary technology unsuitable for export. The tech was considered a national security issue due to the advantage it brings to the manufacturing process.
Adding a 5th axis to CNC machines gives manufacturers more freedom in machining tasks. There are two versions of CNC machines. One type features a swivel head, and the other has a rotary table.
5-axis CNC machines utilizing rotary tables feature a 5th axis built into the workpiece table. The 5-axis CNC relies on the swivel head feature of the 5th axis built into the spindle.
- A 5-axis CNC machine is ideal for projects requiring the following production advantages.
- The machining of intricate forms and features into workpieces that’s impossible to achieve with standard 3-axis CNC devices.
- Cutting multi-sided workpieces such as pyramids and cubes.
- Machining irregular workpiece surfaces.
- Cutting intricate shapes and forms into workpieces.
There is a drawback to adding a 5th axis to CNC machines. The most notable disadvantage of 5-axis CNC machines is the added expense of these machines compared to 3 and 4-axis devices. It also requires more involvement in setup, driving up project costs for companies.
However, the additional manufacturing capacity offered by 5-axis CNC machines often outweighs the additional cost of using this method. For instance, 5-axis machining is typically used in advanced technology projects in the aerospace sector where innovation outweighs prototyping costs.
Final Considerations for CNC Project Planning
Utilizing 4-axis and 5-axis CNC machines requires careful consideration of how your prototyping project can benefit from implementing this technology in manufacturing processes.
Some of the issues to keep in mind when selecting the right CNC process for your prototyping project include the following.
Determine if your project will benefit from the tech. Does your prototype have intricate design features?
- Ensure your CNC option can accommodate the size of your prototype.
- What materials will you require for the project? For instance, you’ll need different cutting tools than machining plastics if you’re using metals.
- Factor setup costs into your budget and assess if it’s financially feasible to implement this process into your project’s financial plan.
Wrapping Up
5-axis and 4-axis CNC machines offer precise, versatile manufacturing of complex components for advanced technology projects. Learning about the differences between these CNC devices allows you to select the right option for your prototyping project. Speak to a manufacturing partner about the right choice for your prototype and the costs involved with bringing your project to fruition.