Vacuum-assisted pouring of liquid materials into silicone molds to create complicated shapes is known as vacuum casting. Latex and rubber elastomers are used in vacuum sealing of a fluid. Vacuum casting is also known aspolyurethanecasting due to the fact that polyurethane resin is an elastomer utilized as a molding agent. Vacuum casting is a less expensive option for producing plastic parts than injection molding because of its lower manufacturing costs.
A great manufacturing technique for mass production and other small-scale activities is also referred to vacuum casting. Electronic components, consumer items, and bulk goods are all produced in vacuum casting. Injection molding, which creates products by pouring molten material into a mold, is extremely similar to itshole formation. Injection molding and vacuum casting are distinguished by the type of material used. Injection molding uses metals such as steel, aluminum, and others, as opposed to vacuum casting, which uses silicone molds. This lowers production costs because silicone is a cost-effective, durable material.
The most popular adhesive with this method is polyurethane. Excellent structural capabilities, ductility, impact resistance, heat resistance, and other characteristics are just a few of the benefits that polyurethanes have to offer. As a result, different polyurethanes may be used depending on the sort of product to be produced.
Vacuum Casting Processes and How exactly does it work?
Vacuum casting includes procedures that result in the production of finished products.
Vacuum casting usually produces a main form that is more developed. Additionally, models produced via lithography may be used, as is the case for applications involving prototyping. It uses a master template that has a specific size and shape. This guarantees that errors won’t carry over to the program’s prototype form. The fundamental representation of the hard process is split in half by silicone rubber. A mold is heated to high temperatures to make sure that the two portions adhere to one another. This strengthens the shape and increases its lifespan.
Then the mold created is sliced away once it has hardened to reveal a central hollow that is precisely the right size to hold the model’s core. After cutting the mold in half, it is inserted into the cavity. There usually are several chemicals and parts in such a product. Carefully selected materials are used to create the resin filler. Resin imitates the properties of artificial materials. Resins are frequently combined with other powders or pigments to create products with decorative or practical features.
The cavity is filled with resin before the mold is placed there. The mold is then vacuumed to make sure there aren’t any air bubbles inside. This avoids damage or spoilage to the end product. The finisher places the resin in an oven for the last stage of curing. To ensure the durability and strength of the material, the mold has been thermally reinforced. Save the silicone cover from the mold so you can reuse it for upcoming designs.
Applications
Vacuum molding is a less expensive option to traditional injection molding that can be used to create intricate and delicate products. Due to its high production quality, die casting is used in the commercial product manufacturing industry.
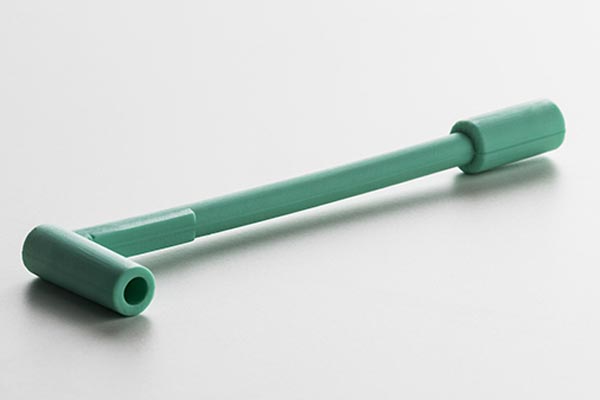
Vacuum casting of silicone
These are just a few of the produces that employ castings
Plastic Industries
Pens, sunglasses and other accessories, cosmetic containers, combs, brushes, and other items are made through vacuum casting.
Food and beverage industry
Bags for food and drinks, napkins, bottles, cans, cups, and others are all produced using vacuum forming. Due to its high production speed and process efficiency, hot casting is frequently used since rapid manufacturing plays a crucial component in many industries.
Electronic Industries
The material polyurethane resists heat. Therefore, polyurethane and molding are the best coating methods for electronic equipment.
Making rigid or flexible pieces with vacuum casting is an excellent way to produce high-quality prototypes, functional tests, concept proofs, and display demos. Depending on the need, urethane casting components can be produced in quantities ranging from a few to hundreds.