DFM involves a design optimization process used in the rapid prototyping phases of product development. It examines the design to ensure it’s cost-effective and easy to manufacture. Silicone molding is a popular rapid prototyping and manufacturing process that benefits from implementing DFM principles in the design stage.
DFM simplifies the design by integrating standard components to increase production efficiency and enhance quality. The process significantly impacts project success and varies between production methods used, such as silicon vs. plastic molding.
Why Is a Design for Manufacturing (DFM) Report Important for Silicone Mold Manufacturing?
The Design for Manufacturing (DFM) report is a crucial analysis for new molding projects. It assists manufacturers with identifying issues in the prototyping stage that may affect mass manufacturing processes. When designing and constructing new molds, it serves a similar role to the (MAR) Moldflow Analysis Report.
This report saves manufacturers and their clients money and time. It’s more cost-effective to make changes to the design in the prototyping stage than when the product is undergoing mass manufacturing.
The DFM report analysis features a detailed inspection of the prototype design and manufacturing process, identifying the following issues.
- Features that are challenging or impractical to manufacture.
- Conflicts involving materials used in the prototype/product design and production.
- Unreliable and inefficient assembly processes.
- Production quality problems.
- Cost-saving ideas and opportunities.
- Impractical draft angles that cause issues with the removal of parts from the mold.
- Non-uniform wall thicknesses that cause defects or warping of products.
- Undercuts that add complexity and cost to mold design and construction.
Typically, DFM report analysis assists with identifying compatibility between the prototype design and manufacturing process, ensuring the prototype and product meet the required quality standards. It also improves yield rate and minimizes production cycle times to increase profitability and quality.
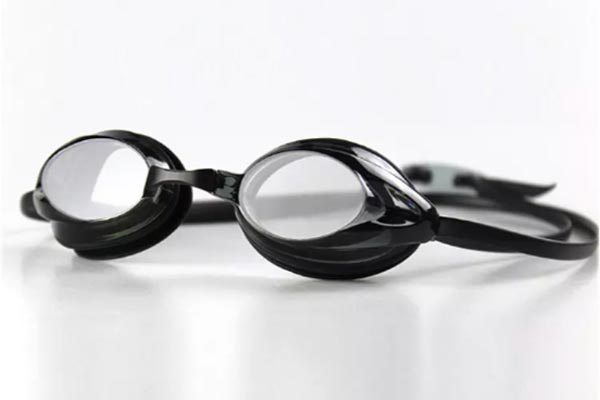
Silicone swim glasses
DFM Reports Assist with Avoiding the Following Manufacturing Problems
With companies continually offshoring manufacturing projects, it’s challenging to coordinate collaboration between design and production teams. So, DFM report analysis bridges the gaps in on-site design and manufacturing of prototypes/products.
The company can design prototypes and send them to manufacturing partners for DFM analysis, creating a conduit for the effective design of the prototype/product. This strategy ensures efficient design and manufacturing to meet project goals regarding design, quality, production efficiency, and outcomes.
This collaboration in the project development phase allows teams to uncover problems before they become an issue in the mass production phase. Design companies and manufacturing partners must conduct a DFM report analysis for all components before undertaking mold design and manufacturing.
Implementing this strategy ensures higher success rates for prototyping projects, reducing costs and time wasted on producing molds and components that don’t meet desired project parameters.
It eliminates frustration and assists with keeping project timelines on track.
DFM Silicon Mold Design Rules
Liquid silicone injection molding is different from thermoplastic injection molding, requiring an independent DFM analysis to ensure project success. One of the benefits of liquid silicone molding over thermoplastic methods is its simplicity due to the flexible mold.
This feature of silicone molding eliminates the requirement for design teams to consider the location of ejector pins. The components are manually lifted from the mold, allowing mold design to be more tolerant of looser design with draft angles.
The shear-thinning properties of liquid silicone permit it to flow freely in all mold sections. These material properties eliminate the need for consistent wall thickness, with silicone parts capable of thicker wall thicknesses than thermoplastic components.
Another interesting quality of silicone injection molding is its ability to feature protruding undercuts. Since the material is pliable and soft, the irregular protrusion of components makes it easy for manufacturers to drag them from the mold without the need for side action.
The viscosity of silicone liquid material means it may leak on the separating line of the mold if the manufacturer doesn’t properly seal it. This is a common restriction in liquid silicone injection molding. Manufacturers can mitigate this issue by correctly sealing the mold.
In Closing – General Rules in DFM Reports & Silicone Mold Manufacturing
DFM reports create insights into silicone mold design to optimize mold manufacturing, ensuring effective component production from the get-go. The DFM report can identify the following principles in mold design to optimize prototyping and production.
- The requirement to shorten mold parting lines and reduce flash.
- The correct draft for parts.
- If there is a need to install gates on the underside of the mold or in areas where they aren’t visible.
- Issues with mixing and metering.
Liquid silicone requires a platinum catalyst in contrast to injection molding with thermoplastics. The manufacturer pumps these materials in consistent ratios via metering units, mixing them with dynamic or static mixers.
DFM reports in silicone molding assist manufacturers with optimizing these processes to ensure final components meet project requirements. As a result, the probability of success when moving to the manufacturing phase is higher.