The vacuum casting process has become popular in recent years as big and small businesses found plenty of benefits from using this technique. It is undoubtedly one of the quickest and most cost-effective means of making prototypes.
With the highly finished master models, the vacuum casting process can create multiple parts with the same high quality from the one-off piece. Only this time, the part is made in a material with better qualities.
Vacuum casting or otherwise known as urethane casting is an ideal process for prototyping and running final parts in a small volume. It is a versatile process that is often overlooked because many are not familiar with it.
In this article, we are taking an in-depth look at vacuum casting and why you should consider this manufacturing method.
What is Vacuum Casting?
The vacuum casting process is labor-intensive, but still, it has a fast turnaround time. Its first step involves creating the master model via CNC or SLS. This part is hand-finished to create the desired surface.
After creating the master pattern, it will be suspended on a container and filled with silicone until it hardens. Then this master model is removed to leave a cavity that will serve as a mold. When the mold is ready to cast a part, the desired material is poured and cured in a vacuum.
You can reuse this mold not more than twenty times. But since it is soft tooling you can have a lot of flashes and may require finishing.
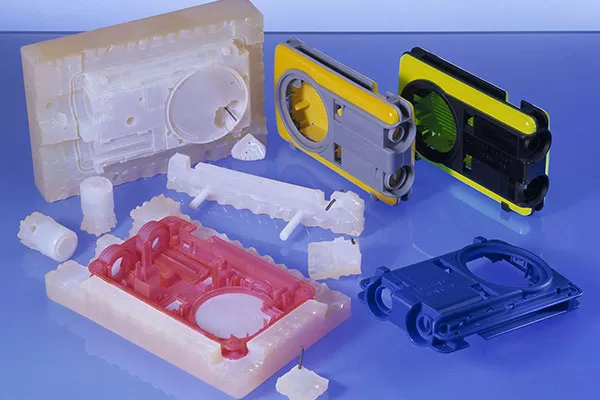
Vacuum casting products
Reasons for Choosing Vacuum Casting
Here are the advantages that vacuum casting presents when you choose to create your prototype models.
Functional Benefits
When it comes to functionality, you can rely on vacuum casting for plenty of that. The silicone materials used in vacuum casting are fire, electric, and shock-resistant. It can also create different shapes with varying thicknesses. It can form difficult shapes most quickly and reliably.
Aesthetic Benefits
With regards to aesthetics, vacuum casting can create parts with high-fidelity to the original. It can also offer plenty of finishing options, including the addition of colors during its manufacturing process. Adding the colors with the resin ensures that the final product will get the desired color. You can also use different finishes like gold or marble that are not your typical colors.
Multiple Applications
One of the main reasons for the popularity of vacuum casting is its multiple applications in different industries. Aside from producing prototypes for consumer goods and marketing purposes, vacuum casting is vital to the medical and aerospace industry.
The automotive industry is also another industry that relies on this process for its prototypes. Aside from big businesses, the process is popular among interior designers to create decorative pieces in small quantities.
Accuracy and Speed
Another benefit of using the vacuum casting method is its accuracy and speed in finishing the part. It is advantageous for companies who need to design and create prototypes fast.
Vacuum casting is also popular because of the cost. This is applicable for one-off prototypes, and short production runs as you will only pay for a fraction of the cost of other methods like plastic injection molding.