Tolerance is critical in the design stage when you’re checking rapid prototyping services. Tolerance is defined as the planned deviation from the exact measurements of the part you’re creating. It needs to be precise and handle values most efficiently. The value of your product and the project’s success depends on it. In this blog, we are studying how it works.
You can see tolerance values on CAD files expressed with +/- for millimeters. A good project manager must clearly understand the measurements required in critical areas of the planned product. High tolerance levels for the full product are not a good trait. You need to have inflection points to prevent performance issues.
ISO Regulations and Points of Tolerance
One of the reasons to treat tolerance with such importance comes from the ISO quality standards regulating the creation of parts used for practical purposes. Regulation #2768-1 states all matters related to linear and angular dimensions. They also explain desired specs on radius and flatness for surfaces.
The ISO guidelines state that low tolerances induced in angular shapes must be 50 microns or 0.06 millimeters. For the untrained eye, offering caused tolerance to any part is a way to create faulty products, but such is not the case. All parts built with precise tolerance can perform following the designs and the functional features expected from them.
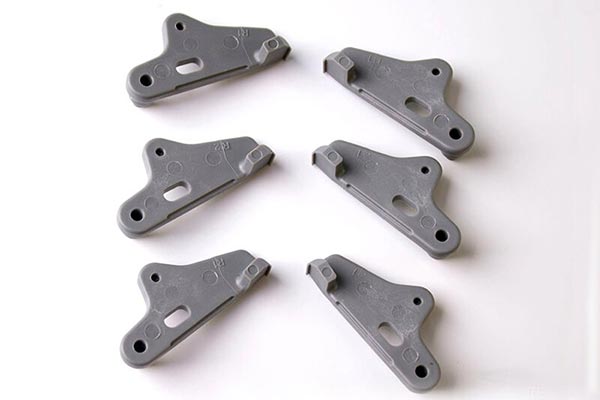
Rapid plastic prototyping
Secondary Effects of Tolerance
Induced tolerance also helps loosen tight features. Parts can never be 100% tight shut. Otherwise, their external surface can be affected by temperatures pretty easily. A super-tight screw can rearrange the shape of a finished product. Lack of mobility and exposure to vibrations wears off anything solid quickly.
Most parts need a good range of motion to make sure that parts can fit or be removed if necessary. Getting self-centered by chasing perfection means you’re bound to fail during performance. Keep in mind that rapid prototyping is beneficial, but it’s still science in development.
Tolerance Matters
Being flexible can help you go a long way. With this information, you can have a different approach for any project that hasn’t been tested well, even after using top-quality design. Keep in mind that not all issues are on the side of the equipment, especially when performance issues arise.
Make sure to follow the guidelines of the ISO norm #2768-1, and pay close attention to your design team. They know what they are doing; work with the in-house manufacturing team and be ready to make concessions. Most of the time, this flexibility will translate into improvements.