Planning is essential to success if you want to mold complex products or parts when you’re in the race to disrupt an industry. LSR molding can give the most definite advantage over any other traditional plastic resin. One specific trait is the topic of this blog and is silicone’s ability to use undercuts. Undercut designs come in multiple shapes, sizes, and complexities, allowing various features.
The undercut feature is something used to connect an undercut component to another. This allows the part to be attached to a printed circuit board (PCB). It’s helpful to bridge channels or grooves since these are some of the most frequently used features. With LSR molding, undercut designs are useful in sections where you can’t use pull-through tabs or spigots. If you look for a workaround for “spigots,” you’ll find these are pushed or pulled through an opening in the printed circuit board so they can be aligned and secure to the keypad on the panel.
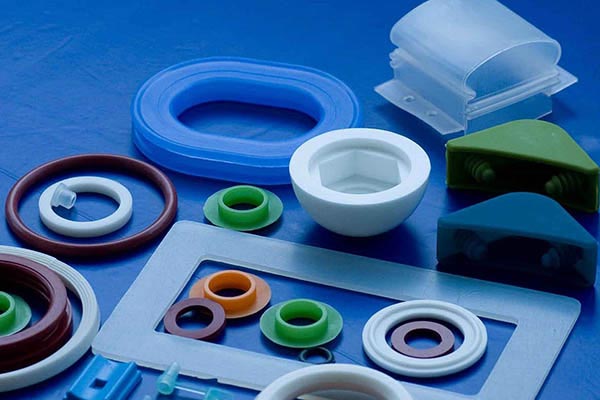
High quality lsr parts
Undercuts Help You Get a Streamlined Build
To get a cleaner product finish, you should know that a proper undercut design can help eliminate these needs. This is not exactly a shortcut or an oversimplification of the basic structure since a good undercut can give you enhanced protection for specific vital components against certain environmental hazards such as moisture, dusting, and other harmful conditions. Think of it as a new layer of shielding used to make your product more durable, especially if it has circuitry.
Undercuts, as you can find in traditional plastic molding, usually interfere with the removal procedure of the product from the mold after it’s curated. That’s why you must avoid undercuts during the design process of the mold. Silicone rubber takes away this setback by being much more malleable. If the undercut section is in the way, quick manual machining can help you eliminate it. The manufacturing process becomes more seamless and easier to handle since you have room to maneuver.
LSR molding Gives you the Best of Silicone
Silicone can stretch thanks to its high tear-strength properties and its elasticity, every single part you create over the undercut areas as you eject them from the mold. Don’t worry about losing shape in your product. Silicone doesn’t deform and retains the size and shape of the part. If you plan the whole manufacturing build thoroughly, any undercuts can add to the design features of the finished components. This could not happen if you work with any other type of resin. You can choose mounting features such as the ones used for custom silicone keypads. You can also manage channels and grooves for customized windows displays.
Choosing the right vendor is always helpful when dealing with these drawbacks. Make sure your vendor has the right expertise in the manufacturing industry to deal with undercuts in your products, especially when tight tolerances are required. An expert on LSR molding has all the tools he needs in their workshop to get you the product just as you need it.