The production sectors have witnessed a significant shift in recent years, companies now can create complex and intricate geometries partly thanks to liquid silicone rubber molding. Liquid silicones rubber molding has been around since the 1970s and has become the go-to technique when it comes to the production of rubber parts and products.
LSR has distinctive qualities compared to other manufacturing techniques hence the reason why it’s used in thousands of industrial applications to make crucial parts and equipment such as electronics, aerospace, industrial markets, infant care, automotive, medical equipment just to mention a few.
LSR is best suited for long-run and short-run parts production making it ideal for both prototype and large-scale production. Stay tuned to know more about LSR.
Traits and characteristics of liquid silicone rubber molding
For decades, LSR has been the choice for a lot of manufacturers owing to the benefits that come with it. LSR is mostly used to create rubber parts owing to the manufacturability of its raw-materials.
The injection molding of LSR will provide your business with enhanced productivity, consistency of part quality, high-volume molding, and quick and seamless processing. LSR is slowly becoming the ideal technique for demanding applications due to its exceptional and unique properties.
Biocompatibility
Under intense testing and experimentation, LSR has shown traits of superior compatibility compared to body fluids and human tissue. When compared to elastomers, LSR is completely resistant to bacterial growth, thus it won’t corrode or stain other materials.
LSR is odorless and tasteless which allows for easy formulation in compliance with FDA requirements. LSR materials can be sterilized using a wide range of methods such as e-beam, gamma, ethylene oxide, autoclaving.
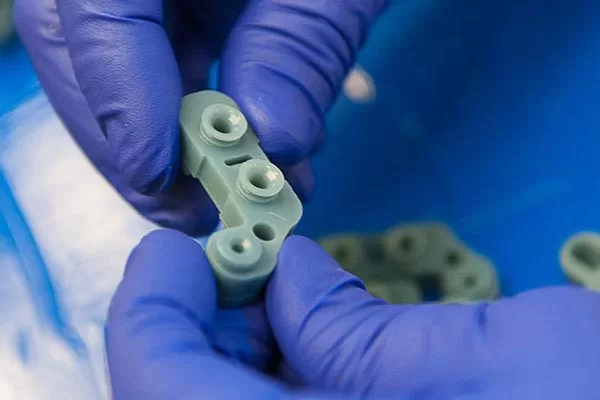
Silicone injection molding parts
Durability
LSR parts and products have the ability to withstand high temperatures, this makes it suitable to create automotive parts and products. Parts and products fabricated from LSR will not melt and are fire-retardant making it much-more superior to plastic injection molding.
Chemical resistance
LSR components are resistant to chemical solutions such as alkali and acids as well as water or oxidation.
Temperature resistance
When compared to other types of elastomers, LSR can withstand low and high temperatures.
Pigmentation and transparency
LSR has traits of natural transparency, this allows for the production of custom and powerful molded products
Benefits of liquid silicone rubber molding
Some of the benefits that come with liquid silicone rubber molding include:
Limited chances of contamination
The LSR process occurs in a closed system, this will significantly reduce the chances of contamination as the operator will not physically handle the material thus it’s not exposed to the outside environment.
A high degree of automation
The entire LSR is very tasking and labor-intensive, a fact that makes it difficult to be done manually. For this reason, the entire operation is automated allowing for a higher degree of accuracy and precision.
The LSR fabrication process provides you with cost-effective solutions when it comes to the creation of complex and intricate parts, it will help turn your ideas into reality.