There are many options to choose from when it comes to prototyping. There is CNC machining, 3D printing and then there is vacuum casting, which can be used as an independent technique or as a perfect complement to the two aforementioned processes.
Many articles have mentioned the reasons for using vacuum casting in rapid prototyping applications. Without the risk of being a broken record, let us answer the question once again of why vacuum casting is a preferred method in prototyping. It might tell you if the process is right for you.
What is Vacuum Casting?
In deciding whether vacuum casting is perfect for creating your prototype, you need to know the fundamental nature of how vacuum casting works. The process consists of several steps.
The vacuum casting process begins with creating the master copy using 3D printing, either by stereolithography (SLA) or selective laser sintering (SLA). You can also use CNC machining, which produces high-quality surface finishes.
This master model is cast in silicone. The part is placed in a vat and covered with liquid silicone. Once the silicone mold cures, it will harden and cut along specific lines to remove the master model. The cavity formed from removing the master copy serves as the mold that can be used to create the part.
In this prototyping technique, the casting process is completed under a vacuum. This ensures that all the air bubbles are gone from the cast resin, which results in high accuracy and dense parts. Once the resin is cured, the mold can be reused and made identical copies.
Vacuum casting is used in many rapid prototyping applications including prototyping, testing and validation, and creating small batches for early market products.
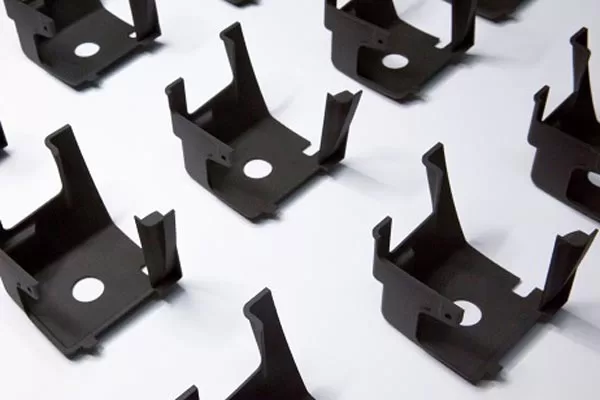
Vacuum casting products
Reasons for Choosing Vacuum Casting
Vacuum casting is a widely used technique in creating prototypes. Here are the reasons why product engineers and developers prefer this method.
Quality
The primary reason why vacuum casting is ideal for prototyping is its quality. In the beginning stage of the prototyping process, vacuum casting can produce identical parts and have the same quality throughout.
Another factor that contributes to its quality is the silicone molds. It can copy even the most intricate details of the master model, which makes it perfect for producing parts with a highly detailed design.
Choice of Materials
Vacuum casting is great for rapid prototyping because it accommodates a wide range of materials. While the material used in the master model is irrelevant, the silicone mold can accommodate different polymer resins including stiff plastic, transparent materials, flexible elastomers, and others.
Close Resemblance to the Final Part
The parts produced from vacuum casting have a high degree of accuracy and can use different materials to create a prototype that closely resembles the final part.
That means the vacuum-casted parts can be used for functional testing and validation. It can be used for fit testing as well, if the part is a component of a larger assembly. A great advantage for product developers is for quality assurance.
Quick Turnaround Time
Another reason why vacuum casting is a popular prototyping method is its quick turnaround time, especially for plastic parts. Compared to conventional methods like plastic injection molding where the tooling takes time, vacuum casting can save you time. It can speed up the product development process.
Silicone molds can be formed in a day and the casted parts can be rapidly produced in succession with the single mold. It can help you with production-grade prototypes.
Cost
Vacuum casting is an economical way of producing high-quality prototypes and small batches of finished parts,
First, vacuum casting does not require much energy like injection molding or CNC machining. The second reason is that the process itself is not expensive as the silicone molds cost lower than aluminum or steel molds. And finally, it is about the economy of scale. The parts produced with a single mold can produce up to 25 parts before the mold gets worn out.
Conclusion
Vacuum casting has plenty of benefits in rapid prototyping applications. With this technique, product developers can make prototypes for trials, marketing purposes, or functional testing.
If you want to find out more if vacuum casting is the right technique for your prototyping needs, do not hesitate to reach us at Nice Rapid.